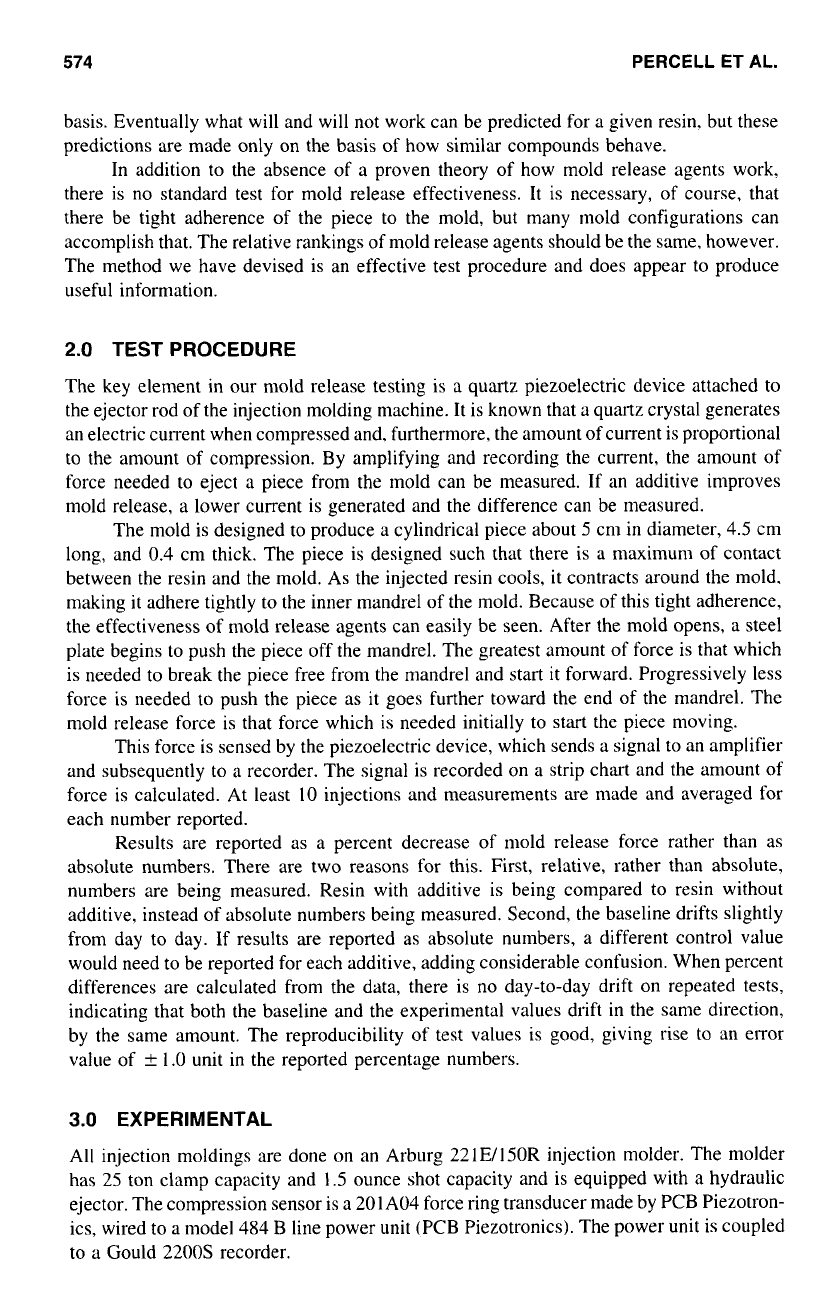
574
PERCELL
ET
AL.
basis. Eventually what will and will not work can be predicted for a given resin. but these
predictions are made only on the basis of how similar compounds behave.
In addition to the absence of a proven theory of how mold release agents work.
there is no standard test for mold release effectiveness. It is necessary,
of
course, that
there be tight adherence
of
the piece
to
the mold, but many mold configurations can
accomplish that. The relative rankings of mold release agents should be the same, however.
The method we have devised is an effective test procedure and does appear to produce
useful information.
2.0
TEST PROCEDURE
The key element in our mold release testing is
a
quartz piezoelectric device attached
to
the ejector rod of the injection molding machine. It is known that
a
quartz crystal generates
an electric cument when compressed and. furthermore, the amount of current is proportional
to the amount of compression. By amplifying and recording the current, the amount of
force needed to eject
a
piece from the mold can be measured. If an additive improves
mold release,
a
lower current is generated and the difference can be measured.
The mold is designed to produce a cylindrical piece about
5
cm in diameter,
4.5
cm
long, and
0.4
cm thick. The piece is designed such that there is a maximum
of
contact
between the resin and the mold. As the injected resin cools,
it
contracts around the mold.
making
it
adhere tightly
to
the inner mandrel
of
the mold. Because of this tight adherence,
the effectiveness of mold release agents can easily be seen. After the mold opens, a steel
plate begins to push the piece off the mandrel. The greatest amount
of
force is that which
is needed to break the piece free from the mandrel and start
it
forward. Progressively less
force is needed to push the piece
as
it goes further toward the end of the mandrel. The
mold release force is that force which is needed initially to start the piece moving.
This force is sensed by the piezoelectric device, which sends
a
signal to an amplifier
and subsequently
to
a
recorder. The signal is recorded on a strip chart and the amount
of
force is calculated. At least
10
injections and measurements are made and averaged for
each number reported.
Results are reported as a percent decrease
of
mold release force rather than
as
absolute numbers. There are two reasons for this. First, relative, rather than absolute,
numbers are being measured. Resin with additive is being compared
to
resin without
additive, instead of absolute numbers being measured. Second, the baseline drifts slightly
from day to day. If results are reported as absolute numbers, a different control value
would need to be reported for each additive, adding considerable confusion. When percent
differences are calculated from the data, there is
no
day-to-day drift on repeated tests,
indicating that both the baseline and the experimental values drift in the same direction,
by the same amount. The reproducibility of test values is good, giving rise
to
an error
value of
t
1.0
unit in the reported percentage numbers.
3.0
EXPERIMENTAL
All injection moldings are done on an Arburg 221E/150R injection molder. The molder
has
25
ton clamp capacity and
1.5
ounce shot capacity and is equipped with a hydraulic
ejector. The compression sensor is a 201A04 force ring transducer made by PCB Piezotron-
ics, wired
to
a model
484
B line power unit (PCB Piezotronics). The power unit is coupled
to a Gould
2200s
recorder.