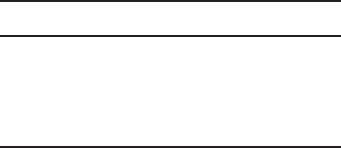
HEADWORKS AND PRELIMINARY TREATMENT 20-23
where H
L
headloss, m
Q flow rate through the screen, m
3
/ s
g acceleration due to gravity 9.81 m/s
2
C coefficient of discharge for the screen
A effective open area of submerged screen, m
2
A typical value of C for a clean screen is 0.6. Actual values of C and A depend on the screen
design. These factors include the size and milling of slots, or, in the case of wire, the diameter
and weave. The percent open area is of particular importance. The values must be determined
experi
mentally. They should be obtained from the manufacturer of the screen. Some typical fine
screen openings and effective open areas are listed in Table 20-8 .
A s with coarse sc reens, the important determination is the headloss during operation when
the screen is partially clogged. Many manufacturers re
commend that the screen be operated at a
condition of being blinded 50 to 70 percent to improve capture efficiency.
Screenings Handling. The amount of solid material collected by fine screens is considerably
greater than with coarse screens because of the the smaller sc reen openings. Capture rates are a
function of the sc
reen opening. Some examples are 87 to 93 percent for 3 mm band screens, 78
to 81 percent for 6 mm band screens. Other fine screens have similar relationships: 84 percent
for 3 mm and 71 to 76 percent for 6 mm (Makie and Oyler, 2007). A screw conveyor or belt
conveyor should be used to collect and transport the screenings to a was
her and compactor.
The design practice for treating and disposing of the screenings is discussed in Chapter 27.
20-5 COARSE SOLIDS REDUCTION
An alternative to capturing coarse solids on bar racks and/or screens is to use a mechanical device
to shred or grind the solids and return them to the flow. Three of the most common devices are
comminutors, macerators, and grinders.
There is a divergence of views on the d
esirability of using this technique for handling coarse
solids. One view is that the coarse solids should be removed from the wastewater early in the flow
scheme to eliminate downstream problems. Another view is that the shredded material is easily
handled by downstream processes
. Of particular concern are rag and plastic materials that form
strings or ropes that wrap around pump impellers, accumulate on clarifier mechanisms and air dif-
fusers, clog sludge pipelines, and foul heat exchangers. Plastic limits the potential for land applica-
tion of biosolids. For certain pro
cesses, such as membrane bioreactors (MBRs), or the requirement
to produce Class A biosolids, coarse solids reduction is not an option. Fine screens must be used.
TABLE 20-8
Fine-screen openings and effective open areas
Hole spacing, mm Open area, %
9 55
640
335
1 31
A dapted from Keller et al., 2006.