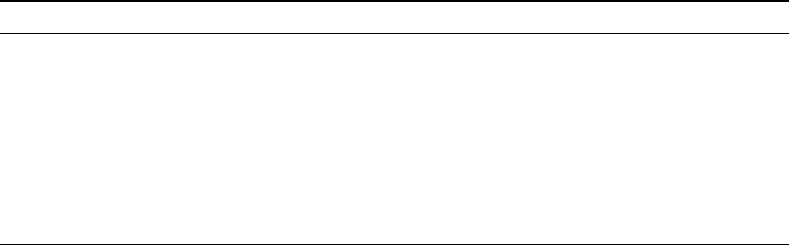
10.3.5.2 Gears
Gear failure, caused by wear and pitting,isaccelerated by overload, dirt, and grit and the lack of or
insufficiently maintained lubrication. Dirtand grit gets into the gear because of damaged or nonexisting
seals. Gear cracking and breakingoff teeth is usually caused by regular overload or sudden, very high
loads. The teeth of heavily worn gears can also break offatnormal load.
If rolls havebeen recut, then the operator must lower the top shaft to maintain the proper roll gap.If
the roll has been recut too much (the diameter becomestoo small), it is possible that the shaft distance
will be less than the recommended minimum, based on the pitch diameter.Inthis case, spur gears can
“bite”into each other.Operating the gears at apitch distanceless than the minimum will generate noise
and vibration, which creates clearly visible “chatter” marks on the surfaceofthe product (Figure10.23).
If gears are running in an oil bath, then the oil level should be checked frequently,right after the mill
stops. Oil leaks should be repaired not only to avoid oil loss from the gearboxes, but also to eliminate
contamination of the lubricants used for forming the section.
Improper gear alignment, sometimes caused by bearing failure, can also contribute to gear failure.
All gearboxesshould be opened at least once ever y3months for avisual check. If the temperature of
the stand or the gear reducer rises, vibrates, or runs noisily,then it should be checked as soon as possible.
10.3.5.3 Bearings
Rollforming mills contain manybearings. The life of the bearings is designed for acertain number of
hours at agiven load. As abearing wears, the surface of the inner and outer rings and the rolling elements
changes. This change creates vibration and sound. Most bearings in the roll forming line havealong life.
They are infrequently inspected unless vibration, noise or undue heat is generated.
The bearings carrying the shafts in the stands are critical and should be frequently checked. The
operator side of the shafts usually runs in needle bearings. Wear on the usually overdesigned needle
bearings is minimal. If these needle bearings are damaged, then the problem is usually caused by lack of
lubrication, sudden overload (double- or triple-thickness material passing throughthe rolls), or by avery
highbending moment created by the operator when lifting one end of the shaft too much (Figure 10.24).
Crackedorbroken bearing components frequently generate vibration or a“clicking” noise. These low-
cost bearings can be replaced quickly and easily.
The drive-side end of the shaft is held by cone bearings. Asmall wear on the bearings will makethe
shaft loose. When the outboard stand and the rolls are removedand the free end of the shaft can be
moved up or down easily,itistime to tighten the bearings. After afew adjustments, it cannot be
tightened anymoreand the bearing has to be replaced.
Rollforming mill bearings occasionally fail because an incorrectly selected forming lubricant has
leaked into the bearing houses and dissolved the bearing lubricant. Abrasive particles, such as scale from
hot-rolled steel, can drastically reduce bearing life. Maintaining good seals on the bearings is critical.
TABLE 10.3 Typical Lubrication Instruction for the Roll Forming Line Shown on Figure 10.9
Interval Lubrication
Every40running hours Cycle through entire speed range
No lube
Every160 running hours Greasepoints “B”(2) places (sliding disk bearing surfaces)
2shots each: 1shot “high” end of cycle, 1shot “low”end of cycle
Every960 running hours Greasepoints “A”
#500 —(2) places/#6000
(4) places. (shaft end bearings or thrust bearings (3) shots each)
Every1500 running hours Greasepoints “C” (2) places
(Motor) to be servicedbymaintenancedepartment. These points
are omitted on units with sealed bearings
Company lube code:GreaseG-2, Do not over grease.
Roll Forming Handbook10-18