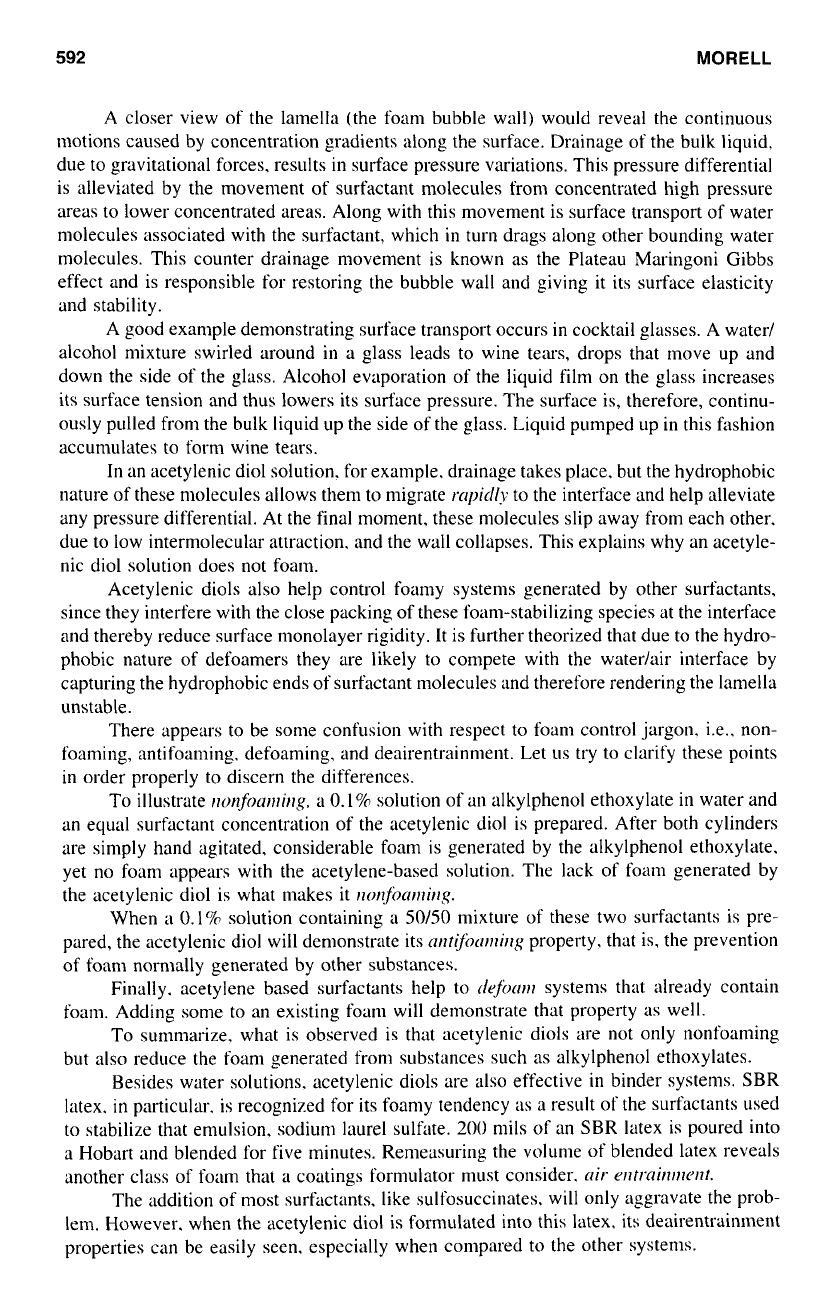
592
MORELL
A closer view of the lamella (the foam bubble wall) would reveal the continuous
motions caused by concentration gradients along the surface. Drainage of the bulk liquid,
due to gravitational forces. results
in
surface pressure variations. This pressure differential
is alleviated by the movement
of
surfactant molecules from concentrated high pressure
areas
to
lower concentrated areas. Along with this movement is surface transport of water
molecules associated with the surfactant, which in turn drags along other bounding water
molecules. This counter drainage movement is known as the Plateau Maringoni Gibbs
effect and is responsible for restoring the bubble wall and giving it its surface elasticity
and stability.
A good example demonstrating surface transport occurs
in
cocktail glasses. A water/
alcohol mixture swirled around
in
a glass leads to wine term, drops that move up and
down the side of the glass. Alcohol evaporation
of
the liquid film
on
the glass increases
its surface tension and thus lowers its surface pressure. The surface is, therefore, continu-
ously pulled from the bulk liquid up the side of the glass. Liquid pumped up
in
this fashion
accumulates to form wine tears.
In an acetylenic diol solution. for example, drainage takes place. but the hydrophobic
nature of these molecules allows them to migrate
mpiclly
to
the interface and help alleviate
any pressure differential. At the final moment, these molecules slip away from each other.
due to low intermolecular attraction. and the wall collapses. This explains why an acetyle-
nic diol solution does not foam.
Acetylenic diols also help control foamy systems generated by other surfactants,
since they interfere with the close packing of these foam-stabilizing species at the interface
and thereby reduce surface monolayer rigidity.
It
is further theorized that due to the hydro-
phobic nature of defoamers they are likely to compete with the watedair interface by
capturing the hydrophobic ends
of
surfactant molecules and therefore rendering the lamella
unstable.
There appears to be some confusion with respect
to
foam control jargon. i.e.. non-
foaming, antifoaming. defoaming, and deairentrainment. Let us try to clarify these points
in order properly
to
discern the differences.
To illustrate
rlonfoarving,
a
0.1%
solution of an alkylphenol ethoxylate in water and
an equal surfactant concentration of the acetylenic diol is prepared. After both cylinders
are simply hand agitated. considerable foam
is
generated by the alkylphenol ethoxylate.
yet no foam appears with the acetylene-based solution. The lack of foam generated by
the acetylenic diol is what makes it
norzjomnir1g.
When
a
0.1%
solution containing
a
50/50
mixture of these two surfactants is pre-
pared, the acetylenic diol will demonstrate its
ar~r$wrnir~g
property. that is, the prevention
of foam normally generated by other substances.
Finally. acetylene based surfactants help to
defimr?
systems that already contain
foam. Adding some
to
an existing foam will demonstrate that property as well.
To summarize. what is observed is that acetylenic diols are not only nonfoaming
but also reduce the foam generated from substances such as alkylphenol ethoxylates.
Besides water solutions, acetylenic diols are
also
effective in binder systems. SBR
latex.
in
particular. is recognized for its foamy tendency
as
a result of the surfactants used
to
stabilize that emulsion, sodium laurel sulfate.
200
mils
of
an
SBR
latex is poured into
a Hobart and blended for five minutes. Remeasuring the volume
of
blended latex reveals
another class
of
foam that a coatings formulator must consider.
crir
er1frai17r??m.
The addition of most surfactants. like sulfosuccinates. will only aggravate the prob-
lem. However. when the acetylenic diol is formulated into this latex. its deairentrainnlent
properties can be easily seen. especially when compared
to
the other systems.