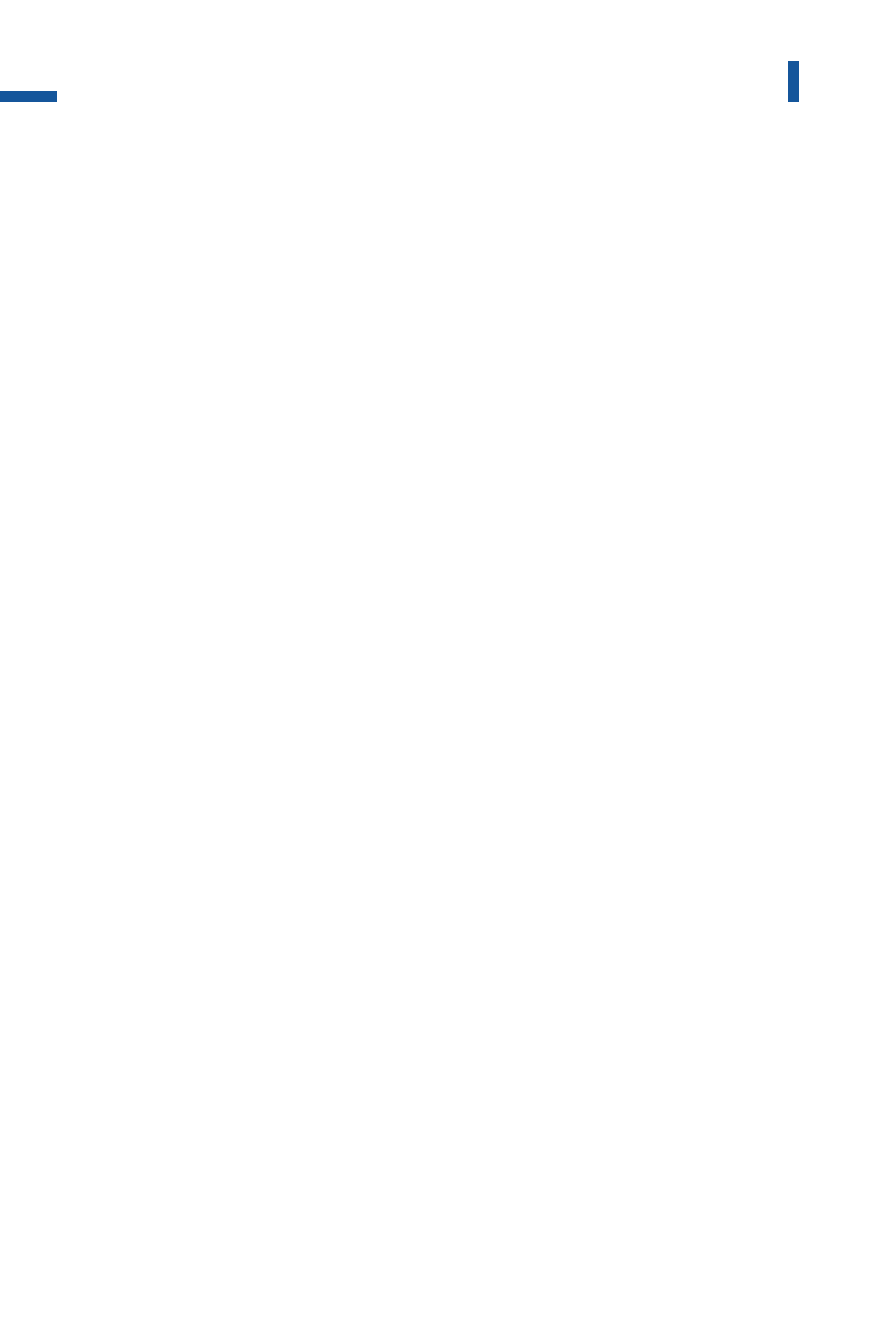
ing outside of the press upright, it is possible to choose between lateral
or longitudinal material feed to the press. Lateral coil feed offers the ben-
efit that the scrap web can be rolled into a coil again. The drawback here
is the greater space requirement of a lateral coil feed system. Generally
speaking, however, the space requirement of a transfer press is consider-
ably less than that of a press line; the lower space requirement also
serves to reduce ancillary costs.
Forming and blanking operations can be economically performed
both on mechanical and hydraulic transfer presses: blanking, initial
draw and subsequent drawing processes, contour pressing, calibration,
flat pressing, flanging, trimming, hole punching, etc. On the one hand,
even parts with extreme draw depths and complex or asymmetrical
shapes can be manufactured on transfer presses without any problems.
Horizontal wedge-driven cutting and forming tools are also used (cf.
Fig. 4.1.17).On the other hand, dies can often be simplified by making
most effective use of the existing number of stations. The number of die
stations within the die sets used does not necessarily need to be identi-
cal. Idle stations can easily be bypassed. Transfer presses with a large
number of die stations permit the production of two different parts
simultaneously provided the die sets are able to form the part on fewer
stations. In these cases, the blanks are fed synchronously to two differ-
ent points in the press.
The total nominal force and energy costs of transfer presses are gener-
ally lower than it is the case for individual interlinked presses. Operating
and maintenance costs are reduced to a single unit, and favorable con-
ditions are created for reducing production costs due to the elimination
of transport distances and intermediate stations.
Mechanical transfer presses
Mechanical transfer presses are built with two, three or four uprights.
Depending on the range of parts to be manufactured and the number
of stations, the presses are equipped with one, two or three indepen-
dently driven slides(Fig. 4.4.23). Each slide is designed individually to
satisfy the requirements for size, nominal force and stroke. In particular
for larger presses with different press force requirements at various
forming stations, this type of multiple upright construction offers
considerable advantages. It is customary in transfer presses to integrate
a draw cushion in the bed (cf. Fig. 3.1.11).A hydraulic overload system
230
Sheet metal forming and blanking
Metal Forming Handbook / Schuler (c) Springer-Verlag Berlin Heidelberg 1998