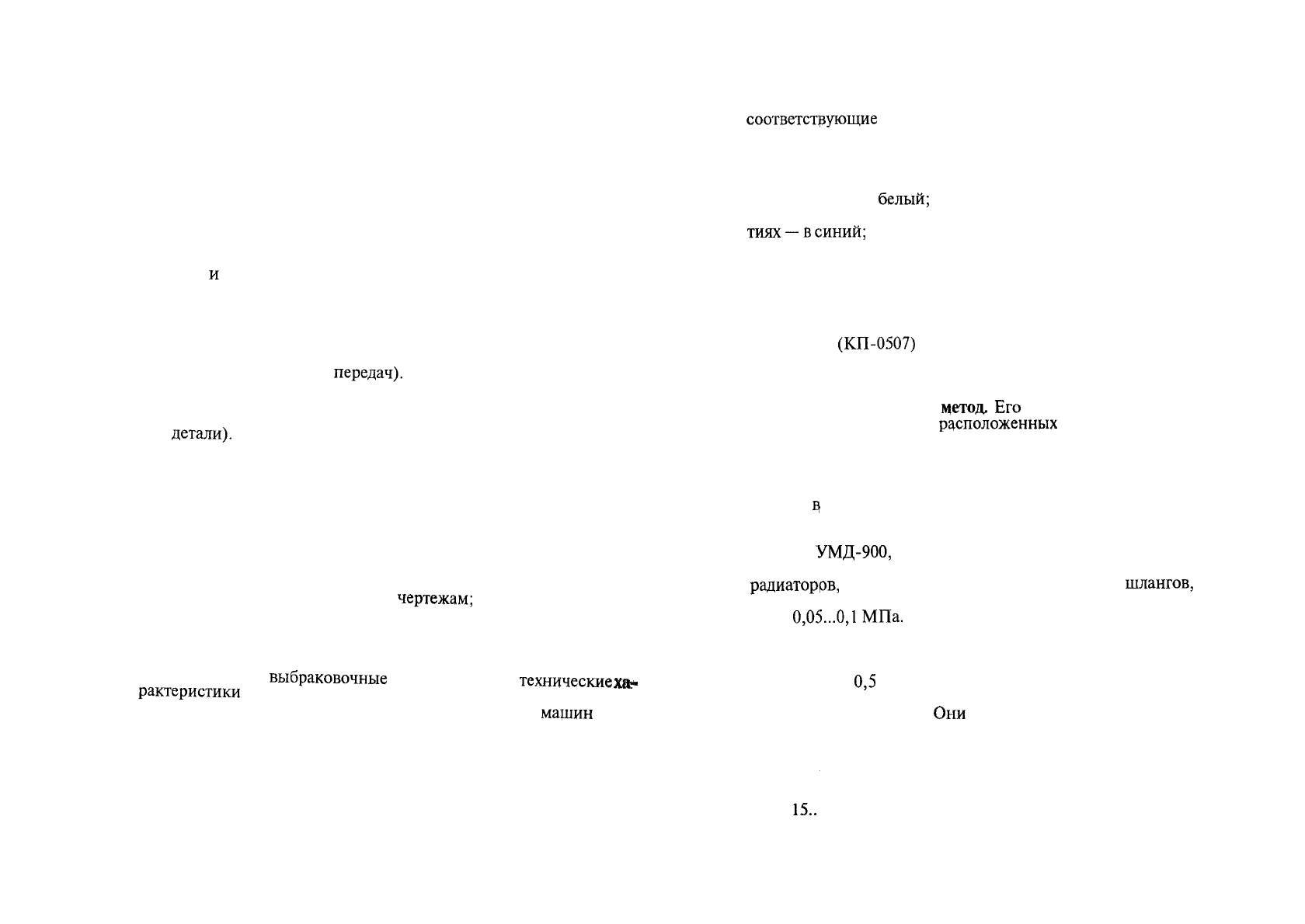
К третьей группе относят детали (коленчатые валы, поршневые
пальцы, вкладыши подшипников и т. д.), работающие в условиях
усталостного разрушения и одновременно подвергающиеся меха-
ническому или коррозионно-механическому изнашиванию.
Механические повреждения деталей. Трещины образуются в ре-
зультате воздействий значительных местных нагрузок, ударов и ус-
талостных напряжений. Они могут появляться в наиболее нагру-
женных местах рам, блоков, корпусов коробок передач и других
корпусных деталей. Трещины часто возникают в деталях из чугуна и
деталях, изготовленных из листового материала (крыльях, капотах,
облицовке и т. п.). Бывают трещины теплового происхождения.
Пробоины возникают в результате ударов других предметов о
поверхности тонкостенных деталей (в стенках блока цилиндров,
крыльев
и
т. п.).
Риски и задиры (ряд рисок) на рабочих поверхностях деталей
чаще всего образуются в результате загрязнения смазки или абра-
зивного действия чужеродных частиц.
Вследствие динамических ударных нагрузок возможно выкра-
шивание. Оно характерно для стальных цементованных деталей
(зубьев шестерен коробок
передач).
Его причиной служат усталост-
ные напряжения, возникающие, например, на беговых дорожках
колец шариковых подшипников.
Поломки и обломы образуются при сильных ударах о детали (ли-
тые
детали).
Изгибы и вмятины возникают в результате динамических нагру-
зок. При этом нарушается геометрическая форма деталей.
Химико-тепловые повреждения. Они приводят к короблению от
действия высоких температур, к коррозии поверхности детали из-за
химического и электрохимического воздействия окружающей и хи-
мически активной среды, к электрокоррозионным повреждениям в
результате искровых разрядов.
При ремонте различают следующие размеры деталей:
номинальные — размеры и другие технические характеристики
детали, соответствующие рабочим
чертежам;
допустимые — размеры и другие технические характеристики, с
которыми деталь может быть установлена на машину без ремонта и
будет удовлетворительно работать в течение всего предстоящего
межремонтного периода;
предельные —
выбраковочные
размеры и другие
технические
ха*
рактеристики
деталей.
Износ соединений сборочных единиц и агрегатов
мащин
опре-
деляют по изменению зазоров и функциональных характеристик
машин, а также по качеству их работы.
Поступающие на дефектацию детали для оценки их техническо- '
го состояния и возможности дальнейшей эксплуатации или необхо-
димости восстановления замеряют, проверяют и осматривают. Со-
ставляют ведомость на замену выбракованных деталей, которая
180
служит основным документом для дальнейшего проведения ремонт-
ных работ.
Детали разделяют на пять групп и маркируют окрашиванием в
соответструющие
цвета:
годные — в зеленый;
годные при соединении с новыми или восстановленными — в
желтый;
подлежащие ремонту в мастерской или на специализированном
предприятии — в
белый;
подлежащие ремонту только на специализированных предприя-
тиях—в
синий;
негодные (металлолом) — в красный.
С помощью универсальных измерительных инструментов (мик-
рометров, штангенциркулей, индикаторных нутромеров) и прибо-
ров (оптиметров, миниметров, инструментальных микроскопов)
определяют зазоры, натяги и т. д. Калибры и шаблоны служат для
контроля зубьев шестерен, размеров деталей и др. Специальными
приборами
(КП-0507)
и приспособлениями проверяют упругость
пружин, колец и т. д.
Для обнаружения скрытых дефектов используют следующие ме-
тоды.
Магнитно-порошковый
метод.
Его
используют для обнаружения
поверхностных и близко
расположенных
к поверхности трещин и
раковин в деталях машин.
Для обнаружения дефектов, перпендикулярных оси детали, про-
водят намагничивание в поле соленоида; дефектов, параллельных
оси детали, — циркулярное намагничивание; дефектов, располо-
женных
в,
различных направлениях, — комбинированное намагни-
чивание.
Для намагничивания деталей применяют универсальные дефек-
тоскопы
УМД-900,
77ПМД-ЗМ и др.
Пневматический способ. Он служит для проверки герметичности
радиаторрв,
топливных баков, топливопроводов,
шлангов,
шин и
т. п. Деталь погружают в ванну с водой и подают воздух под давле-
нием
0,05...0,1
МПа.
Гидравлический способ. Этот способ применяют при проверке
водяных рубашек блоков и головок блока, выпускных и впускных
коллекторов. Деталь устанавливают на стенд и заполняют водой
при давлении
0,5
МПа. По подтеканию воды определяют место тре-
щины.
Капиллярные методы.
Они
основаны на явлении проникновения
смачивающей жидкости в поверхностные трещины, поры и т. д.
Для выявления поверхностных трещин и пор в деталях, выпол-
ненных из немагнитных материалов, применяют люминесцентный
метод. Люминофоры, минеральные масла или кристаллические ве-
щества в виде порошка наносят на поверхность детали и выдержи-
вают
15..
,20 мин. Люминофор проникает в трещины. Детали осмат-
181