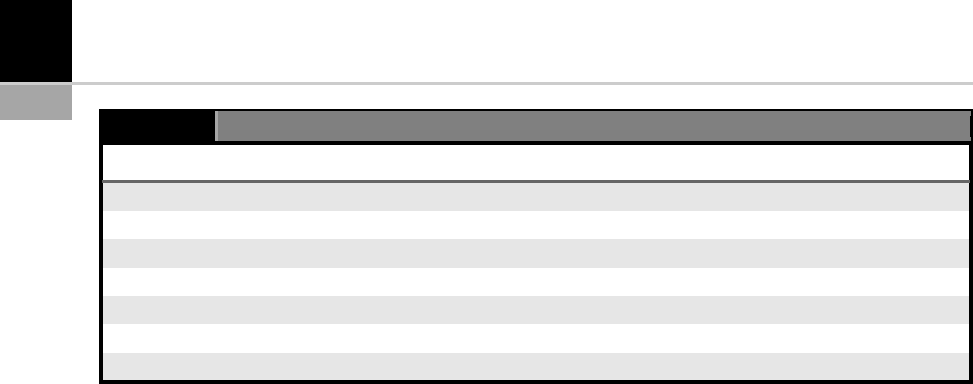
material. Typical data of commercially available
laser sources are listed in Table 12-3.
Pulsed flashlamp pumped Nd:YAG lasers offer
some advantages compared to continuously emit-
ting (cw) Nd:YAG lasers:
*
High maximum pulse power at moderate aver-
age power;
*
Better beam quality;
*
Affordable investment costs and low cost-of-
ownership;
*
Lower requirements for cooling;
*
Steeper slopes for pulse rise time;
*
Pulse forming capability.
The applicability of optical fibers to guide the
laser light offers new possibilities for industrial
use within manufacturing equipment. The sepa-
ration of the laser source itself and the working
head inside the machine or even the possibility
of using one laser source for different machines
by energy-sharing or time-sharing mechanisms.
By means of this the use of lasers becomes more
economic.
The new sources, e.g. fiber lasers, now combine
better beam quality with reduced costs.
Beam Delivery
For Nd:YAG lasers, there are two possible ways
for beam delivery: direct beam and fiber delivery
[10]. The beam quality of a direct beam (BPP 8–
20 mm mrad) is better than the beam qua lity of a
fiber guided system (BPP 15–30 mm mrad). The
intensity distribution of a direct beam is normally
a Gaussian distribution, whereas the fiber guided
system has a top-hat distribution. Thus the Gauss-
ian distribution can be focused better to smaller
beam diameter.
A disadvantage of Nd:YAG rod lasers is the
influence of the thermal lens. Beam quality and
intensity distribution are dependent on duty cycle,
pulse duration and laser power. They also can
change from pulse to pulse as well as within one
pulse. Therefore a laser beam guided through an
optical fiber by multiple reflections is homoge-
nized. Beam quality and intensity distribution
are predetermined by the diam eter of the fiber
and its NA an d vary only slightly. Further more,
the maximum temperature of the weld bead using
a Gaussian distribution is normally higher, so the
top-hat distribution is normally more appropriate
for laser beam welding.
The positioning of the beam can be made, by
using a Cartesian positioning system, to move the
workpiece or by moving the beam by means of a
galvanometer scanner (Fig. 12-11).
Typical applications of laser beam micro--
welding are dealing with wires and thin sheets
ranging from several tens of microns to 1 milli-
meter in thickness. The diameter of the laser beam
should be of the dimension of the thickness of the
parts to be welded, although in certain appli-
cations it can be larger. Sometimes the parts are
already placed in a polymer housing (e.g. a pre-
molded package). Here it has to be taken account
that the housing material must not be influence
by diverging laser radiation or by the heat created
by the joining process. The main materials are
steel and coated and uncoated copper alloys.
TABLE 12-3
Typical Specifications of Pulsed Nd:YAG Laser Sources and Fiber Lasers
Pulsed Nd:YAG Fiber Laser
Average power 10–400 100–200
Pulse power (kW) 1–7 –
Pulse energy (J) 1–50 –
Pulse duration (ms) 0.1–20 Cw
Beam quality (mm mrad) 8–16 0.4
Beam diameter (mm) 50–400 35
Fiber diameter (mm) 100–500 10–50
194
CHAPTER 12 Laser Beam Micro-Joining