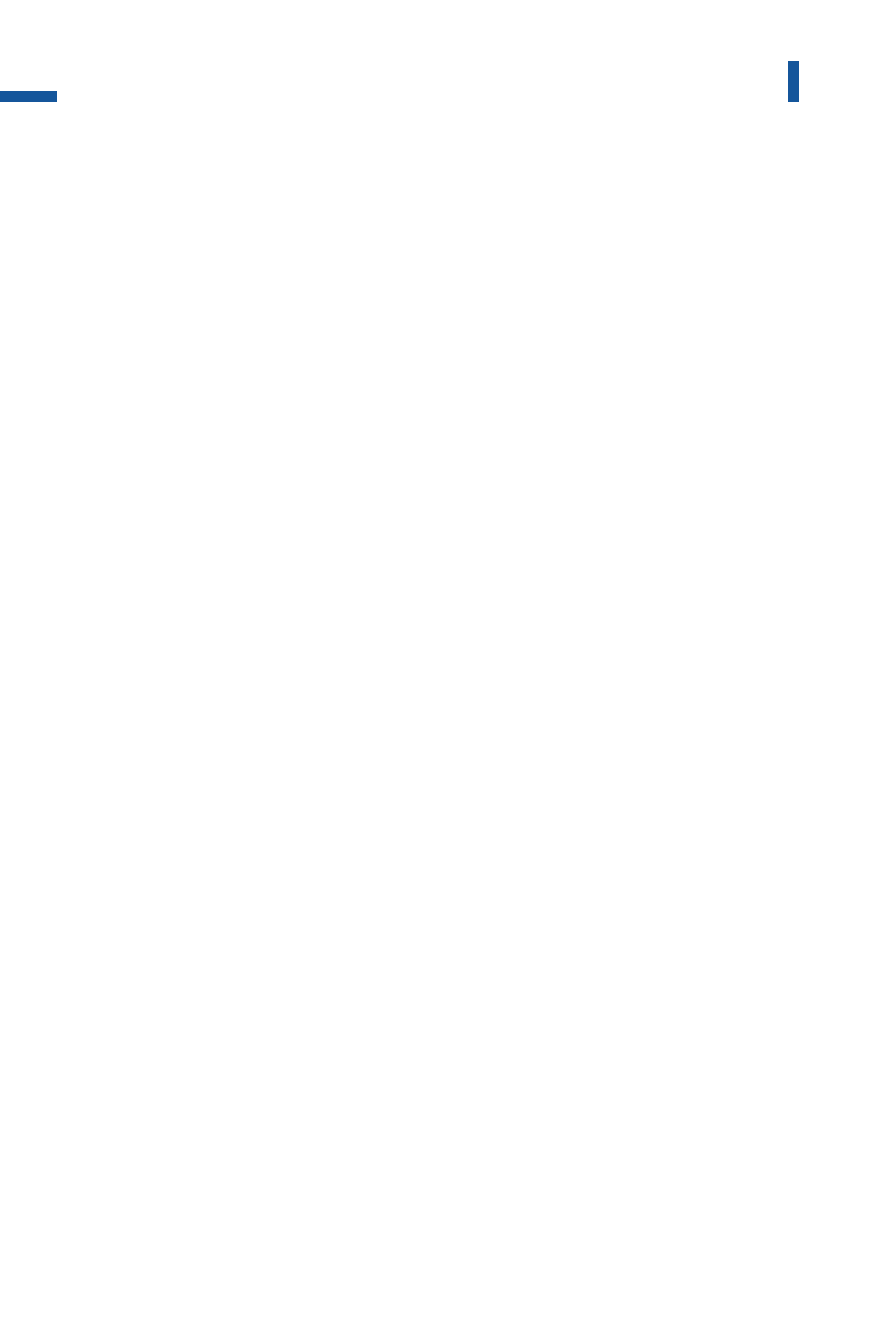
point “Error” in the menu line. Error messages contain an error number,
plain language, reference to the affected assembly (operating resources
identification) and reference to the point in the PLC program. This
information, in conjunction with the status displays, supports the
detection and localization of the source and cause of the malfunction.
Die-dependent data related to all dies used in the line can be entered
and edited at the visualization system. They are stored and managed in
the visualization system. During die change, this data is automatically
transmitted to the relevant control units.
Alongside the visualization system, which is imperative for line oper-
ation and monitoring, PC-based systems are also frequently used for
the acquisition and processing of machine and operational data as well
as measured values.
Machine and production data acquisition and evaluation
The machine and production data acquisition system (MDA/PDA) – or
PMS (Press Management System) for short – logs error and standstill
data as well as production data accumulated in the press line. As such,
it plays an important role in detecting and analysing weak points and
in registering and monitoring press line productivity.
The hardware basis of the PMS is an industrial PC which is directly
linked to the line’s control system. The central PLC is responsible for
making available the necessary data, and so functions as the communi-
cation partner for the PMS. Table 4.4.1 indicates the spheres of opera-
tion of a PMS for large-panel presses.
The field of machine data acquisition is subdivided according to the
acquisition and evaluation of errors and standstill periods.
According to the definition used here, errors are constituted by
machine statuses which are the direct result of faulty or damaged line
elements or components and which generally necessitate repair work.
Errors are automatically classified by the PMS. In addition, a freely con-
figured event-related comment is possible for each error message.
Errorsdo not, however, always cause a standstill; Standstills, in turn,
do not necessarily result in errors. As a result, alongside the detection of
errors, separate acquisition of all press standstill statuses is required.
Standstill,in accordance with the definition used here, consists of all
times during which no parts are produced (cf.Sect.4.9.2). Depending
on the line in question, a difference is made between approx. 30 differ-
262
Sheet metal forming and blanking
Metal Forming Handbook / Schuler (c) Springer-Verlag Berlin Heidelberg 1998