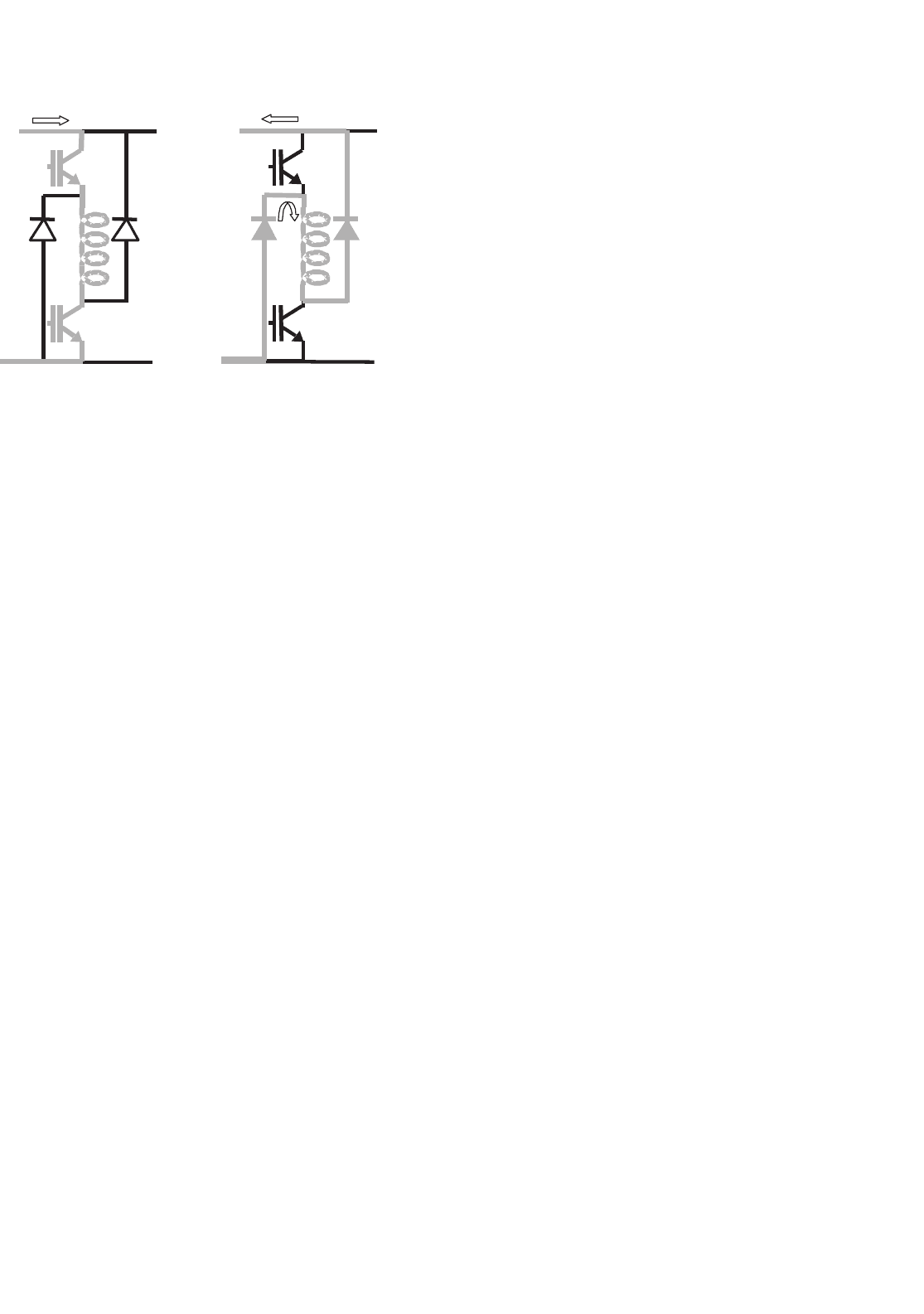
33 Motor Drives 925
+V
dc
T
1
D
2
D
1
T
2
0
i
+V
dc
T
1
D
2
D
1
T
2
0
i
i
(b)(a)
FIGURE 33.108 Hard-chopping mode conduction paths: (a) both
devices on: positive voltage applied to motor phase and (b) T1 and T2
turned off: negative voltage applied to motor phase.
the rising-inductance region. This means that even if a phase
is excited, the current in the motor phase will not increase
in the rising-inductance region. Therefore, at higher speeds,
the turn-on angle must be placed before the beginning of
the increasing inductance region, so that the phase current
will have an adequate time to increase before the back-emf
becomes high.
In addition, the time available for the current to rise after
turn-on becomes less and less as the speed of the motor
increases. This is due to the fact that the available conduc-
tion time is lower for constant switching angles as the speed of
rotation increases. This can be seen by considering that speed
is the time rate of change of angle. Thus, as the speed increases,
there will be a point when the current level never rises to the
chopping level. At this point, the single-pulse mode of oper-
ation will come into effect and the current will decrease or
remain constant throughout the increasing-inductance zone.
An example of a single-pulse mode current waveform was seen
in Fig. 33.105b.
As the current is not commutated in the single-pulse mode,
the control in this mode consists only of controlling the on and
off angles. The turn-on angle θ
on
can be placed at some point
in advance of the rising-inductance region where the phase
inductance is low, so that the current can increase at a faster
rate before the increasing-inductance region. The angle can be
advanced up until maximum allowable current occurs at the
peak of the waveform (this may even mean switching on in
the previous decreasing-inductance zone). The actual control
turn-on and turn-off angles for the single-pulse mode, for a
given load torque and speed, can be determined by simulating
the motor equations.
The speed at which a changeover between single-pulse and
chopping-mode occurs is called the base speed. Base speed is
defined as the highest speed at which the chopping mode can
be maintained at the rated voltage and with fixed on and
off angles. Below the base speed, the current increases dur-
ing the rising-inductance region, unless it is maintained at the
maximum or a lower level by chopping.
Therefore, it can be seen that at lower speeds that are below
the base speed, the motor is controlled using chopping-mode
control, whereas at speeds above the base speed, the single
pulse mode of control is used. In both the control modes,
the control turn-on and turn-off angles are chosen so that the
motor provides the required load torque.
33.9.8 Position Sensing
It can be seen from the preceding discussion that to control
the SR motor satisfactorily, the motor phases are excited at the
rotor angles determined by the control method. It is therefore
essential to have knowledge of the rotor position. Furthermore,
the rotor-angle information must be accurate and have high
resolution to allow implementation of the more sophisticated
nonlinear control schemes that can minimize torque ripple
and optimize the motor performance.
This means that the performance of an SR drive depends on
the accurate position sensing. The efficiency of the drive and
its torque output can be greatly decreased by the inaccurate
position sensing, and the corresponding inaccurate excitation
angles. It has been demonstrated that at high motor speeds, an
error of only 1
◦
may decrease the torque production by almost
8% of the maximum torque output.
Traditionally, the rotor-position information has been mea-
sured using some form of mechanical angle transducer or
encoder. The position-sensing requirements are in fact similar
to those for brushless PM motors. However, although position
sensing is required for the motor operation, the position-
measurement sensors are often undesirable. The disadvantages
of the electromechanical sensors include the following:
(a) The position sensors have a tendency to be unreliable
because of environmental factors such as dust, high
temperature, humidity, and vibration.
(b) The cost of the sensors rises with the position resolu-
tion. Hence, if high-performance control is required,
an expensive high-resolution encoder needs to be
employed.
(c) There is an additional manufacturing expense and
inconvenience due to the sensor installation on the
motor shaft. In addition, consideration must be given
to maintenance of the motor because of the mechan-
ical mounting of the sensors, which also adds to the
design time and cost.
(d) Mechanical position sensors entail extra electrical
connections to the motor. This increases the quan-
tity of electrical wiring between the motor and the
motor drive. This wire normally needs to be shielded