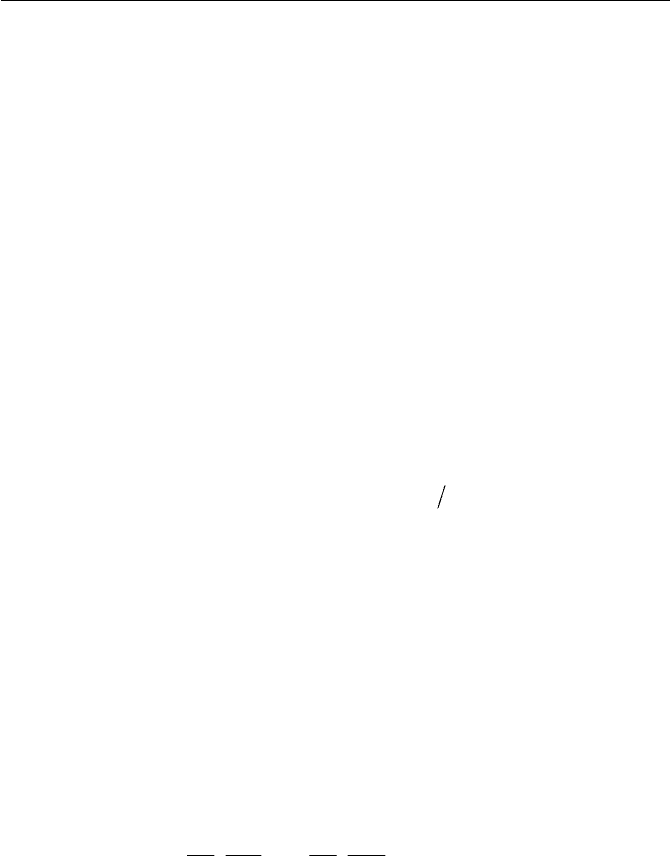
7.1 Non-Newtonian Fluids and Generalized Newtonian Fluid Flow
however, loses their time-independent rheological characteristics at extremely
high shearing and can behave in a totally different manner as expected.
(iii) Viscoelastic fluids
Consider a dynamic system, where one may take the stress
as a dy-
namic property and the strain
as a geometric property. For the sake of
simplicity, the system can be regarded as temperature independent and that
the response time is so short that the inertia effect would be negligible.
When a material exhibits such a way that there is a unique relationship be-
tween
and
, the material is called an elastic body (or elastic material).
If there is a linear relationship between
and
, we have
G
(7.1.10)
The material is said to be a linear elastic body (or linear elastic mate-
rial), where Eq. (7.1.10) is called Hooke’s law, where
G is the Young’s
modulus. In similar manner, as described in Eq. (7.1.1), when there is a
unique relationship between
and
, the material is called a viscous fluid.
If
is taken for the shear stress
xy
and
dtd
for the shear rate, we
can write the linear relationship of
and
for a Newtonian fluid where
(7.1.11)
is the viscosity (or coefficient of viscosity).
A viscoelastic material exhibits both elastic and viscous properties. The
constitutive equation is written for a viscoelastic material where
JJW
,f
(7.1.12)
However, for many realistic viscoelastic materials, including high molecu-
lar weight polymer materials, there is a complicated constitutive relation-
ship, which is generally written in the following functional form
0
2
2
2
2
¸
¹
·
¨
©
§
dt
d
dt
d
dt
d
dt
d
JJ
J
WW
WI
,,,,,
(7.1.13)
It must be kept in mind that
and
are to be treated vis a vis a tensor
quantity in general. Some details of viscoelastic fluids and flows are
treated in Section 7.3. Viscoelastic fluids under applied stress deform, but
when stress is removed, the stress inside the viscoelastic fluid does not
instantly vanish due to sustained stress by the internal molecular struc-
ture. This unique behavior is termed as the memory effect, which often
characterizes flows of the viscoelastic fluid. In order to gain a qualitative
405