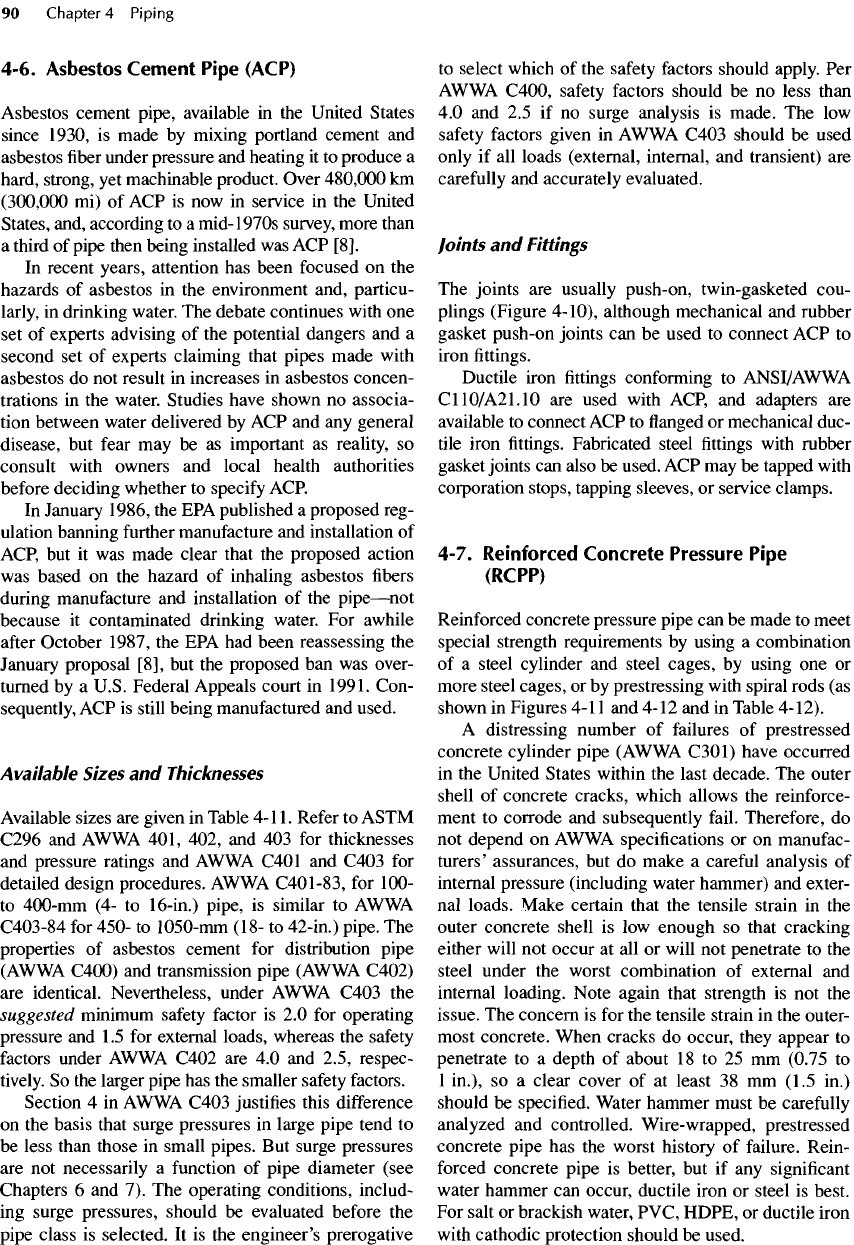
4-6. Asbestos Cement
Pipe
(ACP)
Asbestos cement pipe, available
in the
United States
since 1930,
is
made
by
mixing
portland
cement
and
asbestos
fiber
under pressure
and
heating
it to
produce
a
hard, strong,
yet
machinable product. Over
480,000
km
(300,000
mi) of ACP is now in
service
in the
United
States, and, according
to a
mid-1970s
survey, more than
a
third
of
pipe then being installed
was ACP
[8].
In
recent years, attention
has
been
focused
on the
hazards
of
asbestos
in the
environment and, particu-
larly,
in
drinking water.
The
debate continues with
one
set of
experts advising
of the
potential dangers
and a
second
set of
experts claiming that pipes made with
asbestos
do not
result
in
increases
in
asbestos concen-
trations
in the
water. Studies have shown
no
associa-
tion
between water delivered
by ACP and any
general
disease,
but
fear
may be as
important
as
reality,
so
consult
with
owners
and
local health authorities
before deciding whether
to
specify
ACP.
In
January 1986,
the EPA
published
a
proposed reg-
ulation
banning
further
manufacture
and
installation
of
ACP,
but it was
made clear that
the
proposed action
was
based
on the
hazard
of
inhaling asbestos
fibers
during
manufacture
and
installation
of the
pipe
—
not
because
it
contaminated drinking water.
For
awhile
after
October 1987,
the EPA had
been reassessing
the
January
proposal [8],
but the
proposed
ban was
over-
turned
by a
U.S. Federal Appeals court
in
1991.
Con-
sequently,
ACP is
still being manufactured
and
used.
Available
Sizes
and
Thicknesses
Available
sizes
are
given
in
Table
4-11.
Refer
to
ASTM
C296
and
AWWA
401, 402,
and 403 for
thicknesses
and
pressure ratings
and
AWWA
C401
and
C403
for
detailed design procedures.
AWWA
C401-83,
for
100-
to
400-mm
(4- to
16-in.)
pipe,
is
similar
to
AWWA
C403-84
for
450-
to
1050-mm
(18-
to
42-in.) pipe.
The
properties
of
asbestos cement
for
distribution pipe
(AWWA
C400)
and
transmission pipe
(AWWA
C402)
are
identical. Nevertheless, under
AWWA
C403
the
suggested
minimum
safety
factor
is 2.0 for
operating
pressure
and
1
.5
for
external loads, whereas
the
safety
factors
under
AWWA
C402
are 4.0 and
2.5, respec-
tively.
So the
larger pipe
has the
smaller
safety
factors.
Section
4 in
AWWA
C403
justifies
this
difference
on
the
basis that surge pressures
in
large pipe tend
to
be
less than those
in
small pipes.
But
surge pressures
are not
necessarily
a
function
of
pipe diameter (see
Chapters
6 and 7). The
operating conditions, includ-
ing
surge pressures, should
be
evaluated before
the
pipe class
is
selected.
It is the
engineer's prerogative
to
select
which
of the
safety
factors should apply.
Per
AWWA
C400,
safety
factors should
be no
less than
4.0 and 2.5 if no
surge analysis
is
made.
The low
safety
factors given
in
AWWA
C403 should
be
used
only
if all
loads (external, internal,
and
transient)
are
carefully
and
accurately evaluated.
Joints
and
Fittings
The
joints
are
usually push-on, twin-gasketed cou-
plings (Figure 4-10), although mechanical
and
rubber
gasket push-on joints
can be
used
to
connect
ACP to
iron
fittings.
Ductile iron
fittings
conforming
to
ANSI/AWWA
C110/A21.10
are
used with ACP,
and
adapters
are
available
to
connect
ACP to flanged or
mechanical duc-
tile iron
fittings.
Fabricated steel
fittings
with rubber
gasket joints
can
also
be
used.
ACP may be
tapped with
corporation stops, tapping sleeves,
or
service clamps.
4-7.
Reinforced
Concrete Pressure
Pipe
(RCPP)
Reinforced concrete pressure pipe
can be
made
to
meet
special strength requirements
by
using
a
combination
of
a
steel
cylinder
and
steel
cages,
by
using
one or
more steel cages,
or by
prestressing
with spiral rods
(as
shown
in
Figures
4-11
and
4-12
and in
Table
4-12).
A
distressing number
of
failures
of
prestressed
concrete cylinder pipe
(AWWA
C301)
have occurred
in
the
United States within
the
last decade.
The
outer
shell
of
concrete cracks, which allows
the
reinforce-
ment
to
corrode
and
subsequently
fail.
Therefore,
do
not
depend
on
AWWA
specifications
or on
manufac-
turers' assurances,
but do
make
a
careful
analysis
of
internal pressure (including water hammer)
and
exter-
nal
loads. Make certain that
the
tensile strain
in the
outer concrete shell
is low
enough
so
that cracking
either will
not
occur
at all or
will
not
penetrate
to the
steel under
the
worst combination
of
external
and
internal loading. Note again that strength
is not the
issue.
The
concern
is for the
tensile strain
in the
outer-
most concrete. When cracks
do
occur, they appear
to
penetrate
to a
depth
of
about
18 to 25 mm
(0.75
to
1
in.),
so a
clear cover
of at
least
38 mm
(1.5 in.)
should
be
specified. Water hammer must
be
carefully
analyzed
and
controlled. Wire-wrapped, prestressed
concrete
pipe
has the
worst history
of
failure. Rein-
forced
concrete pipe
is
better,
but if any
significant
water hammer
can
occur, ductile iron
or
steel
is
best.
For
salt
or
brackish water, PVC, HDPE,
or
ductile iron
with
cathodic protection should
be
used.