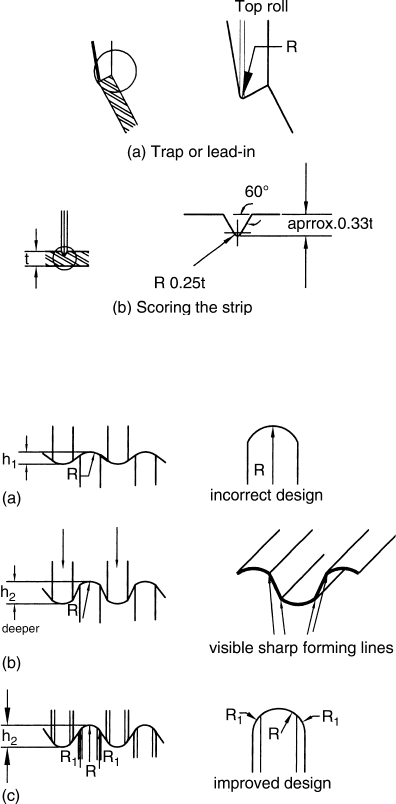
Designs incorporating traps can leave
verysharp roll edges. These edges can be
easily damaged. It is recommended to
either avoid them or add asmall radius
to them (Figure5.145a).
Asmall radius is recommended at the
peak of the scoring(grooving) rolls used
when the product must be formed with
sharp inside radius (Figure5.145b).
For rolls forming sine wave corruga-
tions,adifferent kind of radiusis
recommended. The sinusoidal shape is
usually “air bent”and the roll designer
specifies therequiredradiustobe
incorporated onto the outer edges of
the “donut” shaped rolls. This method
workscorrectlyinmostcases
(Figure5.146a). However, to reduce
springback the forming depth maybe
increased by lowering the top shafts. If
the rolls are pushed deeper in between
each other,the material is no longer
tangential to the rolls. This can create
unacceptable sharp forming lines adja-
cent to the radii in the panels (Figure
5.146b). To avoid the sharp lines, it is
recommended to placeadditional radii at
the edges of the rolls, tangential to both
the large forming surface and the flat
ends of the roll (Figure 5.146c).
(c) Bore Radii.Asharp edge in the boreof
therolls can damagethe shafts and
make installation difficult. Therefore, it
is recommended to specify asmall radius
at both ends of the bores. The radius can
be 0.030 to 0.060 in. (0.75 to 1.5 mm) in
rolls up to 10 in. (250 mm) in diameter.
Toolarge boreradius can create problems
because of the reduced contact area between the rolls and the spacers or shaft shoulders
(see Section 5.7.2).
5.12.6 Relief
The inevitable surface speed differential along the contour of each roll, caused by the different roll
diameters (Figure5.147), create manyproblems. Different diameter roll segments forming or just
contacting either side of the strip surfacewill create friction, maymark the surface of the product, wear
the rolls, make the productspeed unevenand increase the torque (horsepower) requirement for forming.
To minimize the friction, the rollsare often designed with a“relief.”The example shown on
Figure5.148 shows the top roll relieved by 2to38 .This change eliminates the friction between the top roll
and the product, and by driving the product at the peak of the section provides amorepositive and even
driveatthe pass line height.
FIGURE 5.145 To avoid “chipping” of roll edges,
applying asmall radius is suggested at the critical points.
FIGURE 5.146 Asingle radius at the working surface of
the donut-shape rolls (a) can mark product (b). Added
corner radii eliminate this problem (c).
Roll Design 5 -87