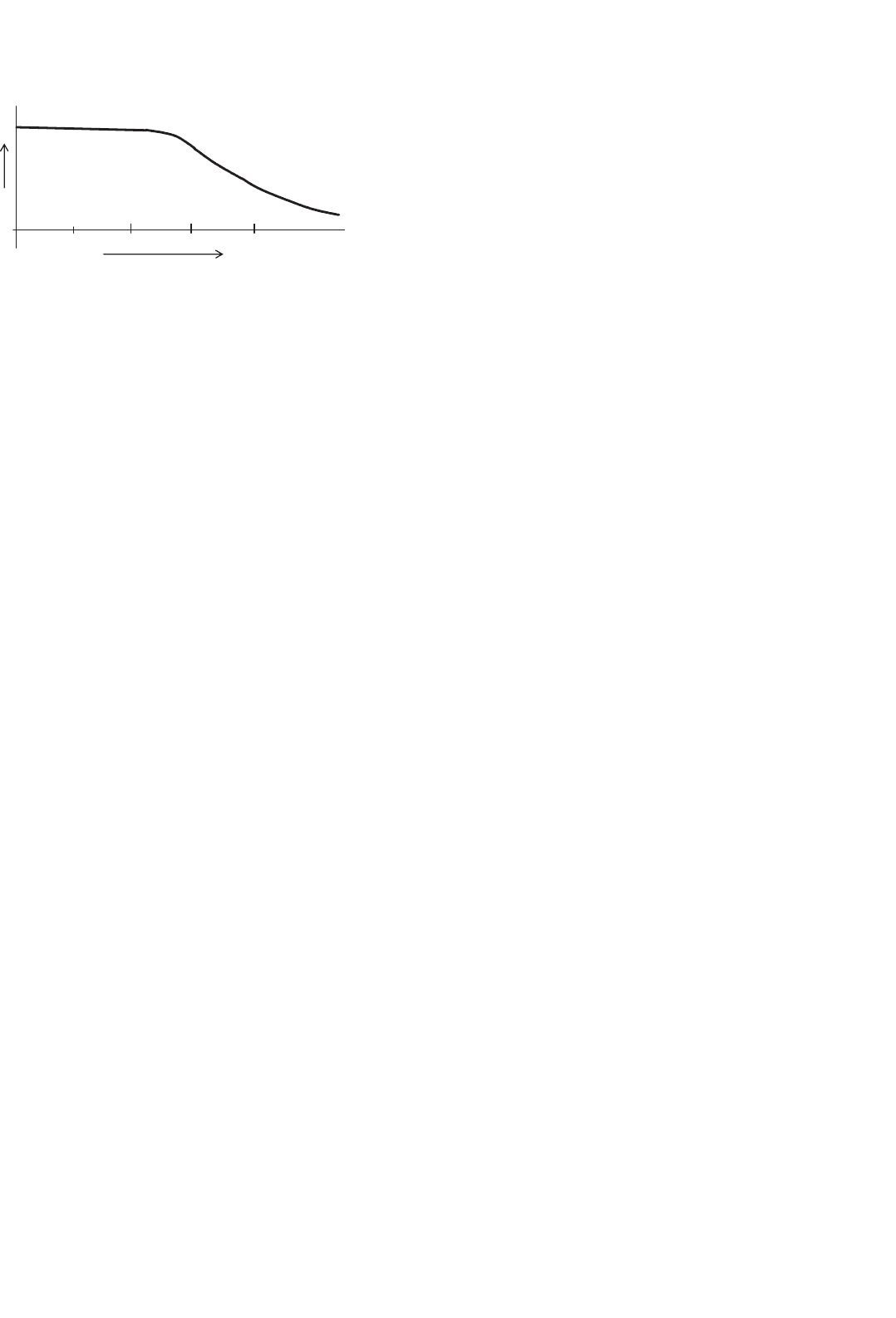
912 M. F. Rahman et al.
Ste
in
rate in ste
s/sec
Pull-out
torque, Nm
10
10,0001000 100
FIGURE 33.89 Typical pull-out torque characteristic of a stepper
motor.
This characteristic indicates the maximum average torque, the
motor may develop while stepping continuously at a given
rate. This torque is also largely determined by the parameters
of the motor and its drive circuits. Figure 33.89 indicates the
typical shape of the pull-out T–ω characteristic of a stepper
motor drive.
At low speed, the pull-out torque is roughly equal to the
average value of the positive half-cycle of the T–θ waveforms of
Fig. 33.82. At high speed, the finite but fixed rise and fall times
of the currents and the back-emf of the winding reduces the
extent to which the windings are energized during each switch-
ing period. Consequently, the pull-out torque of the motors
falls as the stepping rate (speed) increases.
For operation at high speed, the stepping rate is gradually
increased and decreased from one speed to another. With-
out careful acceleration and deceleration to and from a high
speed, the motor will not be able to follow the stepping com-
mands and will lose its synchronism with the stepping pulses
or winding excitations. The acceleration and deceleration rates
of a stepper motor are also determined largely by the pull-out
torque characteristic.
Stepper motors are known to suffer from mechanically
induced resonance and consequent mis-stepping when its
switching rate falls within certain bands, which are largely
determined by the way the developed torque varies with
time, as the motor steps. Careful selection of stepping rate
is normally employed to overcome the problem. Some shaft-
mounted external damping measures may also be used when
the stepping rate needs to be continuously varied, such as in
the case of machine-tool profile following.
33.8.5 Drive Circuits
Two types of drive circuits are in general use for stepper
motors. The unipolar drive is suitable for variable-reluctance
stepper motors, for which the developed torque is deter-
mined by the level of current, not its polarity. For hybrid
and permanent-magnet motors, the direction of current is also
important, so that the bipolar drive circuits are more suitable.
33.8.5.1 Unipolar Drive Circuits
In its simplest form, the unipolar drive circuits, one for
each winding, are as indicated in Fig. 33.90. The transistor
(MOSFET) is turned on to energize the winding, with a current
that is limited either by the winding resistance or by hysteresis
or PWM current controllers. The freewheeling diode allows
the winding current a circulating path when the transistor is
turned off.
The drive circuit of Fig. 33.90a is a basic one. A better drive
circuit is shown in Fig. 33.90b, which includes a zener diode
in the freewheeling path. A pulse-width modulator is also
included in the gate driving circuit. The pulse-width mod-
ulator allows a higher dc supply voltage (typically 5–10 times
the voltage for the resistance-limited drive) to be used, thereby
reducing the rise time of current at switch-on by 5–10 times.
The zener diode allows a fast fall time for the current when the
transistor is turned off by dissipating the trapped energy of the
winding at switch-off faster. Yet another scheme is shown in
Fig. 33.90c which allows the trapped energy of the winding at
switch-off to be returned to the dc source when the transistor
is turned off, rather than being dissipated in the winding or
the freewheeling circuits. This circuit is by far the most effi-
cient, and at the same time gives the fastest possible rise and
fall times for the winding currents.
33.8.5.2 Bipolar Drive Circuits
The bipolar drive allows the motor windings to be driven
with bidirectional currents. The four-transistor bridge drive
circuit of Fig. 33.91, one for each winding, is the most popu-
lar. The circuit can cater to the required rise and fall times of
the winding by properly selecting the dc supply voltage V
dc
,
the pulse-width modulator, and the current controller gains.
Some hybrid and PM motors come with four windings, two
for each phase. These may be connected in series or parallel,
depending on the torque characteristics desired. In any case,
only two drive circuits of the type indicated in Fig. 33.91 are
required.
33.8.5.3 Drive Circuits for Bifilar Wound Motors
Hybrid stepping motors may also come with bifilar windings,
which allow the simpler unipolar drive circuits to be used.
These motors have two tightly coupled windings for each
phase. Figure 33.92 illustrates two bifilar windings on stator
pole and their unipolar drives. The two windings on each pole
have opposite sense, so that the magnetic polarity is reversed by
simply switching the other winding. Since only unidirectional
current is involved, the unipolar drive circuits of Fig. 33.90a
or b may be used at a considerable savings in terms of the drive
circuits. This benefit is, however, derived at the cost of extra
winding space, and hence larger volume, for the same torque.