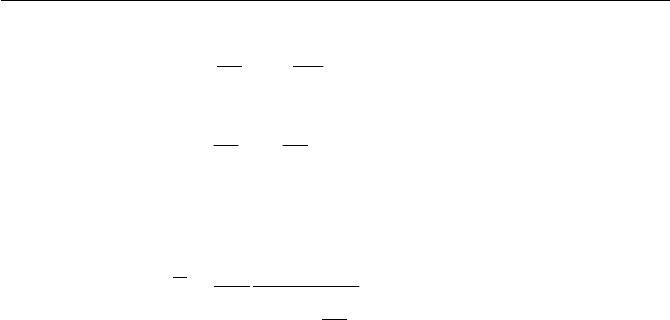
7 Non-Newtonian Fluid and Flow
¸
¸
¹
·
¨
¨
©
§
»
»
¼
º
«
«
¬
ª
¸
¸
¹
·
¨
¨
©
§
0
2
0
ln
ln
u
u
c
L
u
D
D
c
L
u
LL
L
L
E
H
(7.2.70)
c
is an experimental constant. Thus, from Eq. (7.2.62) and Eq. (7.2.70),
the apparent viscosity defined in Eq. (7.2.60) is readily calculated where
¸
¸
¹
·
¨
¨
©
§
0
2
0
0
ln
4
u
u
cD
F
u
L
L
e
S
K
(7.2.71)
In order to minimize the error and to achieve a more idealistic state to
validate Eq. (7.2.71), the filament can be extruded in isothermal cambers,
for example, Sampers and Leblans (1988).
Test fluids with higher fluidity and at higher elongational rate may be
tested for measuring the apparent elongational viscosity by using a pres-
sure-driven converging channel as illustrated in Fig. 7.13(b). The average
velocity increases monotonically as fluid particles move toward the apex.
There appears an elongational flow field, though we must aware of the fact
that there exists a boundary (shear) layer along the channel wall. To have a
well-defined elongational flow field in the channel, the upstream section of
the channel needs to be a tube with a large diameter
0
D relative to the
throat diameter
L
D . The entering flow also has to be moderate. The rela-
tive amount of a shear layer and an elongational core will depend on the
geometry of the channel, the volumetric flow rate and the fluid’s properties.
To minimize the presence of the shear layer, it has been proposed that the
channel walls may have to be lubricated with a relatively low viscosity
fluid (Hsu et al. 1980), although it is difficult to form a uniform layer of
lubricant along the channel wall.
Considering the elongational rheometer, an injection molding machine
is often used as a rheometer head. Cogswell (1978) derived an expression
for calculating an apparent elongational viscosity by using a die entry flow
field. See reference to Fig. 7.13(b) for a nomenclature in cylindrical coor-
dinates. The entry pressure drop
ent
p' is assumed to have two contributing
parts where
esent
ppp '' '
(7.2.72)
436