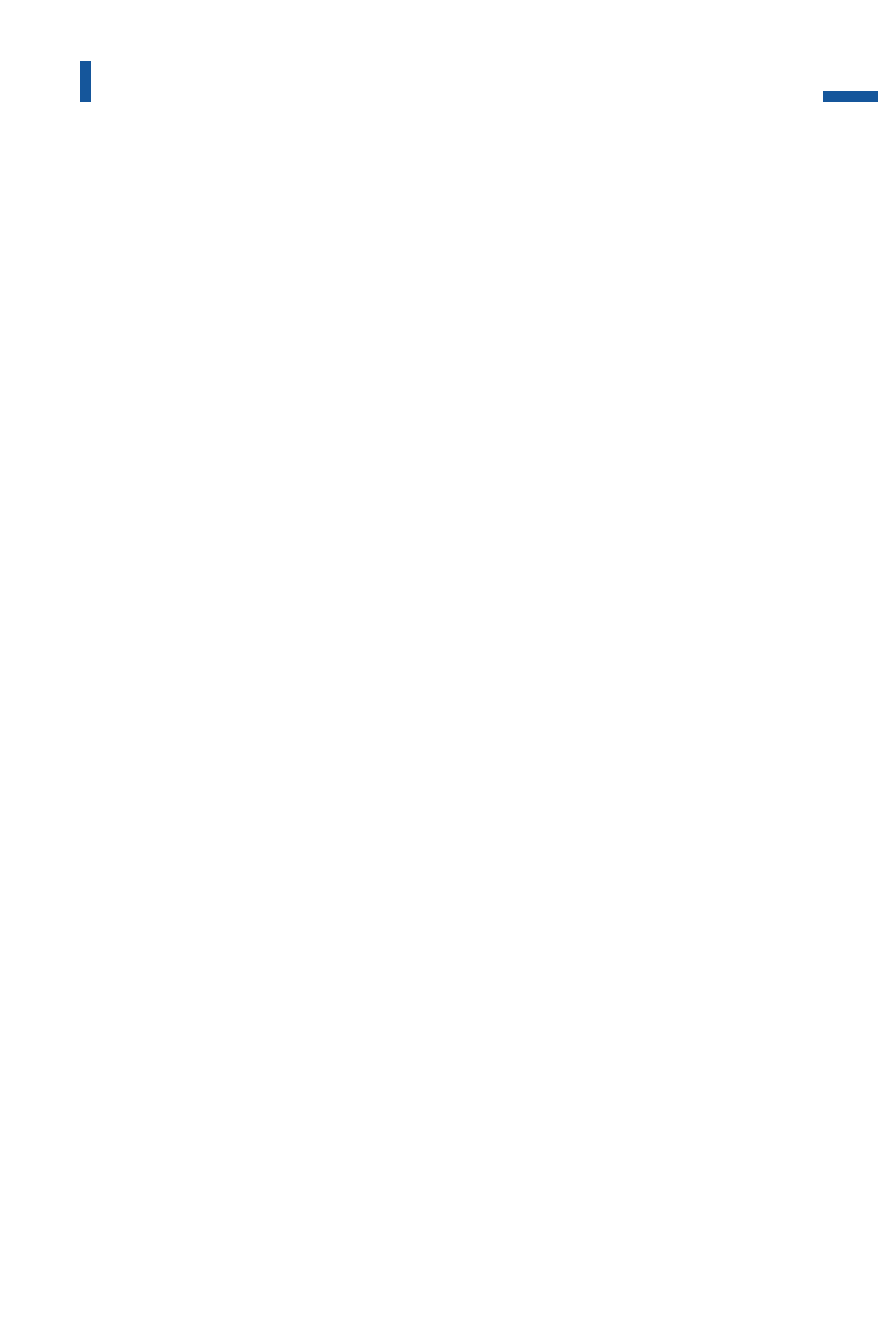
In double-action drawing operationsthe press has two slides acting from
above: the drawing slide with the draw punch and the blank holder slide
with the blank holder (Fig. 4.2.2and cf. Fig. 3.1.8). The blankholding slide
transfers the blankholding force via the blank holder onto the blank and
the draw die. The die and the ejector are located in the lower die on the
press bed. During forming, the blank holder brings the sheet metal into
contact against the die, the punch descends from above into the die and
shapes the part while the sheet metal can flow without any wrinkling out
of the blankholding area. In this case, the drawing process is carried out
with a fixed blank holder and moving punch. In double-action drawing
operations, the drawing slide can only apply a pressing force.
A disadvantage in double-action drawing is the fact that the parts for
further processing in successive forming and blanking dies need to
be rotated by 180°in an expensive and bulky rotating mechanism
(cf. Sect. 3.1.3). With outer body parts the danger exists, furthermore,
that the surface of the part may be damaged in the rotating operation.
Single-action drawing with a draw cushion works the other way round:
the forming force is exerted by the slide above through the die and
the blank holder onto the draw cushion in the press bed (Fig. 4.2.3and
cf. Fig 3.1.9). The draw punch and the blank holder of the drawing tool
are both located in a base plate on the press bed. Pressure pins, which
come up through the press bed and the base plate transfer the blank
holder force from the draw cushion onto the blank holder. The female
die and the ejector are mounted on the press slide. At the start of the
forming process the blank is held under pressure between the draw die
and the blank holder. The slide of the press pushes the blank holder
downwards over the draw die – against the upward-acting force of the
draw cushion. The part is formed via the downward movement of the
die over the stationary draw punch. The press slide must apply both the
pressing and the blank holder forces.
Thus, using a single-action tool, the part does not have to be rotated
after the drawing process. Furthermore, today the use of hydraulically
controlled draw cushions, even with deep drawing processes up to
depths of 250mm, produces a workpiece quality comparable to that of
double-action presses (cf. Sect. 3.1.4).
An energy-saving and cost-effective alternative in stamping is counter
drawing or reverse drawing(Fig.4.2.4and cf. Fig. 3.1.10). In this opera-
tion, once again, a single-action press with a draw cushion is used – nor-
159
Deep drawing and stretch drawing
Metal Forming Handbook / Schuler (c) Springer-Verlag Berlin Heidelberg 1998