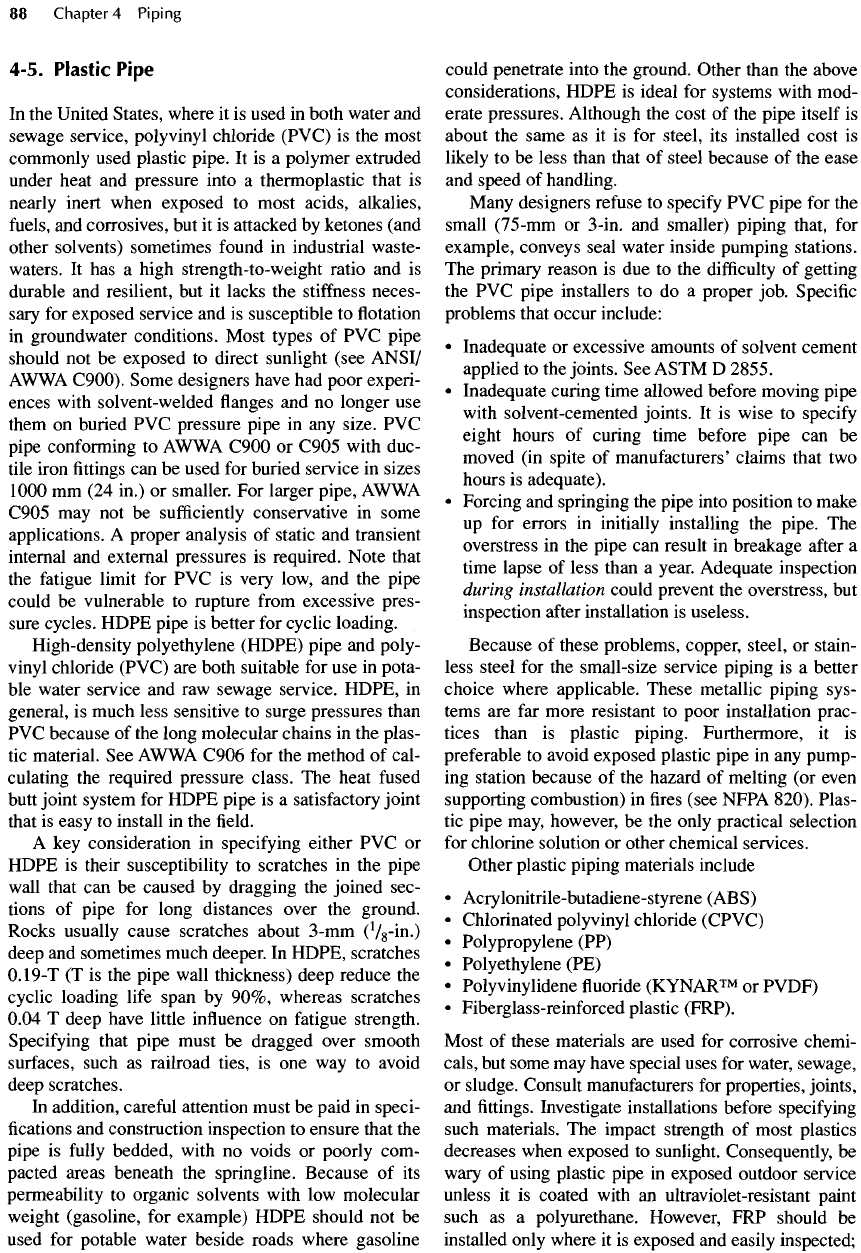
4-5.
Plastic
Pipe
In
the
United States, where
it is
used
in
both water
and
sewage service, poly
vinyl
chloride (PVC)
is the
most
commonly
used plastic pipe.
It is a
polymer extruded
under
heat
and
pressure into
a
thermoplastic that
is
nearly
inert when exposed
to
most acids, alkalies,
fuels,
and
corrosives,
but it is
attacked
by
ketones
(and
other solvents) sometimes
found
in
industrial waste-
waters.
It has a
high
strength-to-
weight
ratio
and is
durable
and
resilient,
but it
lacks
the
stiffness
neces-
sary
for
exposed service
and is
susceptible
to flotation
in
groundwater conditions. Most types
of PVC
pipe
should
not be
exposed
to
direct sunlight (see ANSI/
AWWA
C900). Some designers have
had
poor experi-
ences
with
solvent-welded
flanges and no
longer
use
them
on
buried
PVC
pressure pipe
in any
size.
PVC
pipe conforming
to
AWWA
C900
or
C905
with duc-
tile iron
fittings
can be
used
for
buried service
in
sizes
1000
mm (24
in.)
or
smaller.
For
larger pipe,
AWWA
C905
may not be
sufficiently
conservative
in
some
applications.
A
proper analysis
of
static
and
transient
internal
and
external pressures
is
required. Note that
the
fatigue
limit
for PVC is
very low,
and the
pipe
could
be
vulnerable
to
rupture
from
excessive pres-
sure
cycles. HDPE pipe
is
better
for
cyclic loading.
High-density
polyethylene (HDPE) pipe
and
poly-
vinyl
chloride (PVC)
are
both suitable
for use in
pota-
ble
water service
and raw
sewage service. HDPE,
in
general,
is
much
less
sensitive
to
surge pressures than
PVC
because
of the
long molecular chains
in the
plas-
tic
material.
See
AWWA
C906
for the
method
of
cal-
culating
the
required pressure class.
The
heat
fused
butt
joint system
for
HDPE pipe
is a
satisfactory joint
that
is
easy
to
install
in the field.
A
key
consideration
in
specifying
either
PVC or
HDPE
is
their susceptibility
to
scratches
in the
pipe
wall
that
can be
caused
by
dragging
the
joined
sec-
tions
of
pipe
for
long distances over
the
ground.
Rocks usually cause scratches about
3-mm
(Vg-ni.)
deep
and
sometimes much deeper.
In
HDPE, scratches
0.19-T
(T is the
pipe wall thickness) deep reduce
the
cyclic loading
life
span
by
90%, whereas scratches
0.04
T
deep have little
influence
on
fatigue
strength.
Specifying
that pipe must
be
dragged over smooth
surfaces,
such
as
railroad ties,
is one way to
avoid
deep scratches.
In
addition,
careful
attention must
be
paid
in
speci-
fications
and
construction inspection
to
ensure that
the
pipe
is
fully
bedded, with
no
voids
or
poorly com-
pacted areas beneath
the
springline. Because
of its
permeability
to
organic solvents with
low
molecular
weight
(gasoline,
for
example) HDPE should
not be
used
for
potable water beside roads where gasoline
could penetrate into
the
ground. Other than
the
above
considerations, HDPE
is
ideal
for
systems with mod-
erate pressures. Although
the
cost
of the
pipe itself
is
about
the
same
as it is for
steel,
its
installed cost
is
likely
to be
less
than that
of
steel because
of the
ease
and
speed
of
handling.
Many
designers
refuse
to
specify
PVC
pipe
for the
small
(75
-mm
or
3
-in.
and
smaller)
piping
that,
for
example, conveys seal water inside pumping stations.
The
primary reason
is due to the
difficulty
of
getting
the PVC
pipe
installers
to do a
proper job. Specific
problems that occur include:
•
Inadequate
or
excessive amounts
of
solvent cement
applied
to the
joints.
See
ASTM
D
2855.
•
Inadequate curing time allowed before moving pipe
with
solvent-cemented joints.
It is
wise
to
specify
eight hours
of
curing time before pipe
can be
moved
(in
spite
of
manufacturers'
claims that
two
hours
is
adequate).
•
Forcing
and
springing
the
pipe into position
to
make
up
for
errors
in
initially installing
the
pipe.
The
overstress
in the
pipe
can
result
in
breakage
after
a
time lapse
of
less
than
a
year. Adequate inspection
during
installation could prevent
the
overstress,
but
inspection
after
installation
is
useless.
Because
of
these problems, copper, steel,
or
stain-
less steel
for the
small-size service piping
is a
better
choice where applicable. These metallic piping sys-
tems
are far
more
resistant
to
poor
installation
prac-
tices than
is
plastic piping. Furthermore,
it is
preferable
to
avoid exposed plastic pipe
in any
pump-
ing
station because
of the
hazard
of
melting
(or
even
supporting combustion)
in fires
(see NFPA 820). Plas-
tic
pipe may, however,
be the
only practical selection
for
chlorine solution
or
other chemical
services.
Other plastic piping materials include
•
Aery
lonitrile-butadiene-
sty
rene
(ABS)
•
Chlorinated polyvinyl chloride (CPVC)
•
Polypropylene (PP)
•
Polyethylene (PE)
•
Polyvinylidene
fluoride
(KYNAR™
or
PVDF)
•
Fiberglass-reinforced plastic (FRP).
Most
of
these materials
are
used
for
corrosive chemi-
cals,
but
some
may
have special uses
for
water, sewage,
or
sludge. Consult manufacturers
for
properties, joints,
and
fittings.
Investigate installations before
specifying
such
materials.
The
impact strength
of
most plastics
decreases when exposed
to
sunlight. Consequently,
be
wary
of
using plastic pipe
in
exposed outdoor service
unless
it is
coated with
an
ultraviolet-resistant paint
such
as a
polyurethane.
However,
FRP
should
be
installed only where
it is
exposed
and
easily inspected;