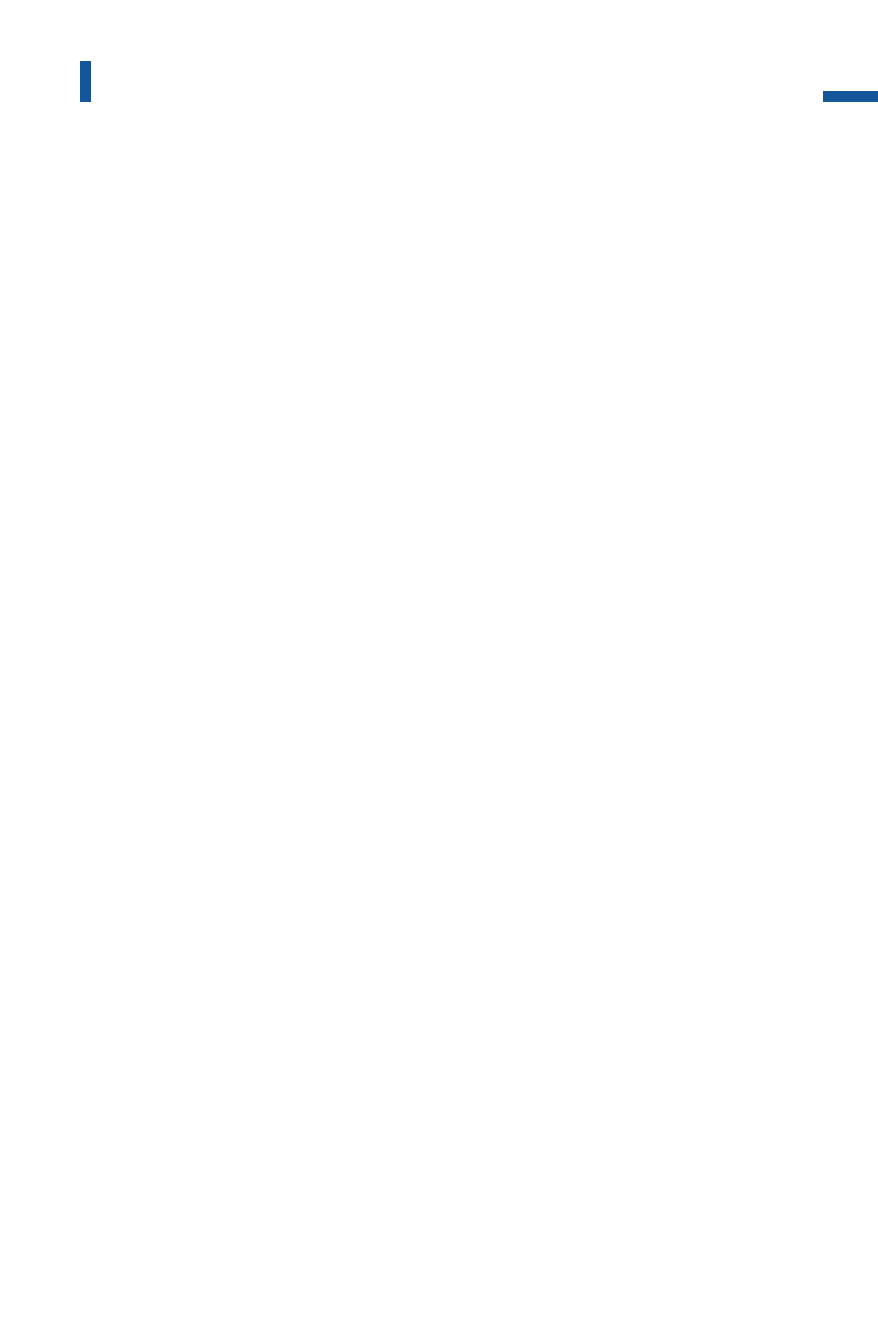
During the bending process, the web surface of the side member is
supported above the bed cushion by means of a support beam. By vary-
ing the bed cushion pressure levels, it is possible to influence the flat-
ness of the web surface, and in particular the rectangularity of the ribs.
A stripping device in the die ensures controlled stripping of the angled
side members from the bending punch. Parallel ejection is achieved
using the support beams.
Segmented bed cushion
As a result of the variable side member length, the cushions at the end
zones of the side members are only partially in use. A tilting moment
occurs here which must be balanced by means of stable gibs.
If all bed cushions are activated at the same time during the upstroke
of the slide for ejection, the cushions which have the smallest load reach
the top dead center first. However, the side members must be ejected in
parallel formation in order to avoid damage. There are two alternatives
here: to eject the side member while maintaining continuous contact
with the top die during the upstroke of the slide, or to control the syn-
chronous ejection speed of all the cushions. If side members are formed
with right-angled bends, different cushion strokes are required.
Control of parallelity and cylinder deactivation
The pistons of the cylinders that control parallelity are located at the
outside of the slide. During the working stroke, they operate against the
mean pressure of the servo valves (cf. Fig. 3.3.5). The off-center loading
of the dies generates a tilting moment on the slide. In the event of a
deviation from parallelity, the pressure is increased in the control cylin-
der that is on the loading side while pressure on the opposite side is
reduced. A supporting moment occurs which acts opposite to the tilt-
ing moment. In the case of side member tools, the off-center loading of
the slide can be large due to the arrangement of the individual mod-
ules. In some cases, tilting of the slide can no longer be prevented by
control of parallelity at a reasonable cost. In such cases, the control of
parallelism is supported by the selective deactivation of individual slide
cylinders (Fig. 4.4.14). As a result, the center of application of the press
force shifts in the direction of the forces generated in the dies. The larg-
er lever arms of the parallelism control force help to increase the
moment acting opposite to the off-center loading. However, deactiva-
tion of individual cylinders reduces the maximum available die force.
215
Sheet metal forming lines
Metal Forming Handbook / Schuler (c) Springer-Verlag Berlin Heidelberg 1998