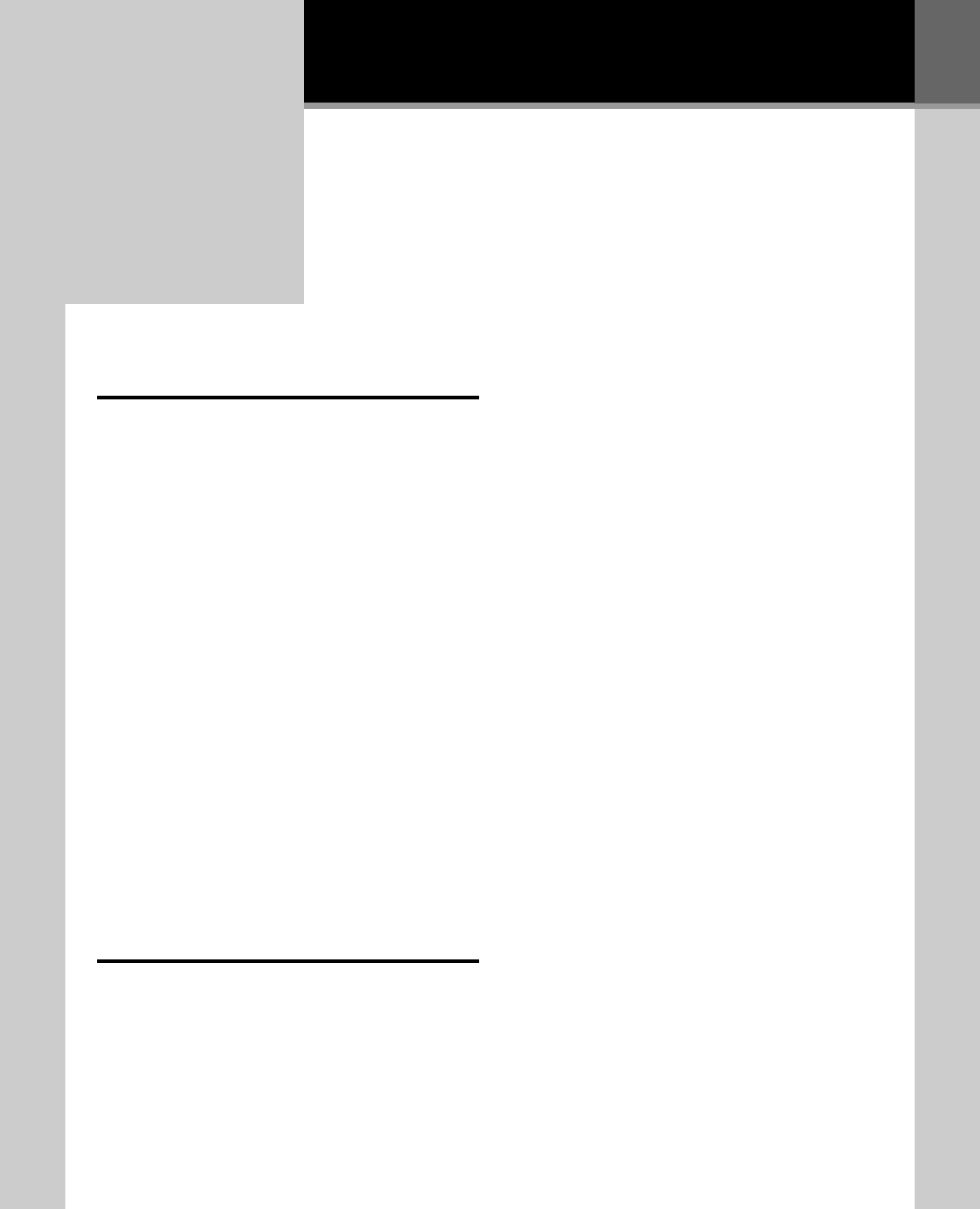
10
Laser-Assisted Micro-Forming
Jens Holtkamp
INTRODUCTION
Forming is one of the basic production technologies,
and due to the potential and low costs of the process
is widely spread in industrial applications. Never-
theless, there are specific limitations regarding the
workpiece materials and the maximum strain
within the forming operation. Brittle and high
strength materials cannot be accommodated with-
out high process complexity or low product quality.
By heating the used materials prior to the form-
ing process, with the corresponding change of
their material properties, these drawbacks can
be eliminated.
The use of laser radiation as the heat source
enables short heating times, due to the associated
high energy density. In addition, there are other
advantages such as contactless heating, good focu-
sability and good controllability lasers are therefore
becoming a promising alternative to existing tech-
nologies such as induction or conductive heating.
In principle, every forming technique can be
enhanced by laser technology. The basics for its
integration and some exemplified processes are
described in the following sections.
SYSTEM TECHNOLOGY
Heating of the workpiece can be achieved by dif-
ferent methods: conductive through the contact of
a heated tool, convective within a convection
oven, or inductive by swirling currents generated
in the material.
Pre-process heating of the workpiece outside of
the tool leads to an increase of temperature within
the whole part. Temperature gradients are not
adjustable; therefore, local heating of selected areas
of the part is not possible. Heating of micro-
components is difficult due to their low mass. This
lowheatcapacityleadstoacoolingdownafterthe
transport into and the contact with the tool.
The disadvantage of methods based on heat
convection is the bad controllability of the form-
ing temperature and the resulting long cycle times.
Similarly to the pre-heating method, the heating
of local areas of the workpiece is not possible.
By using a laser as the heat source, the induced
energy and the resul ting temperatures can be eas-
ily controlled by laser power. Heating of selected
areas is possible by forming the laser beam. The
high energy density of the radiation and the direct
absorption enable short cycle times. Therefore, a
laser is a promising tool to achieve the potential of
micro-forming at elevated temperatures.
The laser system causes the main additional
cost in comparison to the cost of conventional
machinery. Due to its low pric e in comparison
with that of other laser systems, a diode laser is
often favored, but there are also other effective
systems such as fiber lasers. If absorpt ion within
transparent workpieces is intended, the wave-
length of the laser has to be adapted.
The machinery used for laser-assisted pro-
cesses is based on conventional forming machines.
The system is then, beside the laser itself,
enhanced with components for the integration
and control of the laser. One basic additional ele-
ment is an optical system which is placed inside
the tool. Adapted to a fiber which conn ects the
CHAPTER
162