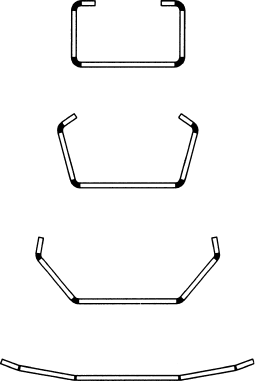
With theadvancement of computers, it
becomes easier to generate top view,side view,
or three-dimensional view of the flower (Figure
5.115). For an experienced roll designer,the
standard andoccasionally thesplitflower
diagrams are sufficient.
Theflower diagramisone of themost
important aspects of roll design. It reveals the
anticipated flowofthe material and the magni-
tude of the stresses generated by the forming
process. The designer tries to avoidlarge “jumps”
(markedas“b” in Figure 5.116a,b), resulting in
higher stresses at the edges or bend lines. The
moreeven the increments, the less chance there
is to run into problems. If necessary, additional
pass(es) can be added or some passes can be
eliminated. Shorter edge and bend line travel
distancewill generate less stress. The original
flower diagram (Figure 5.117a) maybemodified
to reach into thecorners wherever possible
(Figure5.117b).
To find the best, smooth, uniform flow,the rolldesigners usually modify their flower diagrams many
times beforethey are satisfied that undue stresses will not be created between anyofthe passes. Different
approaches to the flower design are described in Section 5.14.
Manually changing aflower diagram of asimple cross-section is easy.However,the morecomplex the
section is, the moretime consuming the change becomes. The roll designers are always under pressure
and frequently behind schedule. Therefore, often the last flower changes are not completed, only noted as
to what changes havetobemade during rolldesign.
One of the big advantages of the computer-aided roll design is the speed of changing the flower
diagrams. The rolldesigners can review manyalternatives in ashorttime and select the one which
appears to be the best under the given circumstances. Upon completion of the flower diagram, the roll
design can commencefrom pass to pass.
5.11.2 Forming in the First Pass Rolls
The first pass rolls havemultiple functions. They “pull” the leading edge of the strip into the mill and
complete the first forming. In some cases, they also guide the strip and can scorethe material for sharp
bending.
To pull the material into the mill is an important function. The maximum allowable forming angles at
all passes, including the first one, depend on the thickness, mechanical properties of the material, roll
diameter,length of the bent elements, lubrication, and the available top shaft drive. However,inthe first
pass, the maximum attainable angle often has to be reduced to suit the other functions, especially when
feeding the strip into the rolls. If the forming angle is too large, then the operator may havetocut tapers
on to twocorners of the leading edge of the coils. Considering the thousands of coils processed through
the mill, it is much less expensivetohavethe correct first pass rolls than have the mill standing idle while
the corners of the coil ends are cut.
Some products, such as widepanels formed in the first pass at the center are usually guided into
the mill by entryguides only.Ahead of the first pass of the center formed panel, a6-to12-in. (150- to
300-mm) long “hump”can be observedwhere the coil enters into the first pass center rolls. The length of
this free floating “hump”fluctuates during forming. This length change is frequently associated with
buckling in and out of the material which may show up as wavesinthe product. The forming can be
FIGURE 5.114 All bends formed at each pass (only 4of
the actual 12 passes are shown).
Roll Design 5 -75