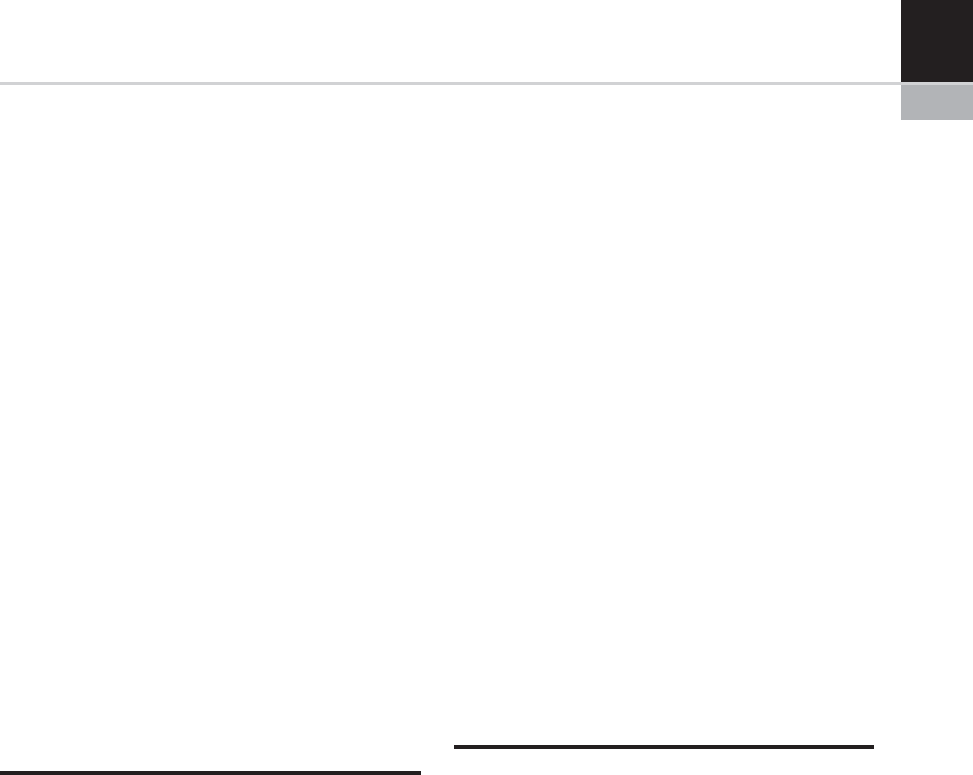
a well-established non-silicon alternative micro-
fabrication technology for MEMS.
LIGA technology provides unique advantages
over other manufacturing methods in the fabrica-
tion of micro-structures. LIGA-based technolo-
gies are used and are being further developed in
a number of R&D institutes around the world.
Spin-off companies and commercial companies
have also evolved around large-scale synchrotron
facilities. Also, commercial applications of the
LIGA process are on the market. LIGA technol-
ogy has been developed over the rather long time
span of two decades [1–4]. During this time other
high aspect ratio technologies such as UV photo-
lithography in thick resist, for example as SU-8,
often referred to as UV -LIGA, and Deep Reactive
Ion Etching (DRIE) of silicon have also evolv ed
and challenged LIGA successfully in some specific
application areas. For planning the role of LIGA
in future manufacturing, a review of potential
applications may serve as a useful basis. The basic
LIGA process and some aspects of the process are
recalled here to illustrate its strengths and discuss
still existing challenges.
THE LIGA PROCESS AND ITS
STRENGTHS
The basic LIGA process is described in Fig. 13-1 .
In the first step of the process, an X-ray-sensitive
polymer (resist) layer of up to several mi llimeters
thickness is coated onto a conductive or non-
conductive substrate. Typically polymethylmetha-
crylate (PMMA) is used as positive resist and an
epoxy-based resist SU-8 [5–9] as negative resist. A
pattern from a mask is then transferred into the
thick resist layer via a 1:1 shadow-proximity print-
ing scheme using hard X-rays from a synchrotron
radiation source. After exposure, selective disso-
lution of the chemically modified irradiated parts
of the positive resist (or dissolution of the non-
irradiated parts of the negative resist) in a chemical
developer results in a polymeric relief replica of the
mask pattern.
Then, depending on the material, number of
parts selected for the final product, accuracy,
quality and price, different fabrication routes
can be chosen, which may include further steps
of mi cro-replication through electroforming and/
or a variety of molding techniques (injection
molding, embossing, casting, compression mold-
ing, etc.). The polymeric micro-structure can be
used:
*
simply as it is;
*
as a lost mold for the formation of ceramic
micro-parts;
*
as an electroplating template to generate metal-
lic micro-parts;
*
as an ele ctroplating template to prod uce a
metallic master-mold, which can then be used
many times to mold cost-effective replicas in
other materials, primarily polymers. When
producing large numbers of electroplated com-
ponents, the molded polymer parts are used as
lost molds for a second plating pro cess.
The unique processing feature that enables the
manufacture of thick micro-structures character-
ized by very steep walls and very tight tolerances is
the creation of a high precision resist template by
deep X-ray lithography using X-ray photons from
a synchrotron radiation source.
LIGA MANUFACTURING STEPS
Resist Technology
The resist technology consists of applyin g a resist
onto a substrate, the substrates that can be used
depend on the product to be made (for example, a
mold insert), but they should meet the following
criteria:
*
a high planarity;
*
the substrate and resist should have good adhe-
sion;
*
the substrate surface should be conductive if an
electroplating step is needed;
*
the resist developer should not etch the sub-
strate.
Concerning the resist, a distinction should be
made between positive and negative resist. In the
first case, the radiation will da mage the polymer
by reducing its molecular weight; the most com-
monly used being polymethylmetacrylate
(PMMA); the irradiates parts becom ing soluble
CHAPTER 13 Deep X-Ray Lithography 203