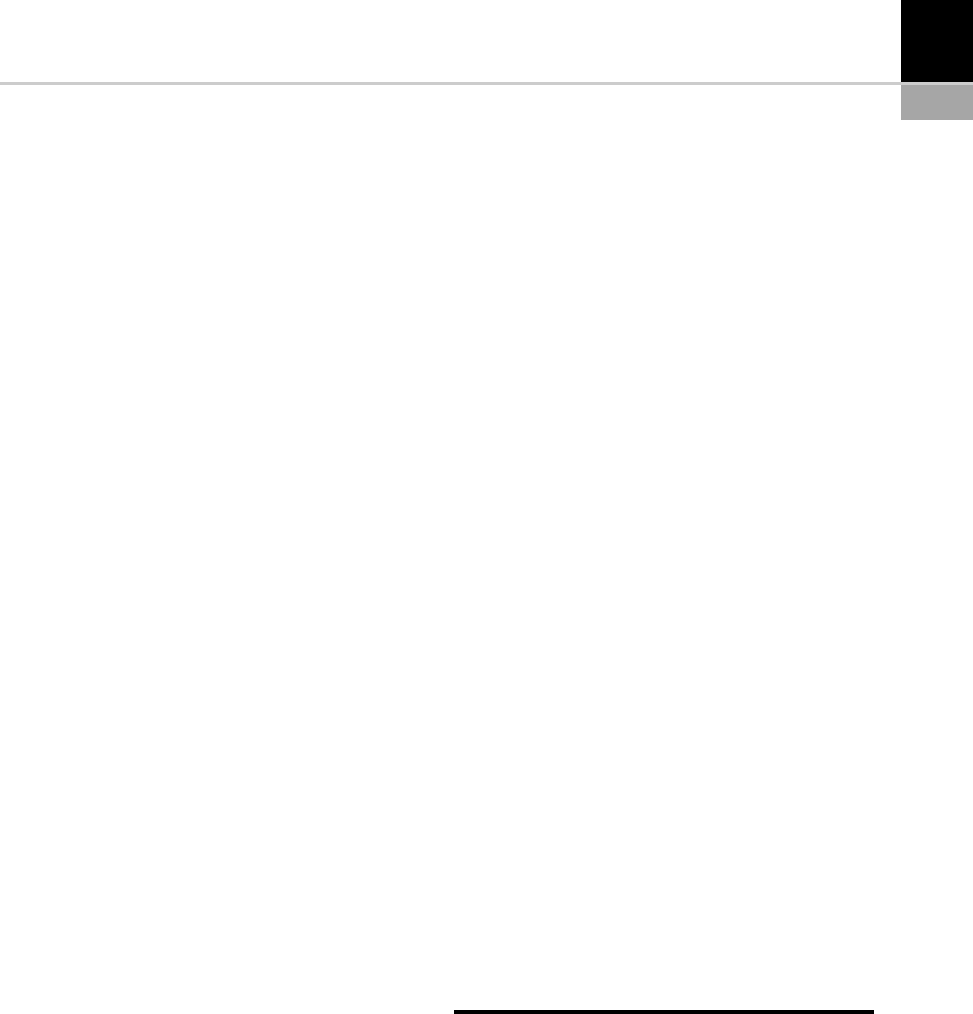
residual layer decreases with packing time. Dur-
ing this molding process, the temperature remains
constant. This isothermal embossing under vac-
uum is required to fill the cavities of the tool
completely. Air inclusions or cooling during mold
filling may result in an incomplete molding of the
microstructures, in particular at high aspect
ratios. Upon the expiry of the packing time, cool-
ing of the tool and substrate starts, while the
embossing force is maintained. Cooling is contin-
ued until the temperature of the mol ded part
drops below the glass transition temperature or
melting point of the plastics. When the demolding
temperature of the polymer is reached, the molded
part is demolded from the tool by relative move-
ment between the tool and the substrate. Demold-
ing only works in connection with an increased
adhesion of the molded part to the substrate plate.
Due to this adhesion, the demolding movement is
transferred homogeneously and vertically to the
molded part. Demolding is the most critical pro-
cess step of hot embossing. Depending on the
selected process parameters and the quality of
the tool, demolding forces may vary by several
factors. In extreme cases, demolding is no longer
possible; the structures are destroyed during
demolding.
Apart from the one-sided molding described,
the process is also used for double- sided posi-
tioned embossing. The principle of the process
remains the same. Instead of the substrate, how-
ever, another tool is applied. To demold the
molded part from one of the two tool halves,
special demolding mechanisms, such as ejector
pins or pressurized-air demolding, are used. For
a better understanding, the schematic representa-
tion of embossing in Fig. 5-2 is limited to the
major process steps. Depending on the tool and
the polymer used, the process and process para-
meters have to be adapted to any changes.
The characteristics and merits of hot emboss-
ing may be summarized as follows:
*
The molding process is characterized by short
flow paths, only from the molten polymer film
into the micro-cavities.
*
Because of the moderate molding velocities in
the range of 1 mm/min only moderate shear
stress in the polymer will be generated. This
results in comparative low residual stress in
the molded parts.
*
If the molding temperature is set to the range
where the relaxation times of a polymer corre-
spond to the cycle times of molding, the stress
induced by molding can be decreased by relax-
ation processes. This opt ion requires knowl-
edge of the temperature dependent relaxation
behavior of the polymer.
*
The use of standardized mold inserts allows
for the quick change of a micro-structured
mold, which underlines the flexibility of the
technology.
*
Beside the quick change of the mold insert, the
polymer can also be changed quickly. Only a
new polymer foil has to be placed between the
mold insert and the substrate plate (Fig. 5.1).
This allows for replicating a mold insert into
several polymers in a short time.
*
The technology allows for a variety of process
variations, for example double-sided molding,
molding of through-holes, multi-layer molding
and also thermoforming of a high temperature
polymer foil by a low temperature polymer melt.
*
Compared to injection molding, the process
may be characterized by longer cycle time.
Although the development shows that with an
effective technology the cycle times could be
reduced, the process is economically well suited
for small and medium series production. Nev-
ertheless, because of the high flexibility this
process can be adapted to several requirements
and it, therefore, is of high potential for the
development of protot ypes within laboratories.
PROCESS VARIATIONS
As mentioned above, hot embossing is not limited
to the case of a single-sided molding cycle. The
concept of hot embossing allows for the process to
be modified according to the requirements of fur-
ther applications of the molded parts. Represen-
tative of a large number of modifications, the
concepts of double-sided molding, multi-layer
molding, the molding of through-holes, and roller
embossing, are described in this section.
CHAPTER 5 Hot Embossing 71