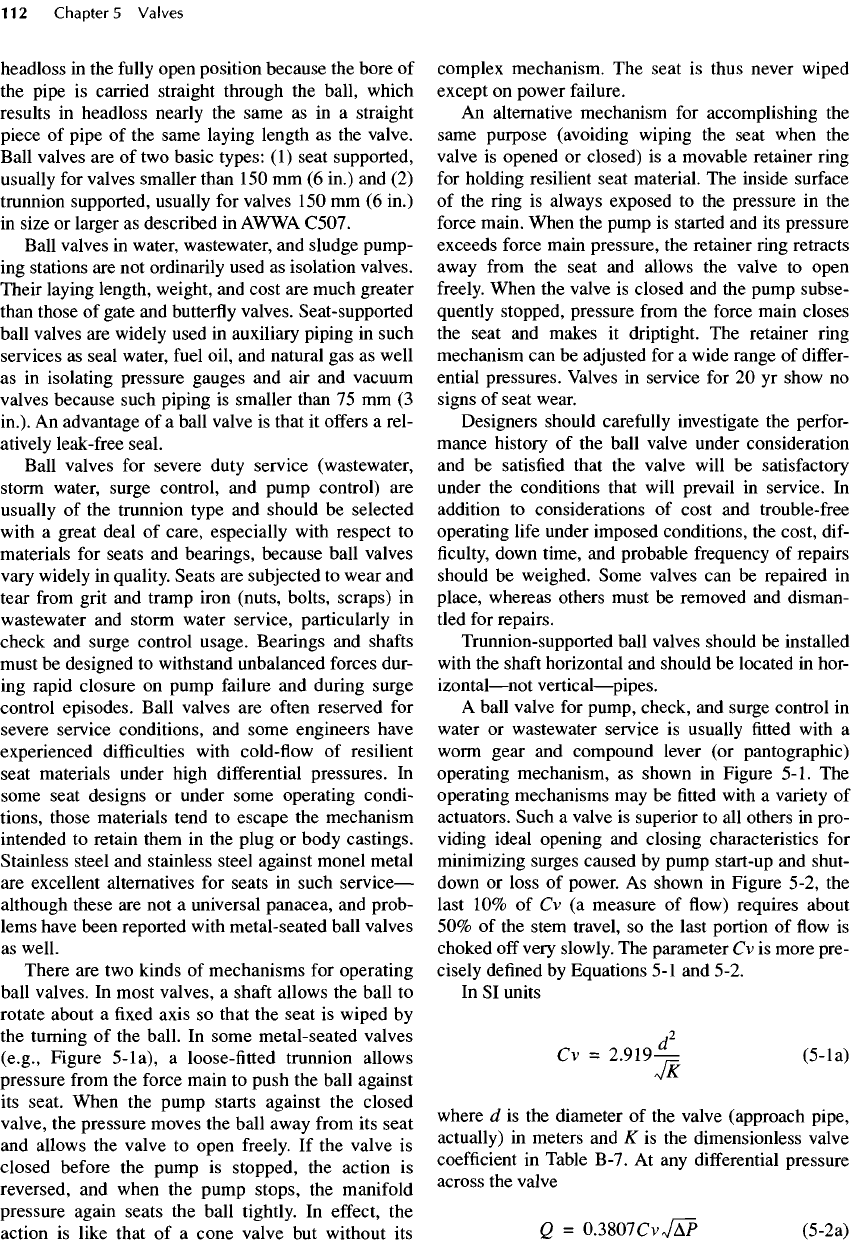
headless
in the
fully
open position because
the
bore
of
the
pipe
is
carried straight through
the
ball, which
results
in
headloss nearly
the
same
as in a
straight
piece
of
pipe
of the
same laying length
as the
valve.
Ball valves
are of two
basic types:
(1)
seat supported,
usually
for
valves smaller
than
150
mm (6
in.)
and (2)
trunnion
supported, usually
for
valves
150 mm (6
in.)
in
size
or
larger
as
described
in
AWWA
C507.
Ball
valves
in
water, wastewater,
and
sludge pump-
ing
stations
are not
ordinarily used
as
isolation valves.
Their laying length, weight,
and
cost
are
much greater
than
those
of
gate
and
butterfly
valves. Seat-supported
ball valves
are
widely used
in
auxiliary piping
in
such
services
as
seal water,
fuel
oil,
and
natural
gas as
well
as in
isolating pressure gauges
and air and
vacuum
valves
because such piping
is
smaller than
75 mm (3
in.).
An
advantage
of a
ball valve
is
that
it
offers
a
rel-
atively
leak-free seal.
Ball valves
for
severe duty service (wastewater,
storm
water, surge control,
and
pump control)
are
usually
of the
trunnion type
and
should
be
selected
with
a
great deal
of
care, especially with respect
to
materials
for
seats
and
bearings, because ball valves
vary
widely
in
quality. Seats
are
subjected
to
wear
and
tear
from
grit
and
tramp iron (nuts, bolts, scraps)
in
wastewater
and
storm water service, particularly
in
check
and
surge control usage. Bearings
and
shafts
must
be
designed
to
withstand unbalanced forces dur-
ing
rapid closure
on
pump failure
and
during surge
control
episodes.
Ball valves
are
often
reserved
for
severe service conditions,
and
some engineers have
experienced
difficulties
with
cold-flow
of
resilient
seat materials under high
differential
pressures.
In
some seat designs
or
under some operating condi-
tions, those materials tend
to
escape
the
mechanism
intended
to
retain them
in the
plug
or
body castings.
Stainless steel
and
stainless steel against
monel
metal
are
excellent alternatives
for
seats
in
such
service
—
although
these
are not a
universal panacea,
and
prob-
lems have been reported with metal-seated ball valves
as
well.
There
are two
kinds
of
mechanisms
for
operating
ball valves.
In
most valves,
a
shaft
allows
the
ball
to
rotate about
a fixed
axis
so
that
the
seat
is
wiped
by
the
turning
of the
ball.
In
some metal-seated valves
(e.g., Figure
5-
Ia),
a
loose-fitted trunnion allows
pressure
from
the
force main
to
push
the
ball against
its
seat. When
the
pump starts against
the
closed
valve,
the
pressure moves
the
ball
away
from
its
seat
and
allows
the
valve
to
open
freely.
If the
valve
is
closed before
the
pump
is
stopped,
the
action
is
reversed,
and
when
the
pump stops,
the
manifold
pressure again seats
the
ball tightly.
In
effect,
the
action
is
like that
of a
cone valve
but
without
its
complex mechanism.
The
seat
is
thus never wiped
except
on
power failure.
An
alternative mechanism
for
accomplishing
the
same
purpose (avoiding wiping
the
seat when
the
valve
is
opened
or
closed)
is a
movable retainer ring
for
holding resilient seat material.
The
inside
surface
of
the
ring
is
always exposed
to the
pressure
in the
force
main. When
the
pump
is
started
and its
pressure
exceeds force main pressure,
the
retainer ring retracts
away
from
the
seat
and
allows
the
valve
to
open
freely.
When
the
valve
is
closed
and the
pump subse-
quently
stopped, pressure
from
the
force main closes
the
seat
and
makes
it
driptight.
The
retainer ring
mechanism
can be
adjusted
for a
wide range
of
differ-
ential pressures. Valves
in
service
for 20 yr
show
no
signs
of
seat wear.
Designers should
carefully
investigate
the
perfor-
mance history
of the
ball valve under consideration
and
be
satisfied that
the
valve will
be
satisfactory
under
the
conditions that will prevail
in
service.
In
addition
to
considerations
of
cost
and
trouble-free
operating
life
under imposed conditions,
the
cost, dif-
ficulty,
down
time,
and
probable frequency
of
repairs
should
be
weighed. Some valves
can be
repaired
in
place, whereas others must
be
removed
and
disman-
tled
for
repairs.
Trunnion-supported ball valves should
be
installed
with
the
shaft
horizontal
and
should
be
located
in
hor-
izontal
—
not
vertical
—
pipes.
A
ball valve
for
pump, check,
and
surge control
in
water
or
wastewater service
is
usually
fitted
with
a
worm
gear
and
compound lever
(or
pantographic)
operating mechanism,
as
shown
in
Figure 5-1.
The
operating mechanisms
may be fitted
with
a
variety
of
actuators. Such
a
valve
is
superior
to all
others
in
pro-
viding
ideal opening
and
closing characteristics
for
minimizing
surges caused
by
pump start-up
and
shut-
down
or
loss
of
power.
As
shown
in
Figure 5-2,
the
last
10% of Cv (a
measure
of flow)
requires about
50% of the
stem travel,
so the
last portion
of flow is
choked
off
very slowly.
The
parameter
Cv is
more pre-
cisely
defined
by
Equations
5-1
and
5-2.
In
SI
units
,2
Cv
=
2.919-yr
(5-la)
*]K
where
d is the
diameter
of the
valve (approach pipe,
actually)
in
meters
and K is the
dimensionless valve
coefficient
in
Table
B
-7.
At any
differential pressure
across
the
valve
Q
=
0.3807CvVAP
(5-2a)