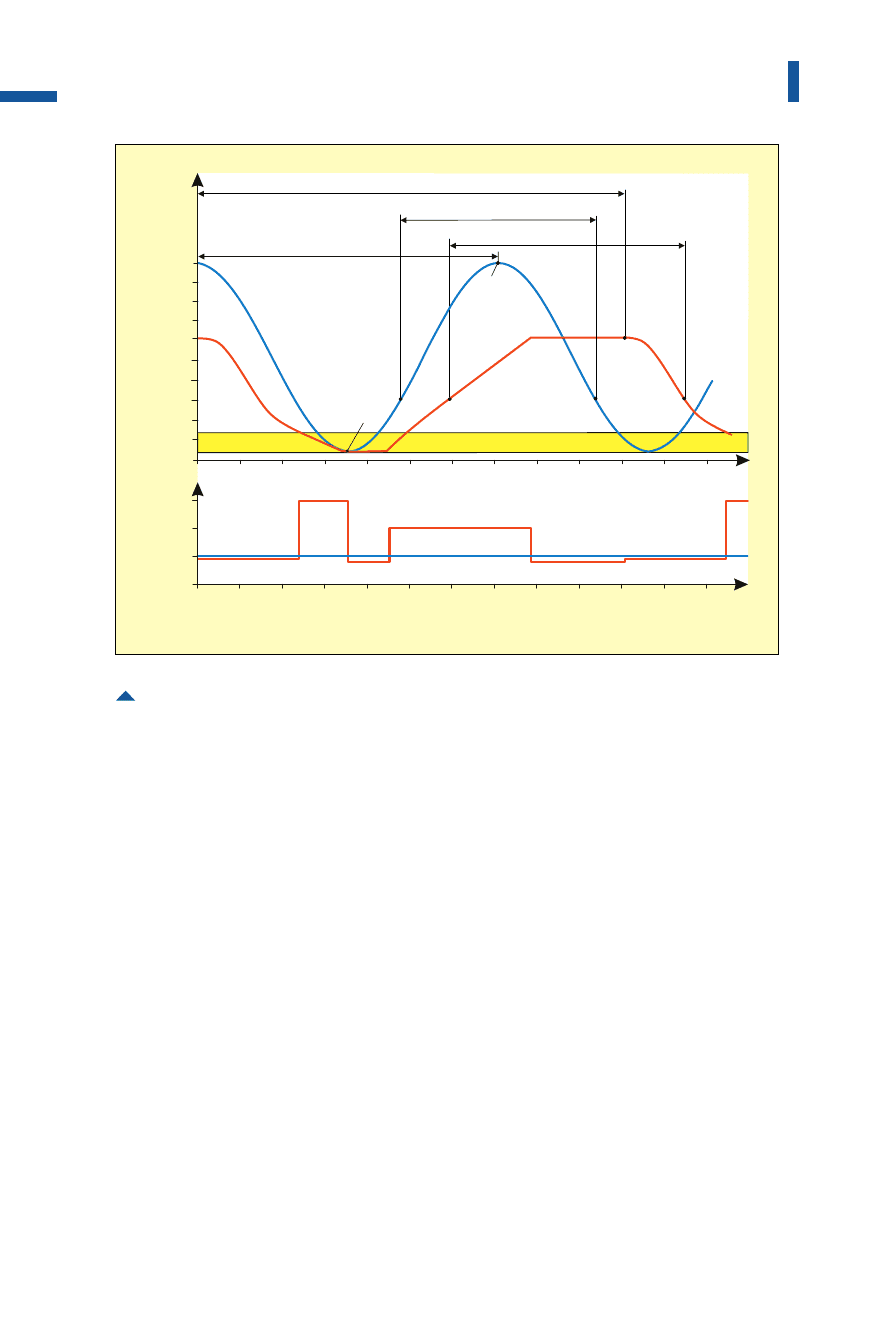
greater amount of energy is required for a work cycle, for example when
working with high drawing depths, the drop in flywheel speed must
not be more than 20% of the idle running speed. A constant supply of
energy for the drive motor is drawn from the electrical net. The energy
capacity of the drive motor is selected such that the motor can bring the
flywheel up to its idle speed after each working stroke. If the energy
requirement of both press types is compared, it becomes apparent that
hourly power requirement for mechanical presses can be some 30% low-
er than that of hydraulic presses despite their lower output. However, this
drawback can be compensated by changing the forming technology
used, for example through counter-drawing(cf. Fig. 3.1.10).
High-performance transfer presses
The high-performance transfer press is derived from a mechanical uni-
versal press with particularly high output, developed for high-precision
200
Sheet metal forming and blanking
Fig. 4.4.2 Slide displacement and power requirement versus time in mechanical and
hydraulic presses with cycle and transport times
hydr. cycle time approx. 5
s
transport time approx. 2,7
s
transport time approx. 2,4
s
hydraulic
press
forming area
hydraulic
press
eccentric
press
eccentric
press
TDC
BDC
mech. cycle time approx. 3,5
s
1000
900
800
700
600
500
400
300
200
100
0
300
200
100
0
displacement [mm]power requirement [kW]
time [s]
0 0,5 1,0 1,5 2,0 2,5 3,0 3,5 4,0 4,5 5,0 5,5 6,0
Metal Forming Handbook / Schuler (c) Springer-Verlag Berlin Heidelberg 1998