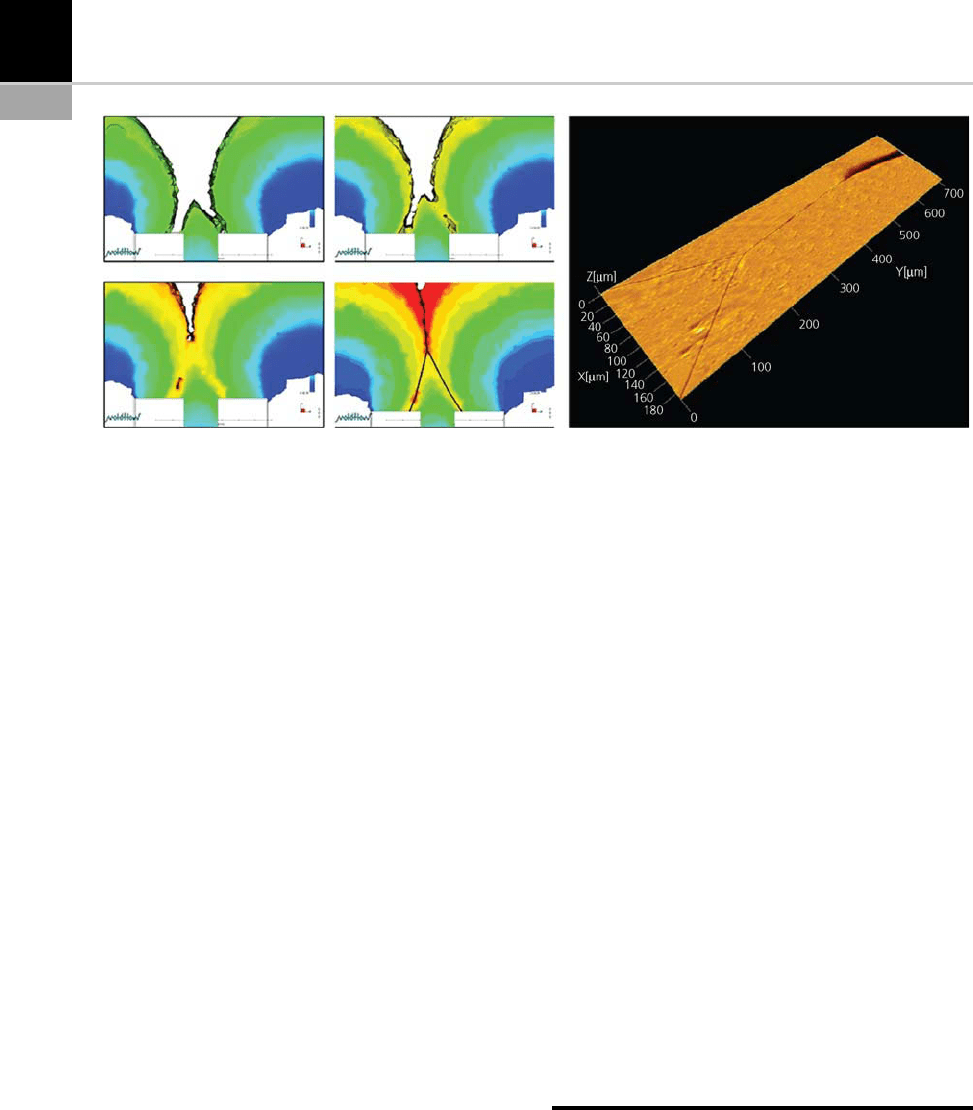
complex components a multiplicity of weld
lines is g enerated. The weld lines are formed as
the mol d is being filled. Weld lines reduce the
mechanical strength of components in the
macro- [22] as well as in the micro- [15] dimen-
sional range. In particular, an area where the
properties are different from the bulk is crea ted.
Weld-line factors (defined as the ratio between
the strength of workpieces containing a weld line
and workpieces with the same geometry but
without weld lines) as lo w as 20% were found
on micro-injection molded tensile strength speci-
mens. The main causes ar e incomplete molecular
entanglement or diffusion, the formation of V-
notches at the weld surface, the pres ence of con-
tamination of micro-voids at the weld-line inter-
face, and unfavorable molecular or fiber orien-
tation at the weld [15].
It is therefore of great importanc e to optimize
the injection molding process, and especially the
filling phase, in order to decre ase such defects. In
particular, injection speed and mold temperature
set at a convenient level can be beneficial in order
to decrease the depth and width of weld lines
(see Figs. 6-29 to 6-31). A higher temperature of
the mold allows a higher molecular mobility
(i.e. lower viscosity) which permits obtaining of
smaller weld lines. Higher injection speed causes a
decrease of the injection time, which has the
consequence of avoiding premature freezing of
the polymer melt, allowing higher mobility of
the polymer at the interface melt front/mold sur-
face. As a conclusion, higher temperature of the
mold and higher injection speed are preferabl e
when molding micro-components with poly-
styrene polymer grade in order to decrease the
importance of weld lines.
Furthermore, the position of the gate with
respect to a considered area of the part with weld
lines is also important. In particular, the longer
the flow length, the larger the weld lines that
will form. Increase of width and depth of 30%
were observed when measuring weld lines far
from the gate compared with weld lines near to
the gate. To this respect, multi-gating solutions
can be employed to shorten the flow length
along the part of the polymer melt during the
filling of the cavity (see Figure 6-32).
PROCESS SIMULATION
Simulation programs in polymer replication
micro-technology are a pplied with the same
purposes as in conventional injection molding.
To avoid the risks of costly re-engineering,
the functions of the final products as well as
FIGURE 6-25 Simulation of the formation of a weld line due to the presence of two micro-features and the meeting of
three melt flow fronts (left) and large-range AFM scanning of the actual meeting area on a polystyrene micro-molded part
(right). The large range scanning of 700 mm 200 mm was obtained using a software tool for stitching three-dimensional
surface topography data sets [20]: 18 different scannings 50 mm 100 mm were employed for the reconstruction [8].
106 CHAPTER 6 Micro-Injection -Molding