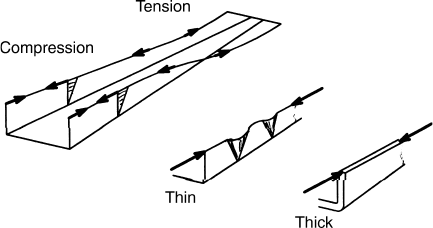
not strong enoughtoaccomplish the required forming at each pass. If the mill is strong enough,
which it should be in the majorities of cases, then the thicker the material, the less passes are
required. This effect can be explained by the fact that the thickness does not limit elongation
(strain), but thicker material will less likely be wavy when compressed in the longitudinal
direction (Figure5.106).
This effect is confirmed by manycases where narrow sections or wide panels can be
satisfactorily formed from different thickness of materials down to alimit. Material thinner than
this limit requires more passes for good forming,otherwise the product will be wavy or will have
other problems.
(b) Continuity of the Strip .Continuous forming provides asmoother flowofthe material from pass
to pass. The flowisdifferent when the partisprecut. The leading edge of the strip will slightly
spring back after leaving the forming pass, and will travelpractically in astraight line until the
front end hits the lead-in flange of the next pass of rolls. Abruptforming thereforetakesplace
on entrytothe next pass. The rest of the precut strip is formed as acontinuous section, but a
similar “jump”happens everytime when the front end of the strip contacts the next forming
pass. Similarly,there will be difference in the flowwhen the tail end of the strip exits from the
passes.
To minimize abrupt forming, precut strips are usually roll formed with two or three more
passes than the same section formed from acontinuous strip.The front and tail ends of precut
sections frequently havemoreflarethan the same section formed from continuous strip cut to
length after forming.
Applying astraightener or curving unit after forming precut strips is either not practical or
quite complicated.
(c) Holes and Notches.Notches at the edge of the strip haveasimilar effect on forming as precutting.
The deeper the notch, the more similar the effect is to precutting (Figure5.107 and Table 5.5).
Holes punched in the web havelittle influence on the number of passes. However,holes
punched in the elements which are under tension during forming can greatly influencethe
required number of passes. In extreme cases, products with large cutouts close to the elements
exposed to highest strain require30, 50, or 80% more passes to be formed than the same section
without holes. Insufficient number of passes will distortthe shape of the holes.
Very large cutouts, like complex miter prenotches will makeroll design moredifficult. At the
point of alarge cutout, the remaining strip is veryweak, but it should neither be permanently
stretched nor compressed during forming. This cross-sectional weakness will also create problems
when the strip passes through aloop after punching,when the material is forced through the
straightener,and when the finished product is handled after forming.
The number of passes is established to keep the stresses at the edges of the strip at around or just
abovethe yield point. When wire webs or sections slit to the edges (Figure5.108)are rollformed,
FIGURE 5.106 The buckling strength of thickerand higher strength material is higher;therefore, it is less likely to
buckle under compression than the thin or low strength material.
Roll Design 5 -65