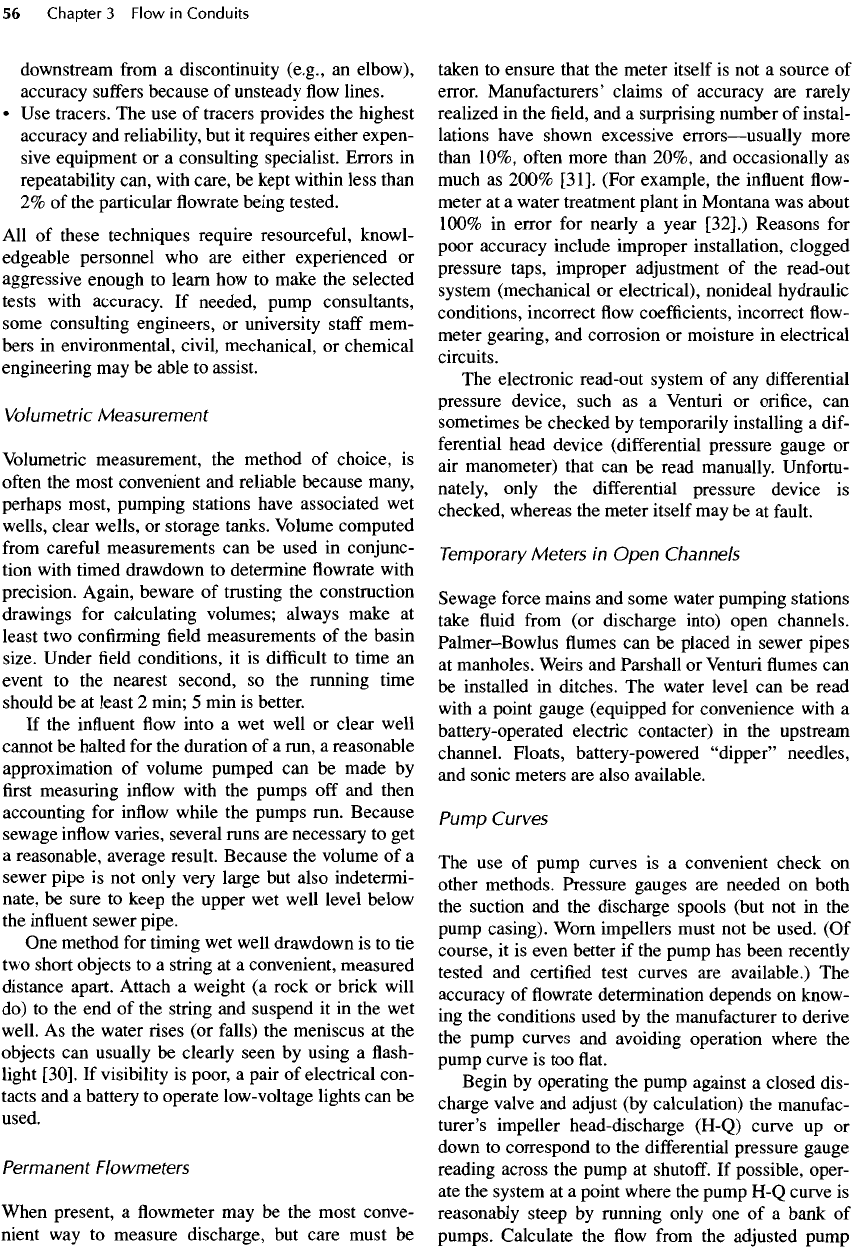
downstream
from
a
discontinuity (e.g.,
an
elbow),
accuracy
suffers
because
of
unsteady
flow
lines.
• Use
tracers.
The use of
tracers provides
the
highest
accuracy
and
reliability,
but it
requires either expen-
sive
equipment
or a
consulting specialist.
Errors
in
repeatability can, with care,
be
kept within less than
2%
of the
particular
flowrate
being tested.
All
of
these techniques require resourceful, knowl-
edgeable personnel
who are
either experienced
or
aggressive enough
to
learn
how to
make
the
selected
tests with accuracy.
If
needed, pump consultants,
some consulting engineers,
or
university
staff
mem-
bers
in
environmental, civil, mechanical,
or
chemical
engineering
may be
able
to
assist.
Volumetric
Measurement
Volumetric
measurement,
the
method
of
choice,
is
often
the
most convenient
and
reliable
because
many,
perhaps most, pumping stations have associated
wet
wells, clear wells,
or
storage tanks. Volume computed
from
careful
measurements
can be
used
in
conjunc-
tion
with timed drawdown
to
determine
flowrate
with
precision. Again, beware
of
trusting
the
construction
drawings
for
calculating volumes; always make
at
least
two
confirming
field
measurements
of the
basin
size. Under
field
conditions,
it is
difficult
to
time
an
event
to the
nearest second,
so the
running time
should
be at
least
2
min;
5
min
is
better.
If
the
influent
flow
into
a wet
well
or
clear well
cannot
be
halted
for the
duration
of a
run,
a
reasonable
approximation
of
volume pumped
can be
made
by
first
measuring
inflow
with
the
pumps
off and
then
accounting
for
inflow
while
the
pumps run. Because
sewage
inflow
varies, several runs
are
necessary
to get
a
reasonable, average result. Because
the
volume
of a
sewer
pipe
is not
only very large
but
also indetermi-
nate,
be
sure
to
keep
the
upper
wet
well level below
the
influent
sewer pipe.
One
method
for
timing
wet
well drawdown
is to tie
two
short objects
to a
string
at a
convenient, measured
distance apart. Attach
a
weight
(a
rock
or
brick will
do) to the end of the
string
and
suspend
it in the wet
well.
As the
water
rises (or
falls)
the
meniscus
at the
objects
can
usually
be
clearly seen
by
using
a flash-
light
[3O].
If
visibility
is
poor,
a
pair
of
electrical
con-
tacts
and a
battery
to
operate low-voltage lights
can be
used.
Permanent
Flowmeters
When
present,
a flowmeter may be the
most conve-
nient
way to
measure discharge,
but
care must
be
taken
to
ensure that
the
meter itself
is not a
source
of
error.
Manufacturers' claims
of
accuracy
are
rarely
realized
in the field, and a
surprising number
of
instal-
lations have shown excessive
errors
—
usually
more
than
10%,
often
more than 20%,
and
occasionally
as
much
as
200%
[31].
(For example,
the
influent
flow-
meter
at a
water treatment plant
in
Montana
was
about
100%
in
error
for
nearly
a
year
[32].)
Reasons
for
poor accuracy include improper installation, clogged
pressure taps, improper adjustment
of the
read-out
system
(mechanical
or
electrical), nonideal hydraulic
conditions,
incorrect
flow
coefficients, incorrect
flow-
meter gearing,
and
corrosion
or
moisture
in
electrical
circuits.
The
electronic
read-out system
of any
differential
pressure device, such
as a
Venturi
or
orifice,
can
sometimes
be
checked
by
temporarily installing
a
dif-
ferential
head device (differential pressure gauge
or
air
manometer) that
can be
read manually. Unfortu-
nately, only
the
differential pressure device
is
checked, whereas
the
meter itself
may be at
fault.
Temporary
Meters
in
Open
Channels
Sewage force mains
and
some water pumping stations
take
fluid
from
(or
discharge into) open channels.
Palmer-Bowlus
flumes can be
placed
in
sewer pipes
at
manholes. Weirs
and
Parshall
or
Venturi
flumes can
be
installed
in
ditches.
The
water level
can be
read
with
a
point gauge (equipped
for
convenience with
a
battery-operated electric contacter)
in the
upstream
channel. Floats, battery-powered
"dipper"
needles,
and
sonic meters
are
also available.
Pump
Curves
The use of
pump curves
is a
convenient check
on
other methods. Pressure gauges
are
needed
on
both
the
suction
and the
discharge spools (but
not in the
pump
casing). Worn
impellers
must
not be
used.
(Of
course,
it is
even better
if the
pump
has
been recently
tested
and
certified test curves
are
available.)
The
accuracy
of flowrate
determination depends
on
know-
ing
the
conditions used
by the
manufacturer
to
derive
the
pump curves
and
avoiding operation where
the
pump curve
is too flat.
Begin
by
operating
the
pump against
a
closed dis-
charge valve
and
adjust
(by
calculation)
the
manufac-
turer's impeller head-discharge (H-Q) curve
up or
down
to
correspond
to the
differential
pressure gauge
reading across
the
pump
at
shutoff.
If
possible,
oper-
ate the
system
at a
point where
the
pump
H-Q
curve
is
reasonably steep
by
running only
one of a
bank
of
pumps. Calculate
the flow
from
the
adjusted pump