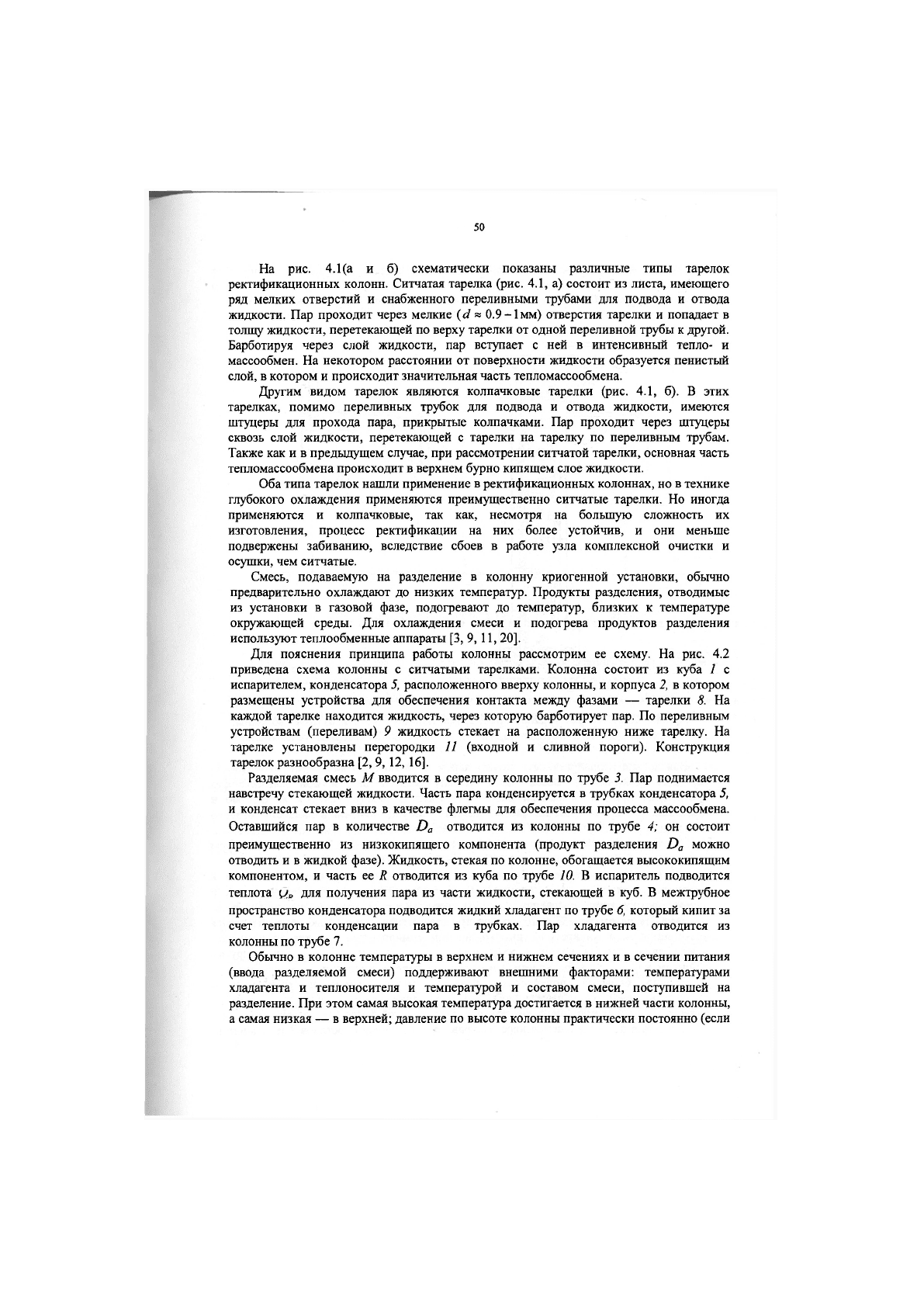
50
На рис.
4.1
(а и б) схематически показаны различные типы тарелок
ректификационных колонн. Ситчатая тарелка (рис. 4.1, а) состоит из листа, имеющего
ряд мелких отверстий и снабженного переливными трубами для подвода и отвода
жидкости. Пар проходит через мелкие (й? » 0.9-1мм) отверстия тарелки и попадает в
толщу жидкости, перетекающей по верху тарелки от одной переливной трубы к другой.
Барботируя через слой жидкости, пар вступает с ней в интенсивный тепло- и
массообмен. На некотором расстоянии от поверхности жидкости образуется пенистый
слой, в котором и происходит значительная часть тепломассообмена.
Другим видом тарелок являются колпачковые тарелки (рис. 4.1, б). В этих
тарелках, помимо переливных трубок для подвода и отвода жидкости, имеются
щтуцеры для прохода пара, прикрытые колпачками. Пар проходит через штуцеры
сквозь слой жидкости, перетекающей с тарелки на тарелку по переливным трубам.
Также как и в предьщущем случае, при рассмотрении ситчатой тарелки, основная часть
тепломассообмена происходит в верхнем бурно кипящем слое жидкости.
Оба типа тарелок нашли применение в ректификационных колоннах, но в технике
глубокого охлаждения применяются преимущественно ситчатые тарелки. Но иногда
применяются и колпачковые, так как, несмотря на большую сложность их
изготовления, процесс ректификации на них более устойчив, и они меньше
подвержены забиванию, вследствие сбоев в работе узла комплексной очистки и
осушки, чем ситчатые.
Смесь, подаваемую на разделение в колонну криогенной установки, обычно
предварительно охлаждают до низких температур. Продукты разделения, отводимые
из установки в газовой фазе, подогревают до температур, близких к температуре
окружающей среды. Для охлаждения смеси и подогрева продуктов разделения
используют теплообменные аппараты [3, 9, 11, 20].
Для пояснения принципа работы колонны рассмотрим ее схему. На рис. 4.2
приведена схема колонны с ситчатыми тарелками. Колонна состоит из куба 1 с
испарителем, конденсатора 5, расположенного вверху колонны, и корпуса 2, в котором
размещены устройства для обеспечения контакта между фазами — тарелки 8. На
каждой тарелке находится жидкость, через которую барботирует пар. По переливным
устройствам (переливам) 9 жидкость стекает на расположенную ниже тарелку. На
тарелке установлены перегородки 11 (входной и сливной пороги). Конструкция
тарелок разнообразна [2, 9,12,16].
Разделяемая смесь М вводится в середину колонны по трубе 3. Пар поднимается
навстречу стекающей жидкости. Часть пара конденсируется в трубках конденсатора 5,
и конденсат стекает вниз в качестве флегмы для обеспечения процесса массообмена.
Оставшийся пар в количестве Оа отводится из колонны по трубе 4; он состоит
преимущественно из низкокипящего компонента (продукт разделения Оа можно
отводить и в жидкой фазе). Жидкость, стекая по колонне, обогащается высококипящим
компонентом, и часть ее К отводится из куба по трубе 10. В испаритель подводится
теплота для получения пара из части жидкости, стекающей в куб. В межтрубное
пространство конденсатора подводится жидкий хладагент по трубе б, который кипит за
счет теплоты конденсации пара в трубках. Пар хладагента отводится из
колонны по трубе 7.
Обычно в колонне температуры в верхнем и нижнем сечениях и в сечении питания
(ввода разделяемой смеси) поддерживают внешними факторами: температурами
хладагента и теплоносителя и температурой и составом смеси, поступившей на
разделение. При этом самая высокая температура достигается в нижней части колонны,
а самая низкая — в верхней; давление по высоте колонны практически постоянно (если