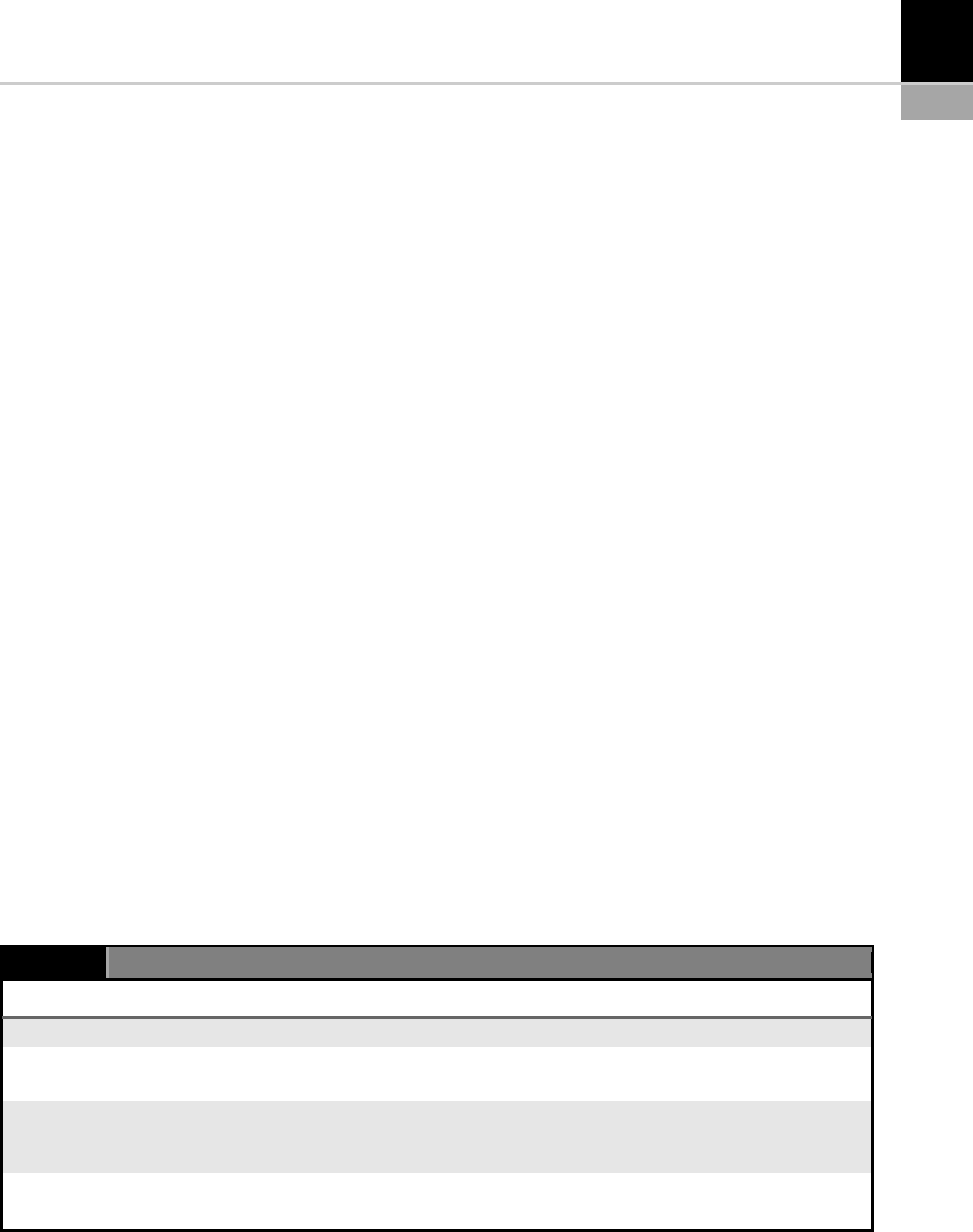
(Fig. 3-3d), micro-electrica l discharge grinding
(m-EDG) (Fig. 3-3e), and micro-wire electrical dis-
charge grinding (m-WEDG) (Fig. 3-3f). m-ED mill-
ing is a further development of m-ED drilling. In
combination with a path controlled motion
in three dimensions, free-forms and cavities can
be produced. This pro cess variant is gaining in
importance for micro-machining because with
this option 3D-shaped tool electrodes do not have
to be manufactured anymore. In analogy towards
the kinematics of conventional grinding pro-
cesses, m-EDG is used for producing, e.g. micro-
fluidic chan nels. For manufacturing, e.g. ejector
pins, m-WEDG is applied.
Dielectric Fluid
The dielectric fluid has several main functions in
the EDM process. It isolates the tool electrode
[11] from the workpiece electrode to achieve a
high current density in the plasma channel. It
cools down the heated surfaces of the electrodes
and exerts a counter pressure to the expanding
plasma channel [12]. Flushing with dielectric fluid
removes the particles after the discharge process
and prevents developing particle linkages causing
process interruptions by short circuit, or damage
of the electrodes’ surfaces [13].
There are two main types of dielectric fluids:
deionized water and dielectric fluids based on
hydrocarbon compounds, also known as dielec-
tric oil.
Deionized water, mostly tap water which was
filtered by deionization re sin to decrease electri-
cal conductivity to k
w
1 mS/cm, has a higher
conductivity and therewith a lower dielectric
strength than hydrocarbon-based dielectric
fluids with k
hdf
< 0.1 mS/cm. Due to the lower
dielectric strength of deionized water, discharge
sparks ignite more easily at bigger working gaps
compared to dielectric oil. The higher vaporiza-
tion heat of water-based dielectric fluids also
removes more thermal energy from the process
than hydrocarbon dielectric fluids. This espe-
cially becomes very important at short discharge
durations and high effective pulse frequencies. In
comparison to dielectric oil, deionized water
effects a higher surface quality [14] and a higher
material removal rate [13].Furthermore,the
influence on the subsurface formation, also
known as white layer, is much lower using deio-
nized water. Disadvantages of water-based
fluids are high tool wear, corrosion of the w ork-
piece, and deionization. Due to the high dielectric
strength, dielectric oil can be used for high dis-
charge energies with small working gaps applied
for micro-die sinking operations. Special disposal
of used oil and contaminated filters, low flash point
and hazardous vapors during the machining pro-
cess are problems when machining with hydro-
carbon dielectric fluids [13]. Table 3-1 gives an
overview of the properties and technological
behavior of hydrocarbon-based dielectric fluids
and deionized water.
TABLE 3-1
Differences of Hydrocarbon Dielectric Fluids and Deionized Water
Type of Dielectric Fluid Hydrocarbon Dielectric Fluids Deionized Water
Electrical conductivity <0.1 mS/cm 1 mS/cm
Technological behavior High material removal rate, small tool
wear, big influence on peripheral zone
High material removal rate, high
surface quality, high wear
Properties No corrosion of workpiece, no
deionization necessary, special disposal,
low flash point, hazardous vapors
Not flammable, no hazardous vapors,
no special disposal, corrosion
Application Micro-die sinking Micro-wire electrical discharge
machining
CHAPTER 3 Micro-EDM 41