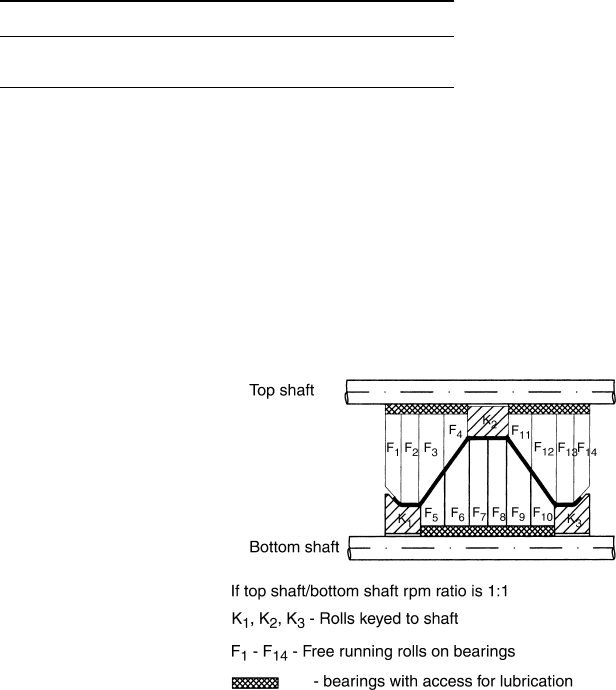
Nondriventop shafts are less expensive, but the mill maynot havesufficient friction to pull the material
when only the first few passes are engaged. Mills with bottom-driven-only last passes may not generate
sufficient “pull” (tension) to avoidbuckling between the passes and to push the material through the
straightener or curving unit and the cutoffdie.
Formills with partial spur-gear drives at selected locations, the roll designer must specify the passes
which requiretop shaft drive. Usually,atleast the first two and the last twopasses are driven. Depending
on the circumstances, additional passes could also havetop drives. If aspur-gear on the bottom roll
directly drives aspur-gear installed on the top roll(or vice versa), then the gear pitch diameters will also
determine the pitch diameters of the rolls. The roll pitch diameter must match the gear pitch diameter
with allowancetoadjust for material thickness
variation and limited recuts of the rolls.
Rollforming mills with the facilityfor quick
disconnection of the top rolldrive are the most
versatile for selecting the appropriate top shafts
to be driven.
In deep sections, the surface speed differential
between different parts of the rollsand the
material can be large. To minimize the friction,
not only the top shaft is nondriven, but indivi-
dual segments of therolls areoccasionally
allowedtorun freeonbearings installed on the
shafts (Figure5.61). The reduced friction will
reduce tool wear,horsepowerrequirement and
surface scratches. It is the tool designer’sfunction
to determine which rolls should be free-running.
The roll designer also has to cooperate with the
machine designer to ensurethat the bearings of
the free-running rollscan be properly lubricated.
5.5.9 Bottom Shaft Drive
It is accepted by the roll forming industrythat, as arule, all bottom shafts are driven. However,
occasionally not driving some bottom shafts has advantages.
Example
Abottom-drivenmill, with afew top-drivenpasses, forms abuilding panel withseven ribs (Figure5.62).
The forming startsbymaking the center ribs in five passes. Forming continues with the adjacent two ribs,
made in the next five passes, then the next tworibs in five passes, and, finally,the two outside ribs in six
passes. As the rib heights are gradually formed to full height, the diameter of the driven bottom rolls
increases. If the section depth is 1in. (25.4 mm), then the circumferenceofthe larger rolls is about 6in.
(152 mm) larger than the rolls that starttoform the ribs. Because the shafts are running at the same rpm,
the last few rollsforming each rib are “pulling” the material faster then the first tworolls. Actual
observation showed that passes 1and 2, 6and 7, 11 and 12, and 16 and 17 (circled in Figure5.62), which
starttoform the ribs, havenegativetorque, or in other words, are breaking,pulling back the formed
section. The first twopasses cannot be disconnected because they are required to pull the front end of
FIGURE 5.61 “Free-running”rolls reduce friction
between rolls and formed sections.
TABLE 5.2 Keyway Width in Rolls
KeyWidth b
3/16 to 1/2 in. (5 to 12.5 mm) 1/16 in. (1.5 mm)
Over 0.5 in. (12.5 mm) 1/8 (3 mm)
Roll Forming Handbook5 -38