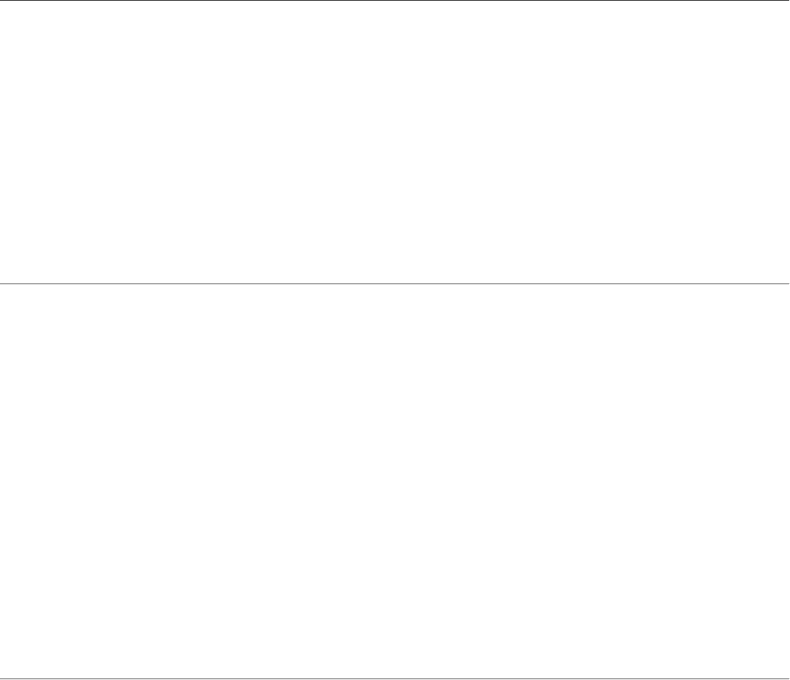
4.19 Painting
Alarge percentage of roll formed products are postpainted. In continuous operations, the products are
hung from the roll forming line run-out table directly onto the paint line. In less critical applications such
as structural building parts, often only aprime coat is applied without cleaning.However,inmost cases,
the metal has to be cleaned. In these cases, the products hooked onto aconveyor travelthrough a(usually)
three-stage washer before priming and finish coating. In some less critical operations, the priming is
omitted.
The means of hanging the product and draining the excess cleaning liquid or paint havetobe
considered in the design stage (e.g., punching holes in the roll forming line for this purpose only).
4.20 Foaming
Residential entrancedoors, garage doors, industrial/commercial building walls, and refrigeration
cabinets are frequently built from sandwich panels. The panels havelight gage metal skins on the outside
and foams in between. In addition to the less frequently used adhesive bonding of rigid foams
(Section 4.16), the foam can be applied either in abatch process or in acontinuous line.
In the batch process, the inside and outside skins are assembled together with separators. Several
products are placed in apress and foaming material is injected between the skins. During curing,the
foam exerts large pressurebut the retaining pressureofthe press prevents the bulging of the skins.
In continuous foaming process, one panel roll former is forming the inner and another rollisforming
the outer skins. One of the mills is about 6to12ft. (2 to 4m)above the other one. The two panels are
brought together in ashallowangle to the point wherethey start to travelparallel to each other.Foam is
sprayed where the two panels meet. During curing,the skins are held in position by strong caterpillar
type of retaining support, which moves with the panels. After curing,the finished product is usually cut
to length wi th aflying saw.
4.21 Packaging
With the exception of products which are assembled at the end of the line into alarger product
(e.g., welding adust ring into an automotive brake component), the products must be packaged and kept
together to facilitate moving into storage, transportation or retail sales.
Roofdecks are just strapped together;sidings are put into acrate. Nonnesting panels and “U” and “C”
channels are nested in pairs (everysecond one is flipped over). Studs are paired too; everyten studs (five
pairs) are strapped together into asmall bundle, and then from several of these ten-pack small bundles a
large bundle is formed and strapped to apallet ready for transportation.
Residential sidings, do-it-yourselfproducts, car trims for after market, and manyother products
are packed at the end of the line into decorative,printed cardboard or other packages.
Because of these packaging requirements, four to six people are often involved in packaging while one
is operating the line. Lately,automated packaging equipment enables running the line by one operator
only,and in some places, one operator runs twoormorerollforming lines, coupled with automated
packaging and package removal.
References
[232] Czerski, R., Howtomakeroll-formed welded products, MetalForming,September,38–44, 1996.
[233] Halmos, G., Curving and straightening of rollformed parts, Fabricator,March/April, 1989.
Roll Forming Handbook4 -62