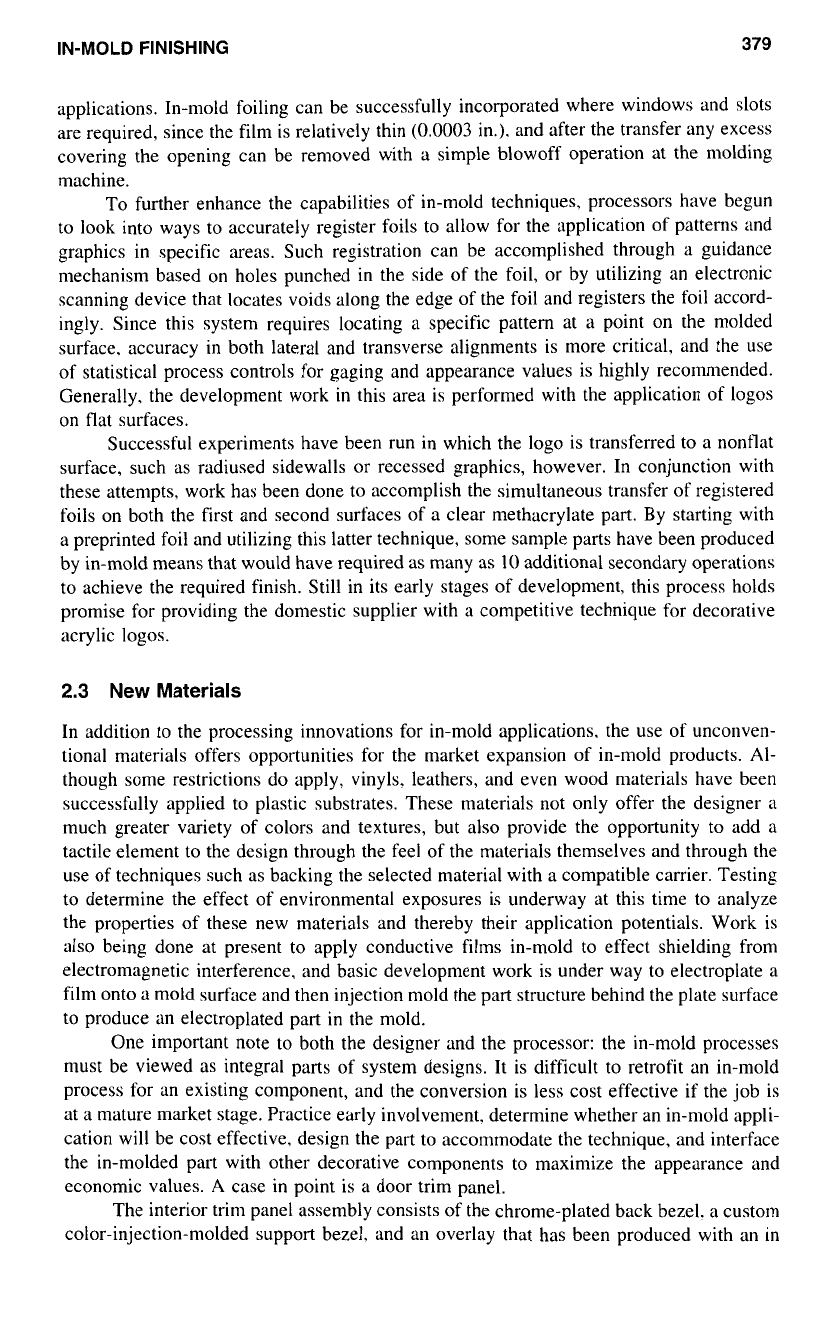
IN-MOLD
FINISHING
379
applications. In-mold foiling can be successfully incorporated where windows and slots
are required, since the film is relatively thin
(0.0003
in.). and after the transfer any excess
covering the opening can be removed with a simple blowoff operation at the molding
machine.
To further enhance the capabilities
of
in-mold techniques, processors have begun
to look
into
ways to accurately register foils to allow for the application of patterns and
graphics in specific areas. Such registration can be accomplished through a guidance
mechanism based on holes punched in the side
of
the foil, or by utilizing an electronic
scanning device that locates voids along the edge
of
the foil and registers the foil accord-
ingly. Since this system requires locating
a
specific pattern at
a
point on the molded
surface, accuracy in both lateral and transverse alignments is more critical, and the use
of statistical process controls for gaging and appearance values is highly recommended.
Generally. the development work in this area is performed with the application of
logos
on flat surfaces.
Successful experiments have been run in which the logo is transferred
to
a nonflat
surface, such as radiused sidewalls or recessed graphics, however. In conjunction with
these attempts. work has been done to accomplish the simultaneous transfer of registered
foils on both the first and second surfaces of a clear methacrylate part. By starting with
a preprinted foil and utilizing this latter technique, some sample parts have been produced
by in-mold means that would have required as many as
10
additional secondary operations
to achieve the required finish. Still in its early stages of development, this process holds
promise for providing the domestic supplier with a competitive technique for decorative
acrylic
logos.
2.3 New Materials
In addition to the processing innovations for in-mold applications. the use of unconven-
tional materials offers opportunities for the market expansion of in-mold products. Al-
though some restrictions do apply, vinyls. leathers, and even wood materials have been
successfully applied to plastic substrates. These materials not only offer the designer
a
much greater variety of colors and textures, but also provide the opportunity to add a
tactile element to the design through the feel of the materials themselves and through the
use
of
techniques such as backing the selected material with a compatible carrier. Testing
to determine the effect of environmental exposures is underway at this time to analyze
the properties
of
these new materials and thereby their application potentials. Work is
also being done at present
to
apply conductive films in-mold
to
effect shielding from
electromagnetic interference, and basic development work is under way to electroplate a
film onto a mold surface and then injection mold the part structure behind the plate surface
to produce an electroplated part in the mold.
One important note to both the designer and the processor: the in-mold processes
must be viewed as integral parts of system designs. It is difficult to retrofit an in-mold
process for an existing component, and the conversion is less cost effective if the job is
at a mature market stage. Practice early involvement. determine whether an in-mold appli-
cation will be cost effective, design the part to accommodate the technique, and interface
the in-molded part with other decorative components
to
maximize the appearance and
economic values.
A
case in point is a door trim panel.
The interior trim panel assembly consists
of
the chrome-plated back bezel. a custom
color-injection-molded support bezel, and an overlay that has been produced with an
in