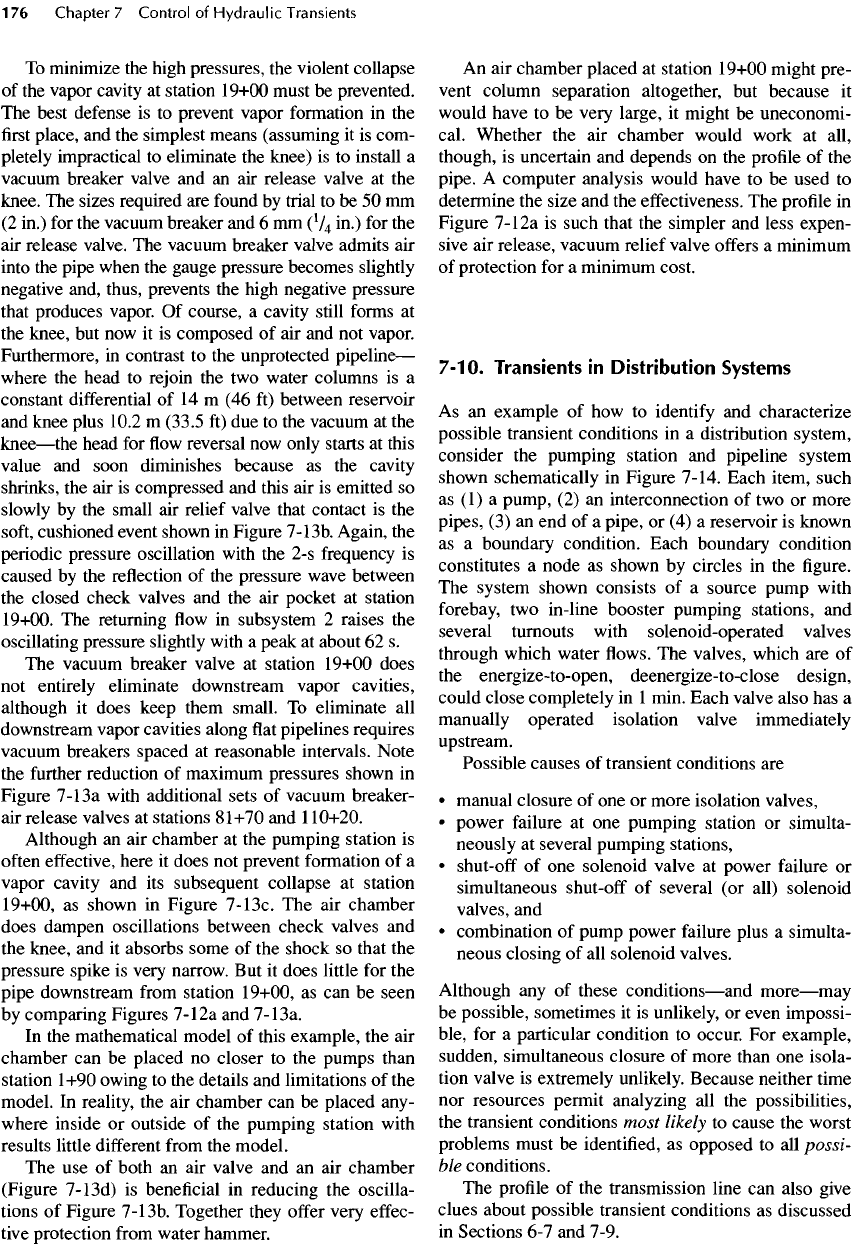
To
minimize
the
high pressures,
the
violent collapse
of
the
vapor
cavity
at
station
19+00
must
be
prevented.
The
best defense
is to
prevent vapor formation
in the
first
place,
and the
simplest means (assuming
it is
com-
pletely impractical
to
eliminate
the
knee)
is to
install
a
vacuum
breaker valve
and an air
release valve
at the
knee.
The
sizes required
are
found
by
trial
to be 50 mm
(2
in.)
for the
vacuum breaker
and 6 mm
(
1
^
in.)
for the
air
release valve.
The
vacuum
breaker valve admits
air
into
the
pipe when
the
gauge pressure becomes slightly
negative
and, thus, prevents
the
high negative pressure
that
produces vapor.
Of
course,
a
cavity still
forms
at
the
knee,
but now it is
composed
of air and not
vapor.
Furthermore,
in
contrast
to the
unprotected
pipeline
—
where
the
head
to
rejoin
the two
water columns
is a
constant
differential
of 14 m (46 ft)
between reservoir
and
knee plus 10.2
m
(33.5
ft) due to the
vacuum
at the
knee
—
the
head
for flow
reversal
now
only starts
at
this
value
and
soon diminishes because
as the
cavity
shrinks,
the air is
compressed
and
this
air is
emitted
so
slowly
by the
small
air
relief valve that contact
is the
soft,
cushioned event shown
in
Figure
7-13b.
Again,
the
periodic pressure oscillation
with
the 2-s
frequency
is
caused
by the
reflection
of the
pressure wave between
the
closed check valves
and the air
pocket
at
station
19+00.
The
returning
flow in
subsystem
2
raises
the
oscillating pressure slightly
with
a
peak
at
about
62 s.
The
vacuum breaker valve
at
station 19+00 does
not
entirely eliminate downstream vapor cavities,
although
it
does
keep them small.
To
eliminate
all
downstream vapor cavities along
flat
pipelines requires
vacuum
breakers spaced
at
reasonable intervals. Note
the
further
reduction
of
maximum pressures shown
in
Figure
7-13a
with additional sets
of
vacuum breaker-
air
release valves
at
stations
81+70
and
1
10+20.
Although
an air
chamber
at the
pumping station
is
often
effective,
here
it
does
not
prevent formation
of a
vapor cavity
and its
subsequent collapse
at
station
19+00,
as
shown
in
Figure
7-13c.
The air
chamber
does dampen oscillations between check valves
and
the
knee,
and it
absorbs some
of the
shock
so
that
the
pressure spike
is
very narrow.
But it
does little
for the
pipe downstream
from
station 19+00,
as can be
seen
by
comparing Figures
7-12a
and
7-13a.
In
the
mathematical model
of
this example,
the air
chamber
can be
placed
no
closer
to the
pumps than
station
1+90 owing
to the
details
and
limitations
of the
model.
In
reality,
the air
chamber
can be
placed any-
where
inside
or
outside
of the
pumping station with
results
little
different
from
the
model.
The use of
both
an air
valve
and an air
chamber
(Figure
7-
13d)
is
beneficial
in
reducing
the
oscilla-
tions
of
Figure
7-13b.
Together they
offer
very
effec-
tive
protection
from
water hammer.
An
air
chamber placed
at
station
19+00
might pre-
vent
column separation altogether,
but
because
it
would have
to be
very large,
it
might
be
uneconomi-
cal. Whether
the air
chamber would work
at
all,
though,
is
uncertain
and
depends
on the
profile
of the
pipe.
A
computer analysis would have
to be
used
to
determine
the
size
and the
effectiveness.
The
profile
in
Figure
7-12a
is
such that
the
simpler
and
less expen-
sive
air
release, vacuum relief valve
offers
a
minimum
of
protection
for a
minimum cost.
7-10.
Transients
in
Distribution
Systems
As an
example
of how to
identify
and
characterize
possible transient conditions
in a
distribution system,
consider
the
pumping station
and
pipeline system
shown
schematically
in
Figure 7-14. Each item, such
as (1) a
pump,
(2) an
interconnection
of two or
more
pipes,
(3) an end of a
pipe,
or (4) a
reservoir
is
known
as
a
boundary condition. Each boundary condition
constitutes
a
node
as
shown
by
circles
in the figure.
The
system shown consists
of a
source pump with
forebay,
two
in-line booster pumping stations,
and
several turnouts with solenoid-operated valves
through
which water
flows. The
valves, which
are of
the
energize-to-open,
deenergize-to-close
design,
could
close
completely
in 1
min.
Each valve also
has a
manually
operated isolation valve immediately
upstream.
Possible causes
of
transient conditions
are
•
manual closure
of one or
more
isolation
valves,
•
power
failure
at one
pumping station
or
simulta-
neously
at
several pumping stations,
•
shut-off
of one
solenoid valve
at
power
failure
or
simultaneous
shut-off
of
several
(or
all) solenoid
valves,
and
•
combination
of
pump power
failure
plus
a
simulta-
neous closing
of all
solenoid valves.
Although
any of
these
conditions
—
and
more
—
may
be
possible, sometimes
it is
unlikely,
or
even impossi-
ble,
for a
particular condition
to
occur.
For
example,
sudden, simultaneous closure
of
more than
one
isola-
tion valve
is
extremely unlikely. Because neither time
nor
resources permit analyzing
all the
possibilities,
the
transient conditions most
likely
to
cause
the
worst
problems must
be
identified,
as
opposed
to all
possi-
ble
conditions.
The
profile
of the
transmission
line
can
also
give
clues about possible transient conditions
as
discussed
in
Sections
6-7 and
7-9.