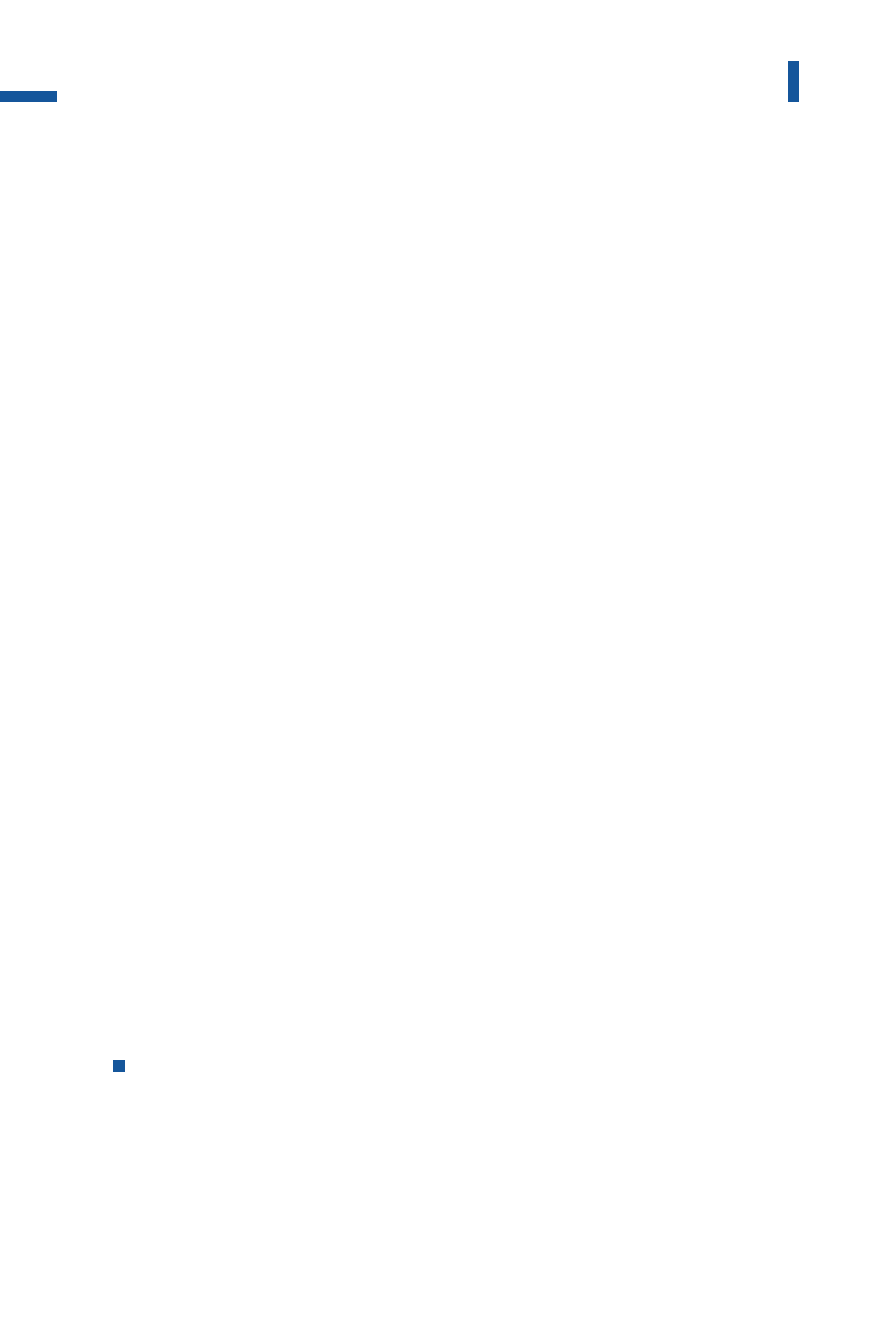
Hydro-mechanical deep drawing allows to achieve a significantly
larger draw ratio than that achievable in conventional drawing opera-
tions. Whilst the limiting drawing ratio using conventional technology
is b< 2.0, deep drawing ratio limits of up to 2.7 can be achieved in
hydro-mechanical deep drawing. Since no intermediate drawing and
annealing operations are required, very cost-effective forming is possi-
ble. The tool costs can also be reduced because of the reduction in the
number of necessary forming operations. Another notable benefit is the
quality of the surfaces of the drawn parts, as the sheet metal has not
been drawn over a rigid drawing edge but over a fluid bead. Costs for
finish processing operations such as polishing or grinding are substan-
tially reduced or often completely eliminated.
Due to the pressing of the blank against the punch which reduces the
amount of spring back, dimensionally accurate part production is pos-
sible. This is particularly important in reflector production, as not only
measurement tolerances but also optical qualities are tested. The thick-
ness of the sheet metal for hydro-mechanically deep drawn parts remains
consistent within narrow limits. This applies particularly to the small
reduction in thickness on the base radii, so that thinner blank can fre-
quently be used for forming the desired part.
Press force is higher in hydro-mechanical drawing than in other
forming methods using rigid tools, due to the reaction pressure in the
water container. Here, the slide force F
St
[kN] is the sum of the conven-
tional forming force F
U
[kN] and the reaction force F
Re
[kN], which acts
on the punch surface through the pressure medium (Fig. 4.2.11).
Depending upon the particular blank materials being processed, the
following pressures occur in the water container:
–aluminium: 50 – 200 bar
–steel: 200 – 600 bar
–stainless steel:300 – 1,000 bar
4.2.5Active hydro-mechanical drawing
Depending on their design, large-panel components for the automobile
industry such as hoods, roofs and doors possess only minimal buckling
strength in the center region of the parts. The reason for this is the low
188
Sheet metal forming and blanking
Metal Forming Handbook / Schuler (c) Springer-Verlag Berlin Heidelberg 1998