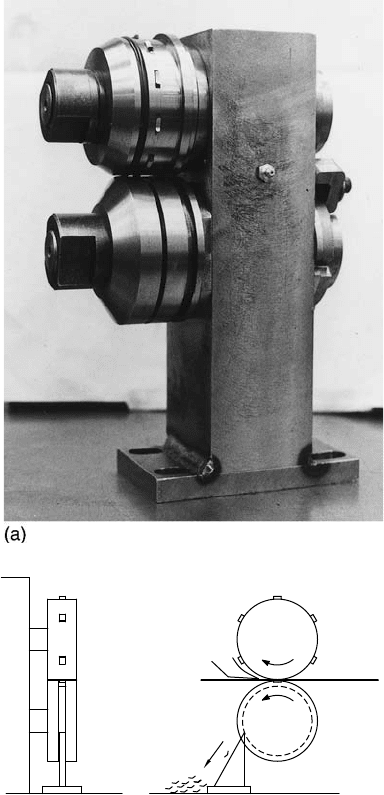
the slot. Close to the bottom, afinger reaches
into the slot, prying the slugs out from the slot
(Figure4.110b). This small, relatively low-cost
arrangement does not require backlash gearing
between the top and bottom rolls. The burr will be
larger after punching,but the rolls in the mill will
flatten the burr down.
Rotaryoperations are frequently similar to the
press operations. The forces generated by the
operations are larger then the ones required for
forming.Therefore, rotaryoperations usually
require larger shaft diameters, larger capacity
bearings, better top shaft adjustment, sturdier
stands, and very accurate shoulder alignment.
If the distanceofthe holes, notches, emboss-
ment, and louvers from the strip edge is critical,
then thestrip ca nbetrappedinthe rolls
(Figure4.111). In other cases, such as decorative
embossment, the rollsare wider than the strip and
the use of strip entryguides are usually sufficient.
During therotar yoperations,the tool is
engaged in the material. As aresult, thereisno
material slippage during engagement and no
compensation for strip speed differential between
therotar yand roll formingoperation.The
simplest solution to avoid problems is not to
drive the rotary tools.
The material must be engaged into several
passes to havesufficient friction to pull through
the rotary dies. It is feasible to open up the gap
between the rotary dies, engage the strip into the
mill and then close the gap again. This is atime-
consuming process and the lead end of each coil
would be wasted. Therefore, in the case of small
forces (thin material, single hole, or emboss-
ment), the operator side of one shaft can havea
square end to facilitate ahand crank (Figure
4.112). The strip is moved through and punched
(embossed) betweenthe rollsbyhanduntil
sufficient length is generated to be caught and
pulled by the forming rolls.
Manual threading is neither practical nor feasible when the torque requirement is too high(thick,
high-strength material, multiple operations at the same time, etc.). In these cases, amotorized, slow die
rotation is used with an overriding clutch. The strip passes through the rotary dies slowly,and once the
forming rolls grab it, probably at the third or fifth pass, it is pulled throughbythe mill at aspeed higher
than the speed of the rotary tool roll.Then, the overriding clutch lets the strip turn the rotary unit. An
alternative solution is to weld the coil ends together.
If the rotary operation was not considered at the time of designing the line, and the mill does not have
sufficient horsepowermotor to pull the material through the rotary dies, then aseparate rotary punch
drive mayberequired. Because it is very difficult to synchronize the speed of the mill and the rotary
operation, aloop with aloop control is recommended between the rotary unit and the mill.
FIGURE 4.110 Rotarypunching unit utilizing punches
in the upper roll and aslot in the bottom roll (a); slugs are
removed with afinger reaching into the slot (b).
Roll Forming Handbook4 -48