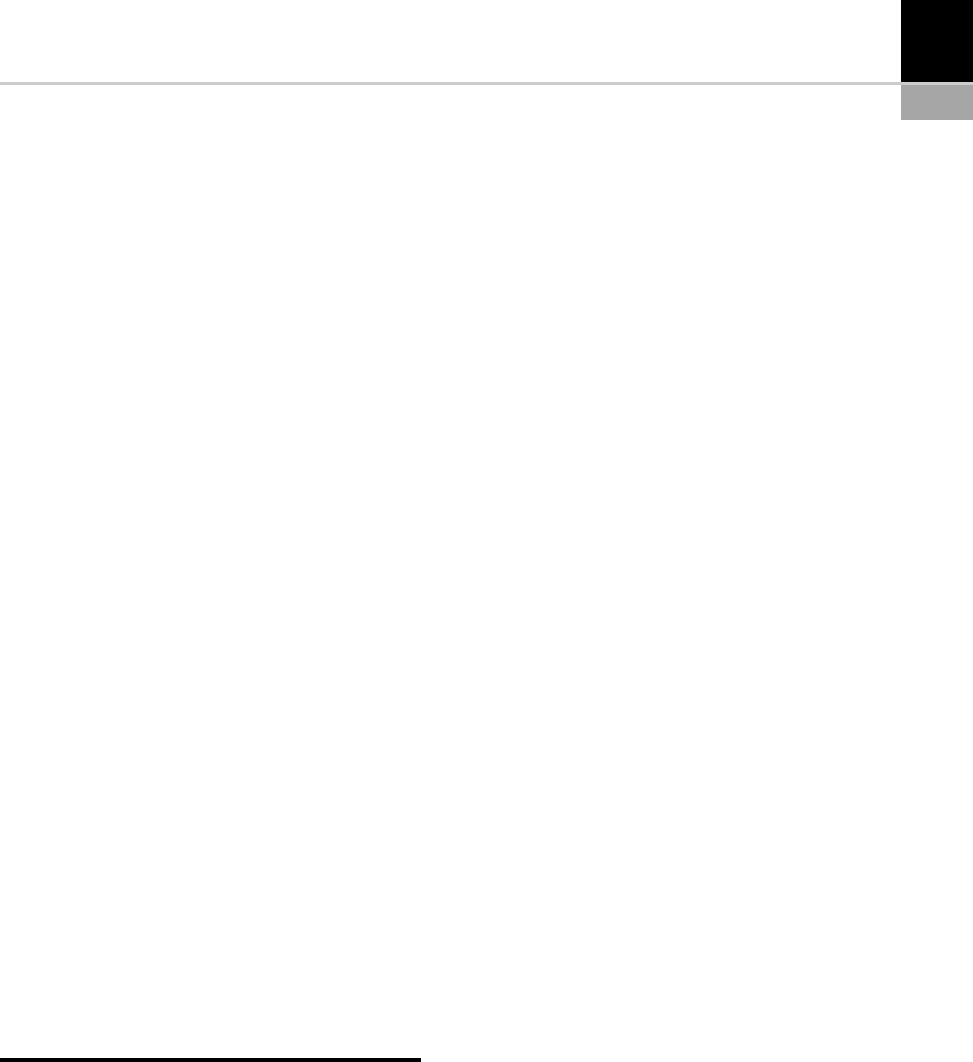
extrusion, with a diameter of about 0.5 mm, must
be able to withstand the total friction force during
ejection. If the friction force is greater than the
yield strength of the component the pin will col-
lapse and reverse forming will occur. The photo-
graph in Fig. 7-13(b) presents an example of
reverse forming of the component: this compo-
nent is the realization of the simulation illustrated
in Fig. 7-13(a) where the forward rod extrusion
has collapsed during ejection. The problem was
resolved by a reduction of the press load, change
of lubricant and polishing of the forming die.
The use and application of lubricants for micro-
bulk forming is at the present time not very
well researched. In convent ional bulk forming,
soaped-phosphate lubricant has been the lubri-
cant of choice for several decades. Unfortunately
this lubricant is unsuitable for micro-bulk form-
ing due to the chemical properties of the lubricant
layer, allowing scaling down only to a certain
thickness. In the example discussed above and
other mi cro-bulk forming experiments at ambient
temperature, the use of a commercial silicon paste
showed good results. However, the application
and removal of the lubricant as well as unintended
confinement of lubricant in the forming die have
been identified as challenges.
For warm forging and the forming of bulk
metallic glasses, a commercial sprayable lubricant
based on MoSO
2
has been utilized. This lubrica-
tion approach worked fairly well and is suitable for
forming at elevated temperatures. A drawback of
utilizing a MoSO
2
-based lubricant is the undesir-
able interaction with the workpiece surface. This
will leave a dark-colored, rough surface which is
difficult to remove and is generally unsuitable for
use in any advanced or medical applications.
PROCESS ANALYSIS
The analysis of the bulk forming process normally
takes place in a dedicated finite element method
(FEM) computer simulation environment. In
practice, the software is solving the underlying
partial differential equations by doing incremen-
tal integration of an approximate set of equations.
Due to the severe deformation of the workpiece in
bulk forming, the software must be capable of
doing accurate remeshing while retaining vo lume
constancy. The process analysis is initiated by
establishing the material parameters. The work-
piece material flow curve is typically acquired by
doing a tensile test or performing an upsetting
test in a universal testing machine. Once the
material data are known, these can be fed into
the material model of the FEM software together
with the tool geometry. If the material is strain-
rate dependent or the process needs to run at high
strain rates, this influence will have to be incl uded
in the model also. This forms the physical basis of
the simulation and the simulation process pro-
ceeds by selection of simulation parameters.
The choice and analysis of simulation para-
meters depend on the type of forging process,
tolerances, simulation accuracy and several other
influencing fact ors. The most important factor,
however, is the number of elements in the simu-
lation, N. The N-factor determines the number of
nodes in the mesh and is thus responsible for the
simulation accuracy. The numb er of calculations
to be done by the computer increases linearly with
N, and thus the number of elements becomes a
trade-off between calculation workload and sim-
ulation accuracy. It is possible to use a zoned mesh
where the user can de fine zones of the workpiece
to have a more refined mesh, typically in areas of
severe deformation.
Another important simulation parameter is the
simulation step size. This is the time (or punch
travel distance) between successive simulation
steps. As in the case of number of elements, a large
number of steps indicate a large calculation work-
load, while a low number of simulations steps will
affect simulation accuracy. However, by taking
notice of the rate of convergence of the simulation
it is possible to choose the right step size within a
few iterations.
For rotationally symmetrical workpieces, such
as bolt, axle or cup geometries, it is possible to
cut down on the calculations by doing a two-
dimensional simulation while retaining the full
validity of the simulation. Even in the case of
three-dimensional geometries it is often possible
to impose symmetry constraints and cut down on
CHAPTER 7 Micro-Bulk-Forming 127