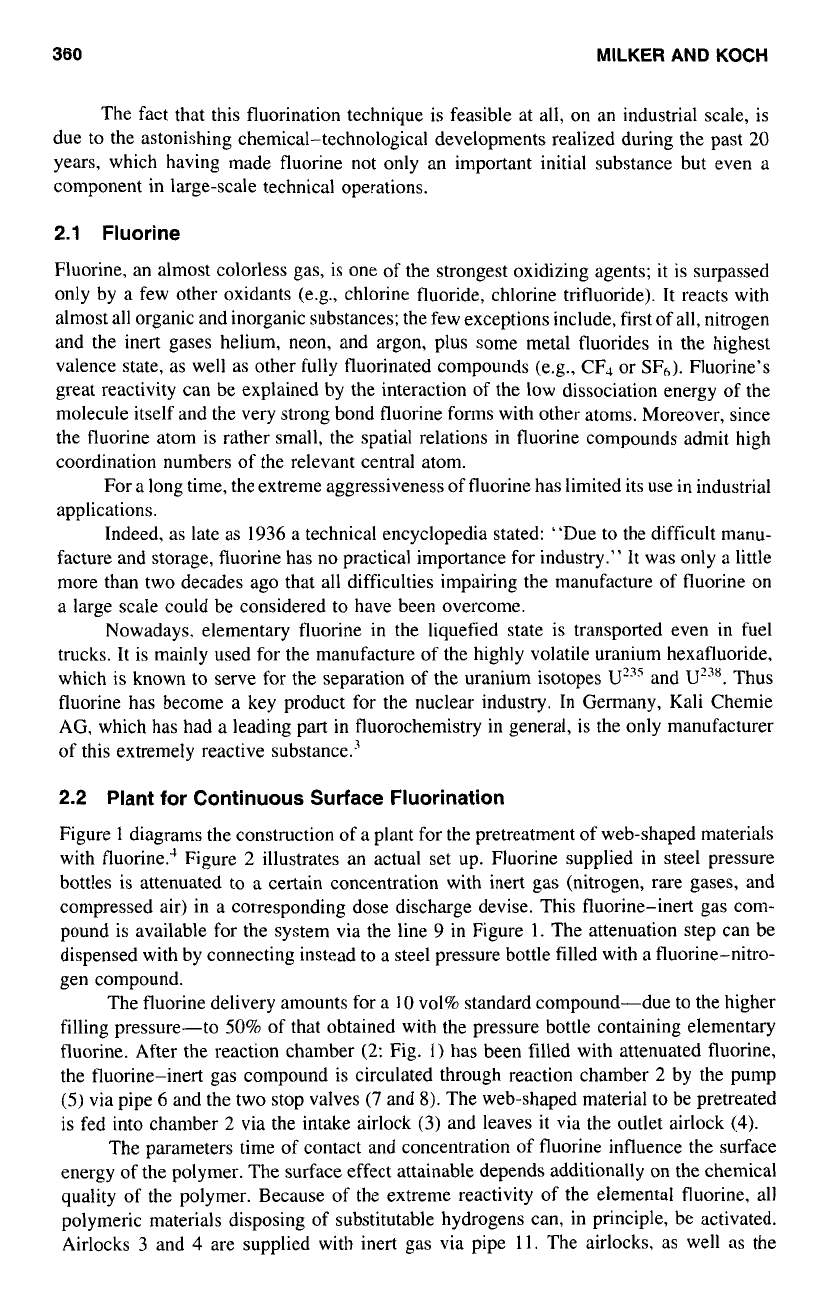
360
MILKER
AND
KOCH
The fact that this fluorination technique is feasible at all,
on
an industrial scale, is
due to the astonishing chemical-technological developments realized during the past
20
years, which having made fluorine not only an important initial substance but even a
component in large-scale technical operations.
2.1
Fluorine
Fluorine, an almost colorless gas, is one
of
the strongest oxidizing agents; it is surpassed
only by a few other oxidants (e.g., chlorine fluoride, chlorine trifluoride). It reacts with
almost all organic and inorganic substances; the few exceptions include, first of all, nitrogen
and the inert gases helium, neon, and argon, plus some metal fluorides in the highest
valence state, as well as other fully fluorinated compounds (e.g., CF‘ or SF6). Fluorine’s
great reactivity can be explained by the interaction
of
the low dissociation energy
of
the
molecule itself and the very strong bond fluorine forms with other atoms. Moreover, since
the fluorine atom is rather small, the spatial relations in fluorine compounds admit high
coordination numbers of the relevant central atom.
For a long time, the extreme aggressiveness of fluorine has limited its use in industrial
applications.
Indeed, as late as 1936 a technical encyclopedia stated: “Due
to
the difficult manu-
facture and storage, fluorine has no practical importance for industry.” It was only a little
more than two decades ago that all difficulties impairing the manufacture of fluorine
on
a large scale could be considered to have been overcome.
Nowadays, elementary fluorine in the liquefied state is transported even in fuel
trucks. It is mainly used for the manufacture of the highly volatile uranium hexafluoride,
which is known to serve for the separation of the uranium isotopes and
U’”.
Thus
fluorine has become a key product for the nuclear industry.
In
Germany, Kali Chemie
AG, which has had a leading part in fluorochemistry in general, is the only manufacturer
of
this extremely reactive substance.3
2.2 Plant for Continuous Surface Fluorination
Figure
1
diagrams the construction
of
a plant for the pretreatment of web-shaped materials
with fluorine.‘ Figure
2
illustrates an actual set up. Fluorine supplied in steel pressure
bottles is attenuated to a certain concentration with inert gas (nitrogen, rare gases, and
compressed air) in a corresponding dose discharge devise. This fluorine-inert gas com-
pound is available
for
the system via the line 9
in
Figure
1.
The attenuation step can be
dispensed with by connecting instead
to
a steel pressure bottle filled with a fluorine-nitro-
gen compound.
The fluorine delivery amounts for a
10
vol% standard compound-due to the higher
filling pressure-to
50%
of
that obtained with the pressure bottle containing elementary
fluorine. After the reaction chamber
(2:
Fig.
1)
has been filled with attenuated fluorine,
the fluorine-inert gas compound is circulated through reaction chamber
2
by the pump
(5)
via pipe 6 and the two stop valves
(7
and
8).
The web-shaped material to be pretreated
is fed into chamber
2
via the intake airlock (3) and leaves it via the outlet airlock
(4).
The parameters time
of
contact and concentration of fluorine influence the surface
energy of the polymer. The surface effect attainable depends additionally on the chemical
quality of the polymer. Because
of
the extreme reactivity of the elemental fluorine, all
polymeric materials disposing of substitutable hydrogens can, in principle, be activated.
Airlocks 3 and
4
are supplied with inert gas via pipe
11.
The airlocks, as well as the