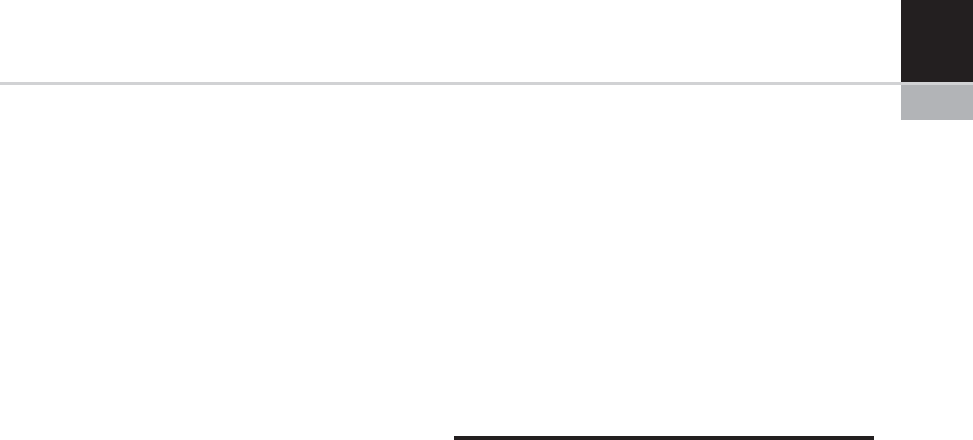
displacement of different features of the sample.
Rough measurements can be done simply by
directly measuring distances with some imaging
software. However, image-analysis tools can do
this with a far greater resolution. Also, through
image-analysis algorithms it is possible to track
features throughout a whole video automatically
in order to construct, for example, a time vs strain
relationship.
There are several algorithms available for
tracking motion in an image sequence. Here, it
will be assumed that an algorithm called c ross-
correlation is employed. For a description of this
algorithm, cf. [12]. This algorithm takes a small
image and a large image as inputs. T he output
will be a map showing how similar the small
image is to each position in the larger one. By
taking the peak value the position of the smaller
image in the larger image is found. This algo-
rithm works even if there is no exact copy of the
small image within the larger. By selecting a
small feature in the first frame of the video and
trying to find this part in the following frames
gives the displacement of this particular feature.
For the c ase of compressive or tensile tests, if
two features that are close to the ends of the
sample are tracked the strain can be calculated.
This strain will be entirely independent of instru-
ment compliance. As menti oned above, strain is
not the only property that can be measured from
the images. For example, by tracking several
parts on the samples, buckling and lateral
expansion of the samples can be measured.
The cross-correlation algorithm can be
improved, making it possible to track changes
with a sub-pixel resolution , provided that the
image is well focused and that the level of noise
is low. This is important, because the total size of
an image is often about 500 pixels in width. In this
case one single pixel corresponds to 0.2% strain
assuming that the sample covers the whole image.
This low resolution would normally be consid-
ered insufficient.
When working close to the resolution limit of
an SEM, the signal is usually very weak, requiring
a very long integration time for each image. In this
case, the acquisition time for a single frame can be
several seconds. It must therefore be taken into
account also that different parts of the image are
scanned at different times, usually starting from
the top and ending at the bottom.
CASE STUDY: A COMPARISON OF
IN-SITU MICRO-TENSION AND
MICRO-COMPRESSION FOR
STUDYING THE PLASTIC
PROPERTIES OF NANO-
CRYSTALLINE ELECTRODEPOSITED
NICKEL AT DIFFERENT LENGTH
SCALES
In order to evaluate the effects of grain size or
geometrical constraints on measured mechanical
properties, there is a need to understand the influ-
ence of the measurement technique, load distribu-
tion, strain rate, etc., on the measurement values
and to correlate the measurements with deforma-
tion mechanisms. Uniaxial in-situ methods are
interesting tools for this purpose. In the following
case study a comparison of in-situ and ex-situ
micro-compression with in-situ micro-tensile tests
is shown; all the tests being used to study the
mechanical properties of electrodeposited nano-
crystalline (nc) nickel. As the material is nano-
crystalline, it would be expected that the size of
the probed volume does not influence the mechan-
ical properties as long as it is at least of the order
of a cubic micrometer. Micro-tensile tests that
probe a volume of more than 2.10
6
mm
3
show
reasonable agreement with results from micro-
compression tests that probe much smaller
volumes of down to a few mm
3
. In-situ uniaxial
solicitation in compression mode reveals several
advantages for studying stress/strain properties.
In the same way as for tensile meas urements, a
quantitative evaluation of the deformation during
compression through video frame records [13]
was found possible.
The material investigated was electrodeposited
nano-crystalline (nc) nickel. Figure 21-9 shows an
HRSEM picture of the nc Ni surface. The sizes of
the grains vary between 30 and 200 nm with an
average of 50 nm. The inset in Fig. 21-9 displays a
TEM cross-section of the film. The grains have a
CHAPTER 21 In-situ Testing of Mechanical Properties of Materials 339