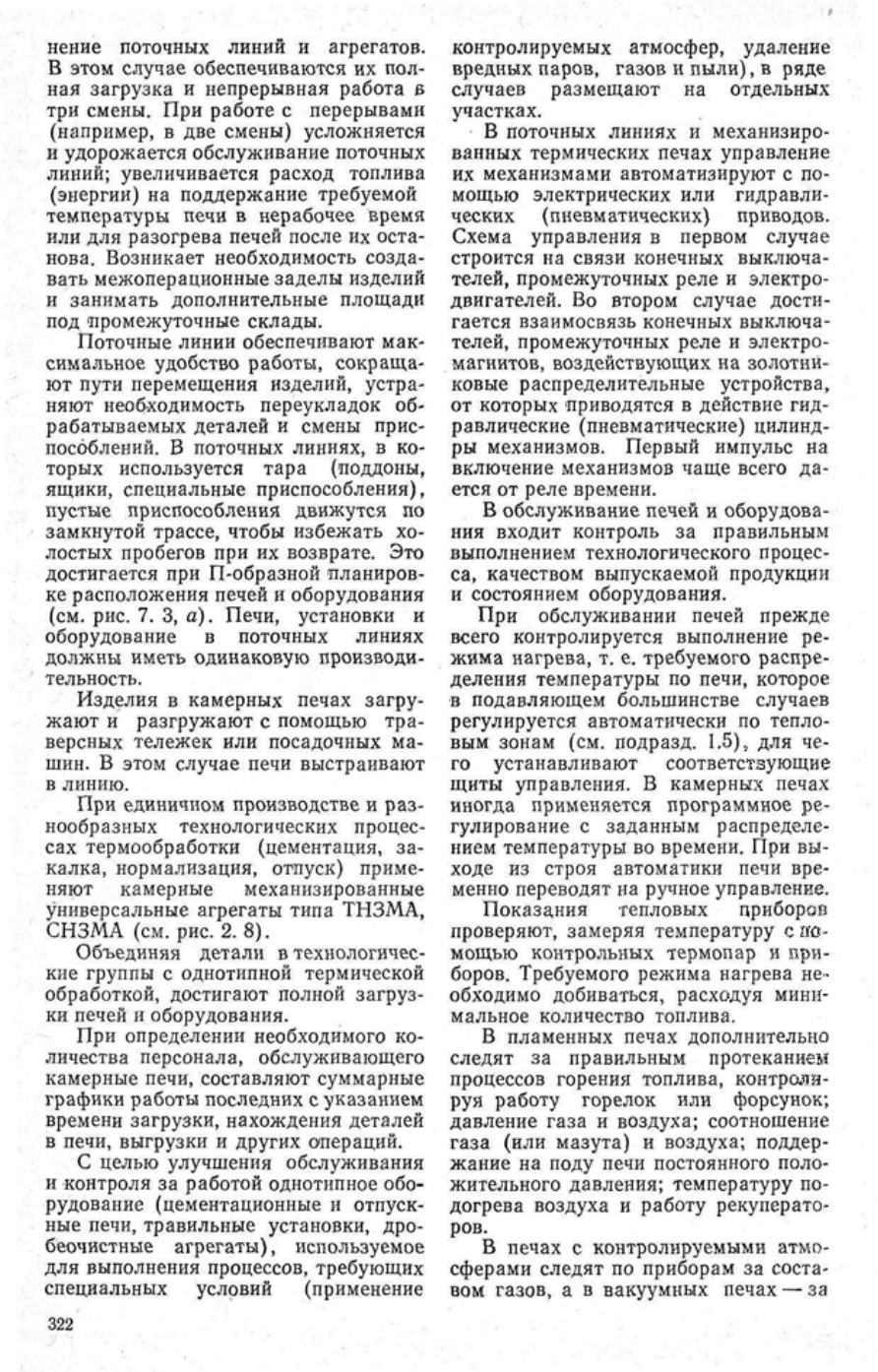
нение
поточных линий и агрегатов.
В этом
случае
обеспечиваются их пол-
ная
загрузка и непрерывная работа 6
три смены. При работе с перерывами
(например,
в две смены) усложняется
и
удорожается обслуживание поточных
линий;
увеличивается
расход
топлива
(энергии)
на поддержание требуемой
температуры печи в нерабочее время
или
для разогрева печей после их оста-
нова.
Возникает необходимость созда-
вать межоперационные заделы изделий
и
занимать дополнительные площади
под 'промежуточные склады.
Поточные
линии обеспечивают мак-
симальное
удобство
работы, сокраща-
ют пути перемещения изделий,
устра-
няют необходимость переукладок об-
рабатываемых деталей и смены прис-
пособлений.
Б поточных линиях, в ко-
торых используется тара (поддоны,
ящики,
специальные приспособления),
пустые приспособления движутся по
замкнутой трассе, чтобы избежать хо-
лостых пробегов при их возврате. Это
достигается при П-образной планиров-
ке
расположения печей и оборудования
(см-
рис. 7. 3, а). Печи, установки и
оборудование в поточных линиях
должны иметь одинаковую производи-
тельность.
Изделия
в камерных печах
загру-
жают и разгружают с помощью тра-
версных тележек или посадочных ма-
шин.
В этом
случае
печи выстраивают
в
линию.
При
единичном производстве и раз-
нообразных технологических процес-
сах термообработки (цементация, за-
калка,
нормализация, отпуск) приме-
няют камерные механизированные
универсальные агрегаты типа ТНЗМА,
СНЗМА
(см. рис. 2.8).
Объединяя детали в технологичес-
кие
группы с однотипной термической
обработкой, достигают полной загруз-
ки
печей и оборудования.
При
определении необходимого ко-
личества персонала, обслуживающего
камерные печи, составляют суммарные
графики
работы последних с указанием
времени загрузки, нахождения деталей
в
печи, выгрузки и
других
операций.
С
целью улучшения обслуживания
и
контроля за работой однотипное обо-
рудование (цементационные и отпуск-
ные
печи, травильные установки, дро-
беочистные агрегаты), используемое
для выполнения процессов, требующих
специальных условий (применение
контролируемых атмосфер, удаление
вредных паров, газов и пыли), в ряде
случаев размещают на отдельных
участках.
В поточных линиях и механизиро-
ванных термических печах управление
их механизмами автоматизируют с по-
мощью электрических или гидравли-
ческих (пневматических) приводов.
Схема управления в первом
случае
строится на связи конечных выключа-
телей, промежуточных реле и электро-
двигателей. Во втором
случае
дости-
гается взаимосвязь конечных выключа-
телей, промежуточных реле и электро-
магнитов, воздействующих на золотни-
ковые распределительные устройства,
от которых 'Приводятся в действие гид-
равлические (пневматические) цилинд-
ры механизмов. Первый импульс на
включение механизмов чаще всего да-
ется от реле времени.
В обслуживание печей и оборудова-
ния
входит
контроль за правильным
выполнением
технологического процес-
са, качеством выпускаемой продукции
и
состоянием оборудования.
При
обслуживании печей прежде
всего контролируется выполнение ре-
жима нагрева, т. е. требуемого распре-
деления температуры по печи, которое
в
подавляющем большинстве случаев
регулируется автоматически по тепло-
вым зонам (см. подразд. 1.5), для че-
го устанавливают соответствующие
щиты управления. В камерных печах
иногда применяется программное ре-
гулирование с заданным распределе-
нием
температуры во времени. При вы-
ходе
из строя автоматики печи вре-
менно
переводят на ручное управление.
Показания
тепловых приборов
проверяют, замеряя температуру с по-
мощью контрольных термопар и при-
боров. Требуемого режима нагрева не-
обходимо добиваться,
расходуя
мини-
мальное количество топлива.
В пламенных печах дополнительно
следят за правильным протеканием
процессов горения топлива, контроли-
руя работу горелок или форсунок;
давление газа и
воздуха;
соотношение
газа (или мазута) и
воздуха;
поддер-
жание на поду печи постоянного поло-
жительного давления; температуру по-
догрева
воздуха
и работу рекуперато-
ров.
В печах с контролируемыми атмо-
сферами
следят по приборам за соста-
вом газов, а в вакуумных печах — за
322