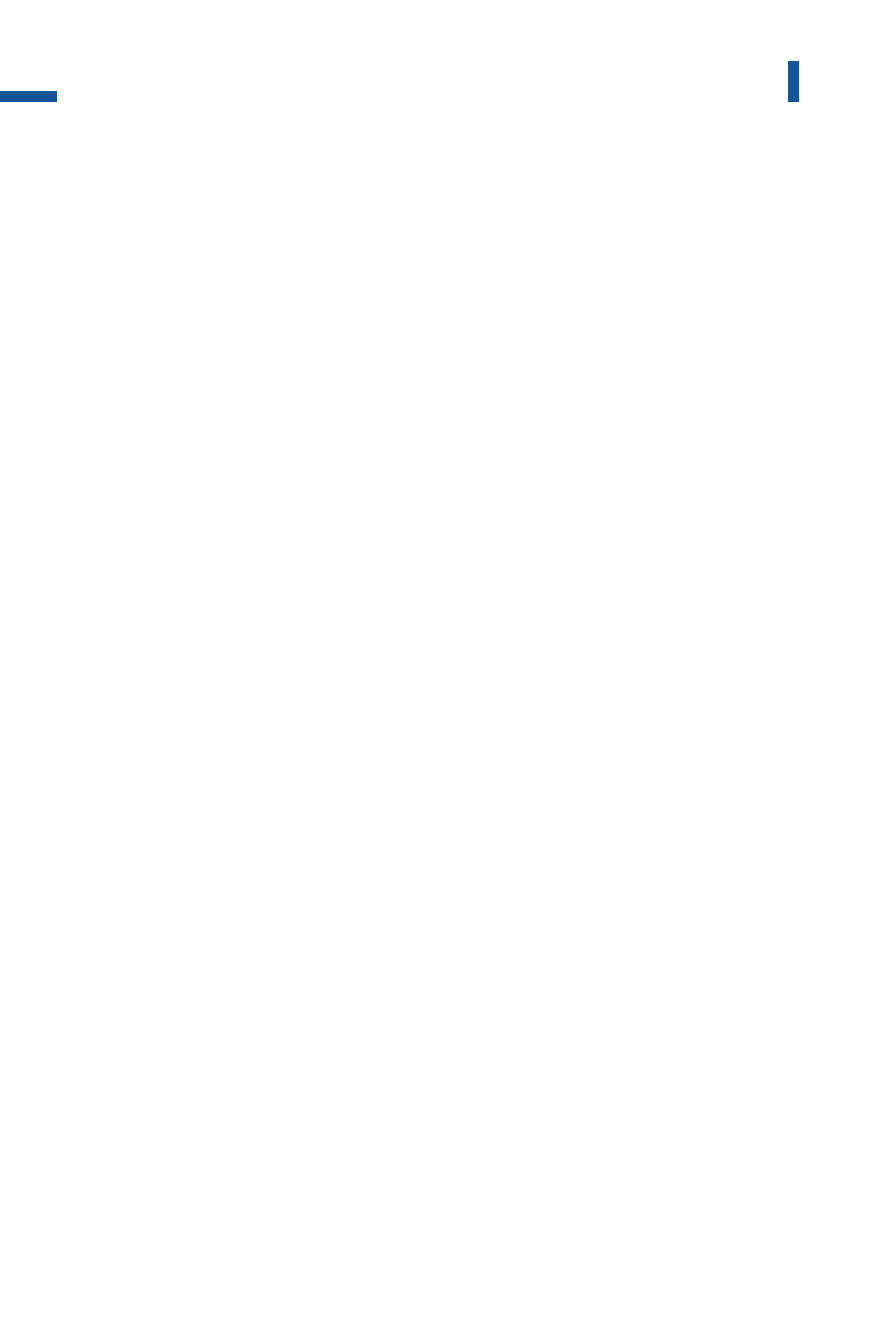
tions. The entire gripper rail system is then equipped with a lift stroke.
This principle, which is described in Sect. 4.4.7 “tri-axis transfer presses”,
is generally in the production of larger panels.
All three axes of the gripper rail drive systems are positively driven by
double cams. Configuration of the motion curves in accordance with
mathematical principles prevents jerky accelerations – in other words,
no centrifugal effects are created which would jeopardize reliable work-
piece transport. The distance between the gripper rails perpendicular to
the direction of transport can be adjusted infinitely or on a step-by-step
basis. In the case of parts with small dimensions, this eliminates the
need for long grippers and corresponding motion of large masses.
Hydraulic transfer presses
In the case of hydraulic transfer presses, an electrically driven gripper
rail system transports the workpieces from the destacker to the storage
location behind the press (Fig. 4.4.25).
The manufacture of parts using the counter drawing method is gener-
ally used only in hydraulic presses (Fig.4.4.26, cf. Fig.3.1.10and 4.2.4).
The drawing process is performed, generally in two stages, by active draw
cushions in the press bed followed by trimming and flanging of the edge.
The slide closes and displaces the blank holder while the two rear dies
form the edge. The slide reaches its bottom dead center when it makes
contact with mechanical stops. Only after this stage is reached, the parts
are drawn using the punches by switching over the drive pumps from
slide to bed cushion operation. The blanks are held at every die station
using the pre-selected force level acting from above. Once the forming
operation has been completed, the slide opens while the bed cushions
return to their starting positions. The advantage of this forming method
is that no tilting moment acts on the slide during the forming process, as
the two halves of the die set are resting on each other during the entire
drawing operation. Thus, it is possible to achieve a high standard of part
quality and also a favorable energy balance (cf. Sect. 3.3).
If the parts are produced in the transfer press using a single-acting sys-
tem with a draw cushion, large off-center loads can occur if drawing
forces come into effect in the first stations, e. g. in the front-most dies,
while the rear die stations have not yet been subjected to loading. This
situation leads to tilting of the slide, which can be compensated with the
aid of a hydraulic system controlling the slide parallelity (cf. Fig. 3.3.5).
232
Sheet metal forming and blanking
Metal Forming Handbook / Schuler (c) Springer-Verlag Berlin Heidelberg 1998