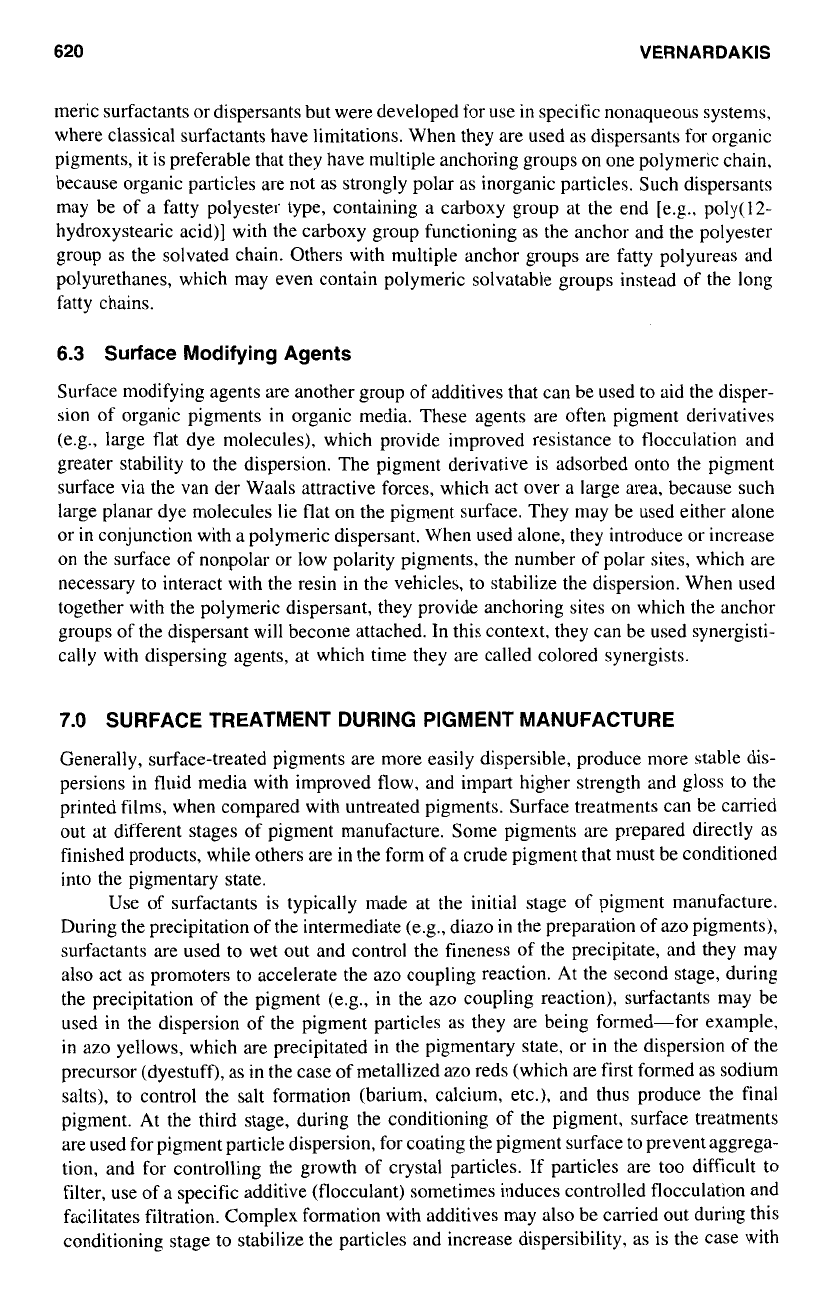
620
VERNARDAKIS
meric surfactants or dispersants but were developed for use
in
specific nonaqueous systems,
where classical surfactants have limitations. When they are used as dispersants for organic
pigments, it is preferable that they have multiple anchoring groups on one polymeric chain,
because organic particles are not
as
strongly polar
as
inorganic particles. Such dispersants
may be of
a
fatty polyester type, containing
a
carboxy group at the end [e.g.. poly(l2-
hydroxystearic acid)] with the carboxy group functioning as the anchor and the polyester
group as the solvated chain. Others with multiple anchor groups are fatty polyureas and
polyurethanes, which may even contain polymeric solvatable groups instead of the long
fatty chains.
6.3
Surface Modifying Agents
Surface modifying agents are another group of additives that can be used to aid the disper-
sion of organic pigments in organic media. These agents are often pigment derivatives
(e.g., large flat dye molecules), which provide improved resistance to flocculation and
greater stability to the dispersion. The pigment derivative is adsorbed onto the pigment
surface via the van der Waals attractive forces, which act over
a
large area, because such
large planar dye molecules lie flat on the pigment surface. They may be used either alone
or
in
conjunction with a polymeric dispersant. When used alone, they introduce or increase
on
the surface
of
nonpolar or low polarity pigments, the number of polar sites, which are
necessary to interact with the resin in the vehicles, to stabilize the dispersion. When used
together with the polymeric dispersant, they provide anchoring sites
on
which the anchor
groups of the dispersant will become attached. In this context. they can be used synergisti-
cally with dispersing agents, at which time they are called colored synergists.
7.0
SURFACE TREATMENT DURING PIGMENT MANUFACTURE
Generally, surface-treated pigments are more easily dispersible, produce more stable dis-
persions in fluid media with improved flow, and impart higher strength and gloss to the
printed films, when compared with untreated pigments. Surface treatments can be carried
out at different stages of pigment manufacture. Some pigments are prepared directly
as
finished products, while others are in the form
of
a
crude pigment that must be conditioned
into the pigmentary state.
Use of surfactants is typically made at the initial stage of pigment manufacture.
During the precipitation of the intermediate (e.g., diazo in the preparation of azo pigments),
surfactants are used to wet out and control the fineness of the precipitate, and they may
also
act
as
promoters to accelerate the
azo
coupling reaction. At the second stage, during
the precipitation of the pigment (e.g., in the azo coupling reaction), surfactants may be
used in the dispersion of the pigment particles
as
they are being formed-for example,
in
azo
yellows, which are precipitated in the pigmentary state, or
in
the dispersion of the
precursor (dyestuff),
as
in the case of metallized azo reds (which are first formed
as
sodium
salts), to control the salt formation (barium, calcium, etc.), and thus produce the final
pigment. At the third stage, during the conditioning of the pigment, surface treatments
are used for pigment particle dispersion, for coating the pigment surface to prevent aggrega-
tion, and for controlling the growth
of
crystal particles. If particles are too difficult to
filter, use of
a
specific additive (flocculant) sometimes induces controlled flocculation and
facilitates filtration. Complex formation with additives may also be carried out during this
conditioning stage to stabilize the particles and increase dispersibility,
as
is the case with