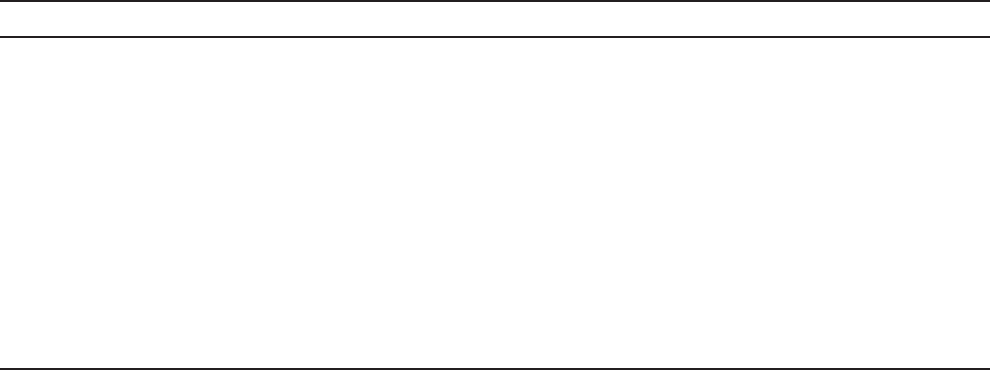
20-10 WATER AND WASTEWATER ENGINEERING
Bar Rack Cleaning Mechanisms
Although manually cleaned racks are often provided in bypass lines, mechanically cleaned
screens are typically used in the United States. These fall into four categories: chain-driven,
reciprocating rake, catenary, and continuous belt. These are illustrated in Figure 20-5 . Ad
van-
tages and disadvantages of each type are presented in Table 20-4 on page 20-12.
Chain-Driven. In general, front-cleaned, front-return chain-driven screens are more efficient in
retaining captured solids, but they are less rugged and are susceptible to jamming. They are seldom
used for plants receiving combined sewage. Back-c
leaned screens are more rugged but are more
susceptible to carryover of solids to the downstream side. Both types suffer from the disadvantage
of submerged sprockets that require frequent operator attention and are difficult to maintain.
Reciprocating Rake. The reciprocating rake or climber screens i mitate the motion of a person
raking the screen. They
are front cleaned, front return. Thus, they are effective in capture and
discharge of screenings without carryover. They have the advantage that all parts requiring main-
tenance are above the water line. The disadvantages are that a single rake may limit capacity to
handle high loadings of screenings, and they have a requirement for a high overhead clearance to
accommo
date the raking mechanism.
Catenary Screen. The catenary screen is a front-cleaned, front-return chain-driven screen. In
contrast to the chain-driven screens, it has no submerged sprockets. It can handle heavy objects.
It has a large footprint.
Continuous Belt. The continuous belt can handle both fine and coarse solids. It has no su
b-
merged sprocket.
Type Typical opening Typical use
Trash racks 40–150 mm To prevent logs, stumps, and large heavy debris from
entering treatment processes. Principally used in combined
sewers ahead of pumping units. In WWTPs, frequently
followed by coarse screens.
Bar rac
ks or coarse screens 6–75 mm To remove large solids, rags, and debris. Typically used
in WWTP.
Fine screens 1.5–6 mm To remove small solids. Typically follows a
coarse screen.
Very fine screens 0.25–1.5 mm To reduce suspended
solids to near primary treatment
level. Typically follow a coarse screen and/or fine screen.
May be used when downstream processes do not include
primary treatment.
Microscreens 1m–0.3 mm Used in conjunction with very fine screens for effluent
polishing.
TABLE 20-3
Nomenclature of racks and screens
Sources: Daukss, 2006, WEF, 1998.