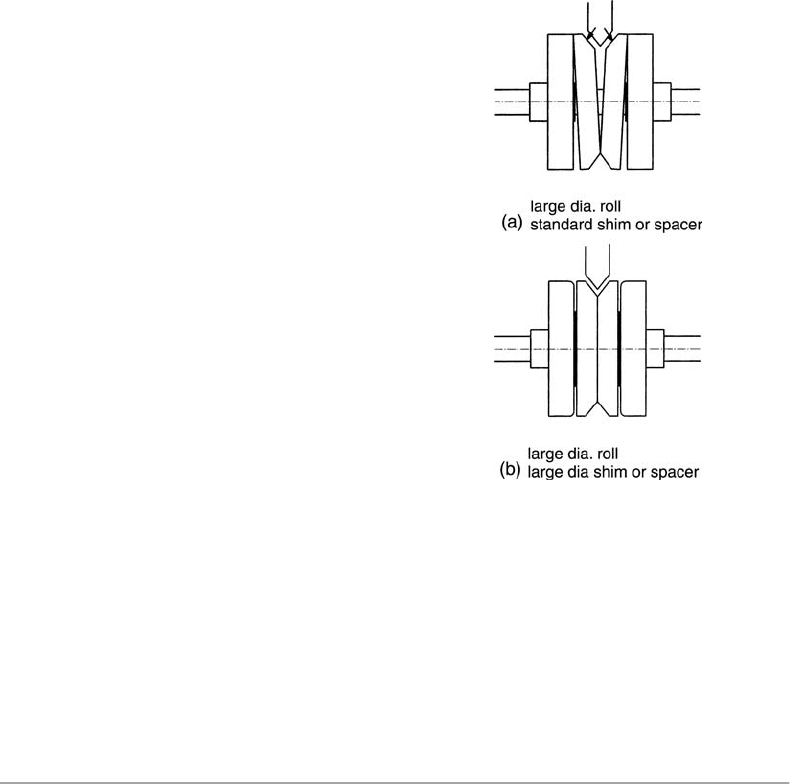
The removal and reinstallation of such a
split spacers may take less than 1min after
the operator-side stand is pulled out by a
shortdistance.
Split spacers are moreexpensivethan
one-piecespacers, but the extra cost can be
quickly recovered by reducing the non-
productive time.
5.7.5 Shims
(a) One-Piece Shims .Shims are made out of
hard“shim”stock. The bores can be about
0.005 to 0.060 in. (0.13 to 1.5 mm) larger
than the shaft diameters. Keyways should
be cut into the shims. The outside diameter
should be aminimum 1in. (25 mm) larger
than the bore. If the shims or spacers are
placed between largediameterrolls
(Figure 5.83), then their O.D. should be
considerably larger to avoid excessive tilt-
ing or bending of the rolls.
Shimsshouldbeavoided wherever
possible. Shimscannotbeproperly
marked, and they can be easily mixed up
and lost. The edges of the thin shims can
easily fold over,creating aspace of double
shim thickness between rolls.
(b) Split Shims.Quick-change shims can be easily made by splitting the shims at one side as shown in
Figure5.84a. The use of horseshoe shims (Figure 5.84b) is definitely not recommended for the
reasons explained in Section 5.7.4b.
5.8 Calculating Strip Width
5.8.1 Straight and Curved Elements
To calculate the blank size, or in other words, strip or coil width, the final cross-section is divided into
straight and curvedelements. Forblank size calculation purpose, it is assumed that the lengths of the
straight elements do not change during roll forming. Calculating the length of acurved element by using
the length of its center line (theoretical neutral axis) gives an incorrect, larger starting width than the
required width.
Foraccurate strip width calculation, it is assumed that the theoretical neutral axis of the bent element
moves from the half thickness location closer to the inside (Figure5.85a). The new location of the
“relocated” neutral axis is expressed by the bend allowance(“ k ”). Forexample, the “ k ”factor for alow
carbon, annealed steel having abend radius equal to the material thickness ð r : t ¼ 1 Þ is about 0.33. This
means that the new neutral axis, used to calculate the blank size, will be 0.33 times the metal thickness
distancefrom the inside surfaceofthe bent element instead of 0.5 times.
In reality,the material also gets thinner at the corners as shown in Figure 5.85b. The stresses created by
the bending are over the yield limit and they cannot change abruptly to zerostress at the end of the
curvedelement. The changeover is gradual, which means aslight thickness change in the straight element
too.However,the empirical “ k ”factor used for the curvedelement provides an accurate blank size (strip
width), with the assumption that the length and the thickness of the straight element are not changing.
FIGURE 5.83 Between large diameter rolls, large
diameter shims or spacers should be used to avoid tilting
of the rolls.
Roll Forming Handbook5 -52