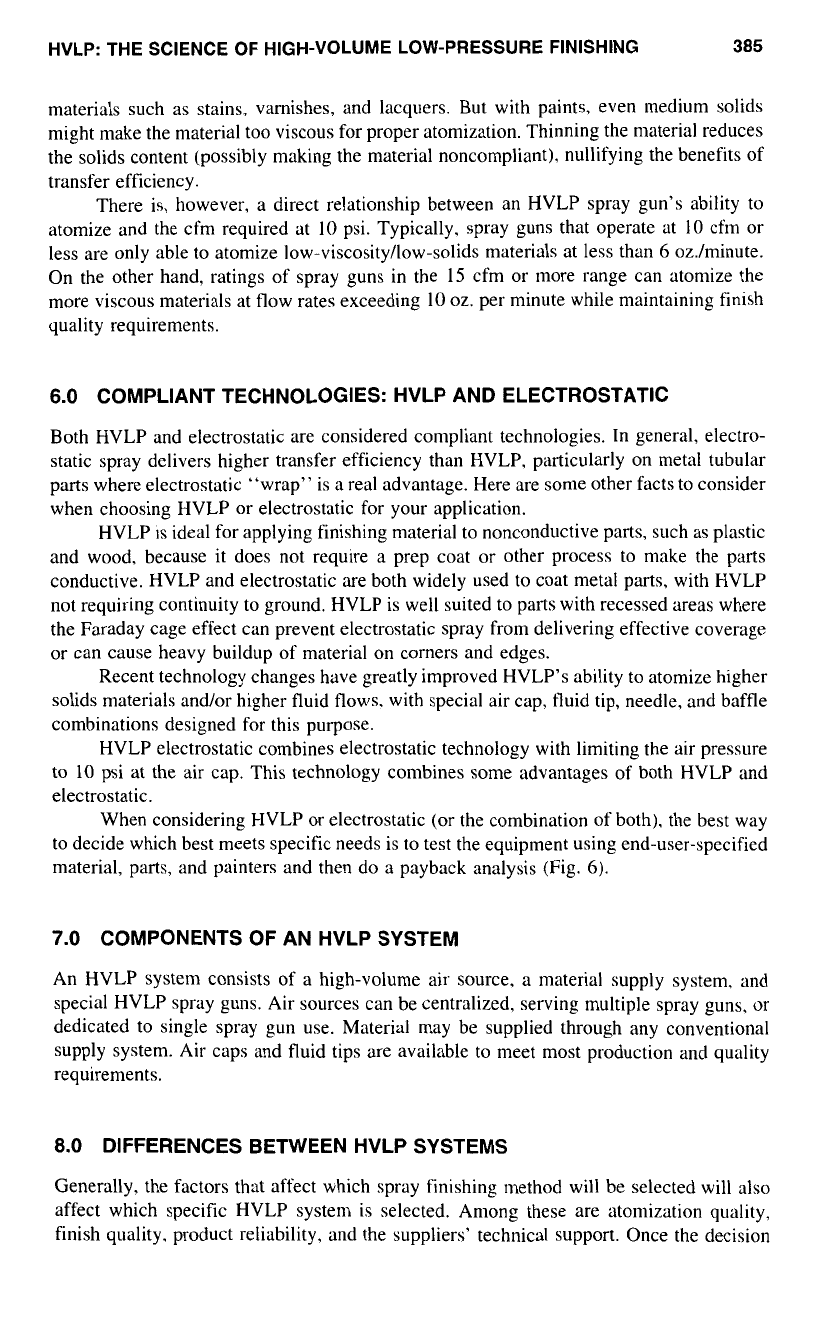
HVLP: THE SCIENCE
OF
HIGH-VOLUME LOW-PRESSURE FINISHING
385
materials such as stains, varnishes, and lacquers. But with paints, even medium solids
might make the material too viscous for proper atomization. Thinning the material reduces
the solids content (possibly making the material noncompliant), nullifying the benefits
of
transfer efficiency.
There is, however, a direct relationship between an HVLP spray gun’s ability to
atomize and the cfm required at
10
psi. Typically. spray guns that operate at
IO
cfm or
less are only able to atomize
low-viscosity/low-solids
materials at less than
6
oz./minute.
On the other hand, ratings of spray guns in the
15
cfm or more range can atomize the
more viscous materials at flow rates exceeding
IO
oz. per minute while maintaining finish
quality requirements.
6.0
COMPLIANT TECHNOLOGIES: HVLP AND ELECTROSTATIC
Both HVLP and electrostatic are considered compliant technologies. In general, electro-
static spray delivers higher transfer efficiency than HVLP. particularly on metal tubular
parts where electrostatic “wrap” is a real advantage. Here are some other facts to consider
when choosing HVLP or electrostatic for your application.
HVLP is ideal for applying finishing material to nonconductive parts, such as plastic
and wood, because it does not require a prep coat or other process to make the parts
conductive. HVLP and electrostatic are both widely used
to
coat metal parts, with HVLP
not requiring continuity to ground. HVLP is well suited to parts with recessed areas where
the Faraday cage effect can prevent electrostatic spray from delivering effective coverage
or can cause heavy buildup of material on corners and edges.
Recent technology changes have greatly improved HVLP’s ability to atomize higher
solids materials and/or higher fluid flows. with special air cap, tluid tip, needle, and baffle
combinations designed for this purpose.
HVLP electrostatic combines electrostatic technology with limiting the air pressure
to
10
psi at the air cap. This technology combines some advantages of both HVLP and
electrostatic.
When considering HVLP or electrostatic (or the combination of both). the best way
to decide which best meets specific needs is to test the equipment using end-user-specified
material, parts, and painters and then do a payback analysis (Fig.
6).
7.0
COMPONENTS OF AN HVLP SYSTEM
An HVLP system consists of a high-volume air source, a material supply system. and
special HVLP spray guns. Air sources can be centralized, serving multiple spray guns, or
dedicated to single spray gun use. Material may be supplied through any conventional
supply system. Air caps and fluid tips are available to meet most production and quality
requirements.
8.0
DIFFERENCES BETWEEN HVLP SYSTEMS
Generally, the factors that affect which spray finishing method will be selected will also
affect which specific HVLP system is selected. Among these are atomization quality,
finish quality. product reliability, and the suppliers’ technical support. Once the decision