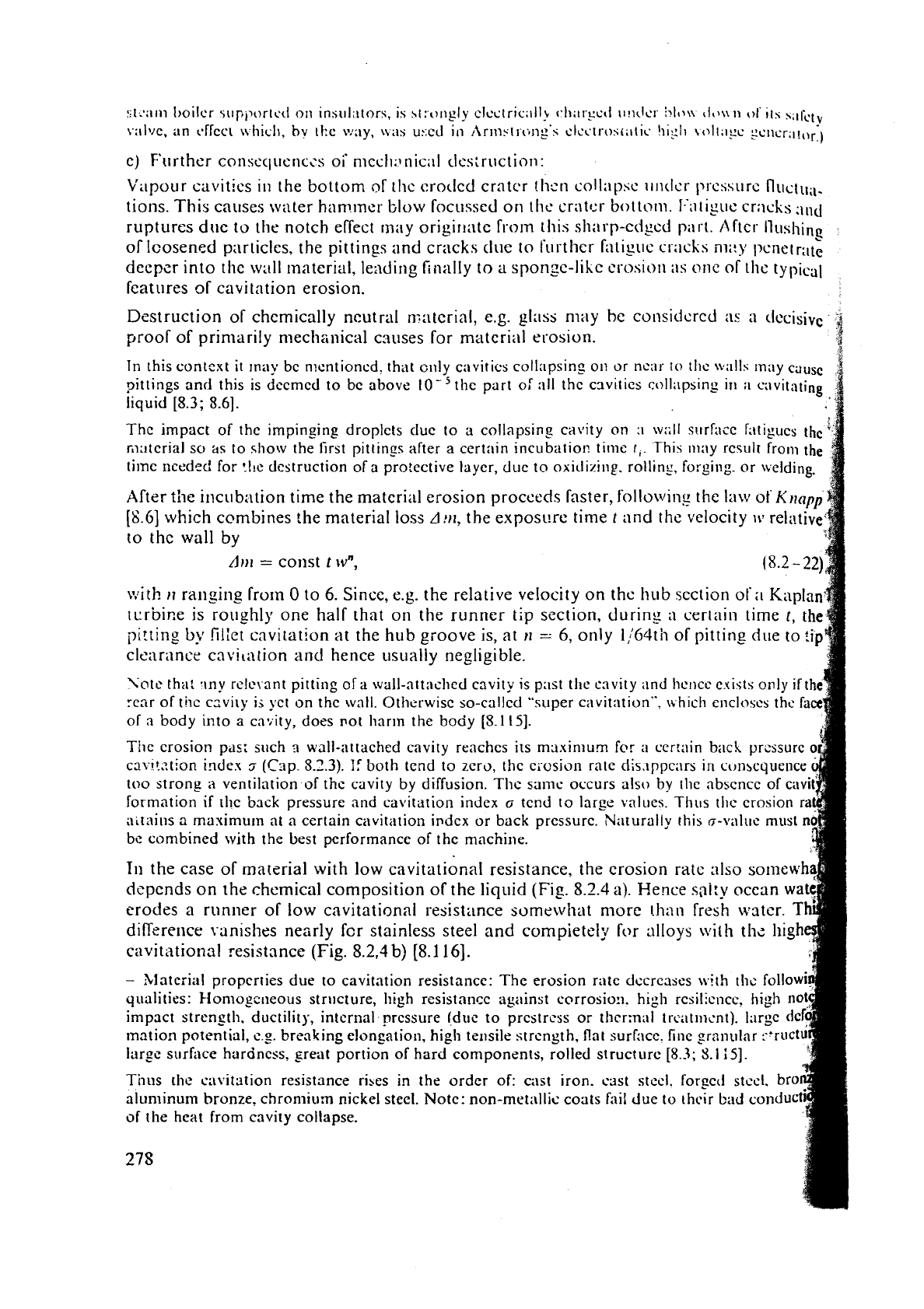
!;t:*:trn I)oilcr slipi>ort~tl or1 insirlators, is ht:.onfly clcctric:~llc c:li;~rccci \l!l{lcr
':lit$\\
ti,$\\
n
of
its
s;lfctY
v:~lvc. an 1.ffcct
\\:hicl~,
bv 11:c
\B!;~y,
was
u:;cd
in
11rrns11-(ing's clccrrosi~~lic~ !ii:!l~ \oll;ryc gcllcr;l!,,r,)
e) Further cotiseqilcnccs
oi'
n~ccli;~nic;il tlcs:ruction:
Vapour cavities
in
the bottom nf
thc
crotlcd cratcr
then
collnpsc 1111cIcr
IJI.C!+LI~~
tions.
This
causes water hammer blow focussed on the crntcr bottom. I-atigi~e cr;lcks :1nd
ruptures due to the notch effect tnay origitlatc from this sharp-cdgcd p;lrt. 11fter' IILIs~~~~~
L
of
lcosened particles. the pittings and cr:lcks clue to further frttigl~c cracks
miry
pcnetr;lte
deepzr into thc wall tnaterial, lending finally
to
a spongc-like c~-osiat~
iIS
one of Ihc
typical
features
of
cavitation erosion.
Destruction
of
chemically ncutral n:atcrial, e.g. glass nlay be considcrcd
a:
a
decisive
proof
of
primarily mechznical causes for material erosion.
a
1
%
In
this contcxt
it
rnay bc mcntioncd, that cnly c;lvitics collapsing on or ncar to tllc
\\;III\
may cause
pittings and this is dcemcd to be above
loe5
the part or
:ill
the cavities call,\psing in
;I
cavitating
liquid
18.3;
8.61.
Thc impact of the impinging droplets clue to a collapsing cavity
on
:I
w:;ll
sr~rf:lcc fi~tigucs
the"
filaterial so
as
to show the first pittings after
a
certain incubatio~? time
f,.
'This
may
rcsirlr fro111
the
tirnc needed for !l!c
destruction
of a protective layer, due to oxidizing. rolling, forging. or welding.
After the incubation time the material erosion proceeds faster, following the
law
ot
k'nnpp
[8.6]
which combines the material loss A,~I, the exposure time
t
and the velocity
\rl
relative
to
the wall by
AIII
=
co~lst
t
wn,
(8.2-22)
with
II
ranging from
0
to
6.
Since,
e.g.
the relative velocity on the hub section
ot'a
Knplan
1crbir.e
is
roughly one half that on the runner
tip
scction, durins
n
certain time
t,
the
pitting
by
fillet
cavitation at the hub groove is, at n
-
6,
only 1164th
of
pitting due
to
lip
cl~ilranct. cavitation and hence usually negligible.
Yotc that
my
rc!c\.ant pitting of
a
wall-nttr~ched cavity is ~~1st tlie cavity and hcncc c?tistso~ily
if
t
rcnr of thc czvi~y
is
yct on the wall. Otherwise so-called "super cavitation", which encloses the fa
of
s
body into
a
cavity, does vot harm the body [5.11
51.
Tile erosion pi~s: such
s
wall-attached cavity reaches its maximurn for
a
certain back prcssurc
cavi!ztion index
5
(C3p. 5.3.3).
If
both tend to zcro, thc erosion rate clls;~ppcnrs in
consequence
too
strong
a
ventilation of the cavity by diffusion. Thc samc occurs also by thc abscncc of
ca
formation if ille back pressure and cavitation index
G
tend to large values, Thus thc erosion
aitains
a
maximum at
n
certain cavitation index or back pressure. Naturally this 6-value must
n
bc
combined
with
the best performance of the machine.
111
the case
of
material with low cavitational resistance, the erosion rate also somewh
dcpends on
the
chemical composition
of
the liquid
(Fig.
8.2.4
a).
Hence
s;li:y
ocean
wat
erodes a runner
of
low cavitational resistance sumtt\\lhat more ~.hnn fresh water.
T
dikrence vanishes nearly fcr stainless steel and compietcly for alloys \vit!i thc high
cavitational resistance
(Fig.
8.2,3
b)
[8.116].
-
Material propcrries due to cavitation resistance: The erosion rate dccrcases with tlic follo
qualities: Hon~o~cueous structure,
high
resistance against corrosio:l. high rcsilicncc, high n
impact strength, ductility, internal
-
pressure fdue to prcstrcss or thermal
t
rcatnncnt). large
dc
mation potential, c.2. breaking elongation, high tr~~sile strcngth, flat surf:lcc, fine gr:,nular :+ruct
1ar_ge slirfilce hardness, great portion of hard components, rolled structure
[8.3;
5.1
i5].
Thus the cavitation resistance ribes
in
the order of: cast iron. cast stccl. forgcti stecl. bro
alunlirium bronze, chromium nickel steel. Notc: non-metallic coats fail due to thcir
bad
coliduc
of tlie heat from cavity collapse.
275