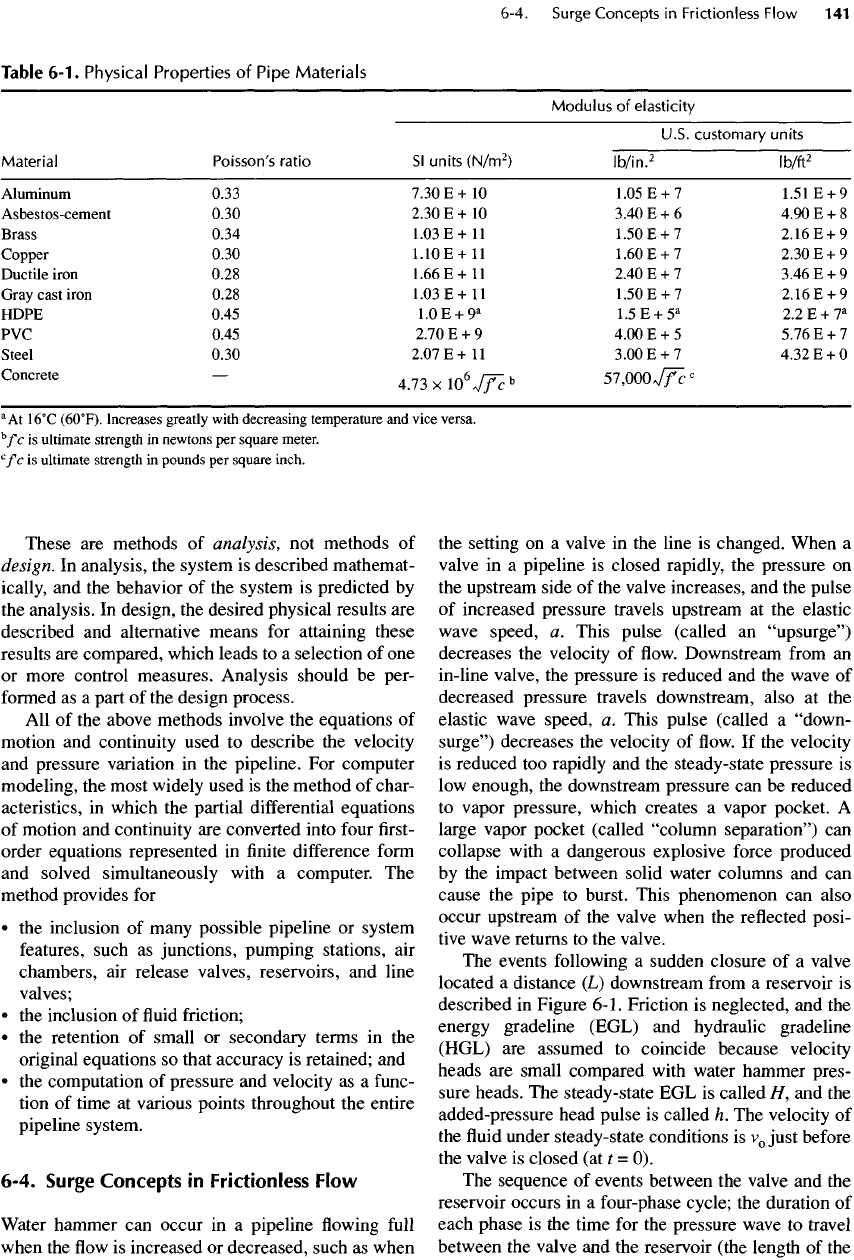
These
are
methods
of
analysis,
not
methods
of
design.
In
analysis,
the
system
is
described mathemat-
ically,
and the
behavior
of the
system
is
predicted
by
the
analysis.
In
design,
the
desired physical results
are
described
and
alternative means
for
attaining these
results
are
compared, which leads
to a
selection
of one
or
more control measures. Analysis should
be
per-
formed
as a
part
of the
design process.
All
of the
above methods involve
the
equations
of
motion
and
continuity used
to
describe
the
velocity
and
pressure variation
in the
pipeline.
For
computer
modeling,
the
most widely used
is the
method
of
char-
acteristics,
in
which
the
partial
differential
equations
of
motion
and
continuity
are
converted into
four
first-
order equations represented
in finite
difference
form
and
solved simultaneously with
a
computer.
The
method
provides
for
• the
inclusion
of
many possible pipeline
or
system
features,
such
as
junctions, pumping stations,
air
chambers,
air
release valves, reservoirs,
and
line
valves;
• the
inclusion
of fluid
friction;
• the
retention
of
small
or
secondary terms
in the
original equations
so
that accuracy
is
retained;
and
• the
computation
of
pressure
and
velocity
as a
func-
tion
of
time
at
various points throughout
the
entire
pipeline system.
6-4. Surge
Concepts
in
Frictionless
Flow
Water
hammer
can
occur
in a
pipeline
flowing
full
when
the flow is
increased
or
decreased, such
as
when
the
setting
on a
valve
in the
line
is
changed. When
a
valve
in a
pipeline
is
closed rapidly,
the
pressure
on
the
upstream side
of the
valve increases,
and the
pulse
of
increased pressure travels upstream
at the
elastic
wave
speed,
a.
This
pulse (called
an
"upsurge")
decreases
the
velocity
of flow.
Downstream
from
an
in-line valve,
the
pressure
is
reduced
and the
wave
of
decreased pressure travels downstream, also
at the
elastic wave speed,
a.
This pulse (called
a
"down-
surge")
decreases
the
velocity
of flow. If the
velocity
is
reduced
too
rapidly
and the
steady-state pressure
is
low
enough,
the
downstream pressure
can be
reduced
to
vapor pressure, which creates
a
vapor pocket.
A
large vapor pocket (called "column
separation")
can
collapse with
a
dangerous explosive force produced
by
the
impact between solid water columns
and can
cause
the
pipe
to
burst. This phenomenon
can
also
occur upstream
of the
valve when
the
reflected posi-
tive wave returns
to the
valve.
The
events following
a
sudden closure
of a
valve
located
a
distance
(L)
downstream
from
a
reservoir
is
described
in
Figure
6-1.
Friction
is
neglected,
and the
energy gradeline (EGL)
and
hydraulic gradeline
(HGL)
are
assumed
to
coincide because velocity
heads
are
small compared with water hammer pres-
sure heads.
The
steady-state
EGL is
called
//,
and the
added-pressure head pulse
is
called
h. The
velocity
of
the fluid
under steady-state conditions
is
V
0
just before
the
valve
is
closed
(at t = O).
The
sequence
of
events between
the
valve
and the
reservoir occurs
in a
four-phase cycle;
the
duration
of
each phase
is the
time
for the
pressure wave
to
travel
between
the
valve
and the
reservoir (the length
of the
Table
6-1.
Physical
Properties
of
Pipe
Materials
Modulus
of
elasticity
U.S.
customary units
Material
Poisson's
ratio
Sl
units (N/m
2
)
Ib/in.
2
Ib/ft
2
Aluminum
0.33
7.30
E+10
1.05
E + 7
1.51
E + 9
Asbestos-cement
0.30
2.30
E+10
3.4OE+
6
4.9OE
+8
Brass 0.34
1.03
E+11
1.5OE+
7
2.16E
+9
Copper
0.30
1.10
E+11
1.60
E
+7
2.3OE+
9
Ductile iron 0.28
1.66
E
+11
2.40
E + 7
3.46
E + 9
Gray
cast
iron 0.28
1.03
E+11
1.5OE+
7
2.16E+
9
HDPE 0.45
1.0 E +
9
a
1.5 E +
5
a
2.2 E +
7
a
PVC
0.45
2.7OE
+9
4.0OE+
5
5.76E
+ 7
Steel
0.30
2.07
E+11
3.00
E
+7
4.32
E
+O
Concrete
-
4
73
x
1Q
6^
b
57,000^
c
a
At
16
0
C
(6O
0
F).
Increases greatly
with
decreasing temperature
and
vice versa.
b
fc
is
ultimate
strength
in
newtons
per
square
meter.
c
/c
is
ultimate strength
in
pounds
per
square inch.