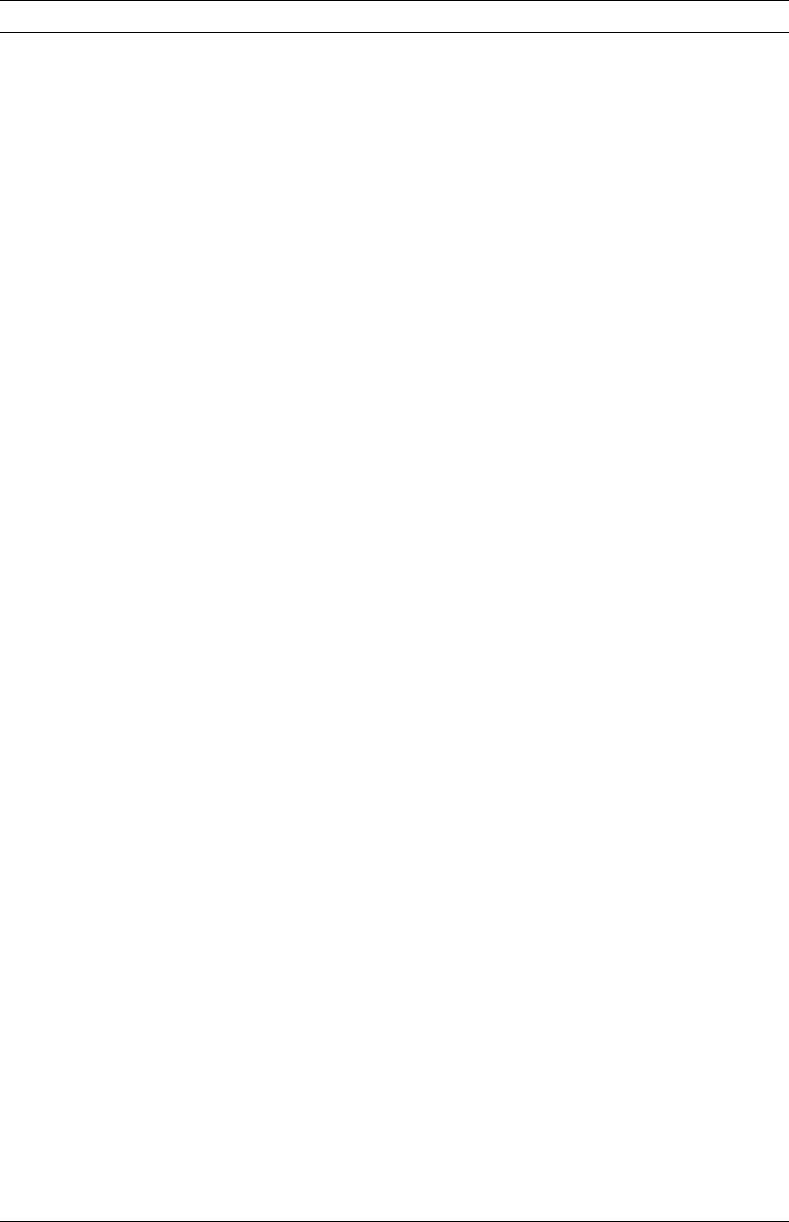
TABLE 10.5 (Continued)
Problem Possible Causes Check/Eliminate/Prevent
Peeled, scraped off
coating, and fines
Toonarrow entryguide or trapping on the rolls can “shave
off” coating or precut material
(continued) Check strip width. It must not be wider than the specified
maximum
Slitting Bad slitting frequently leaves metal fines or fine, cracked,
pulverized material at the slit edges which will be
deposited on the mill. After cleaning the mill bed and
tooling, clean the edges of the strip beforeitenters the
mill with a“rag.”Contact the slitter if the rag picks up
undesirablefibers or fines
Lubrication Check the lubricant used in forming
Check the tank and the filter in the recirculating system
In critical cases, install open cell foam blocks, pushed
against the top and bottom rolls to removefines
Surface scratch marks
(straight) [Figure
10.38(r)]
Entryguide, side-roll stand,
straightener,cutoffdie
Long straig ht scratch mark on the finished product. It is
relatively easy to trace it back to asharp edge or corner
causing this defect
Surface scratch marks
(arc) [Figure 10.38(s)]
Pick-up on roll, chipped roll,
crackedroll
Arc(circular) types of scratch marks on products on the
nonhorizontal legs or webs are most frequently caused
by “pick-ups”onthe rolls. The pick-up is usually zinc or
other metallic material transferred and fused to the roll
by combination of pressure and friction
clean the rolls
prevent pick-up by applying properlubricant and assure
proper gap between rolls
Polished rolls have lesser tendency to “pick-up”foreign
material than rolls with rough surface
Chrome plating of the rolls are most often unnecessarily
recommended. In some cases, it helps to eliminate or
minimize pick-up,but in most cases, the polished,
smooth surfaceofthe plated rolls is moreimportant
than the chromeonthe surface
If the marks are caused by chipped (or cracked) rolls, then
agood solution is to replacethe chipped (or cracked)
rolls. Aquick, short-term solution is to grind offthe
sharp edges around the chipped roll edge
Surface scratch or mark
(repeated) [Figure
10.38(t)]
Same as listed under “Arc”
type scratch marks
It appears at intervals of approximately threetimes the
roll diameter
Bent shaft It is usually easy to traceback to the roll or to other
rotating componentOther rotating tools, side or
straightener roll, secondary
operation rolls, and so on
Shinymarks
[Figure10.38(q)]
Material Some material, such as Galvalum-coated steel, dull
stainless steel or some dull painted surfaces willshow
shinypressure marks along the bend lines, even when
minimum roll pressure is applied. These marks are due
to the surfacecharacteristicsofthe strip (metal or
coating) and usually cannot be eliminated
Roll setup To omuch roll pressure (or insufficient roll gap) will create
shinymarks in anarrow strip in the full length of the
product. This is the most frequent cause of shinymarks.
The location of large pressure can be easily traced
back to the pass causing it while the productisstill in
the mill
( Continued)
Equipment Installation, Roll Setup, Maintenance, and Troubleshooting 10-47