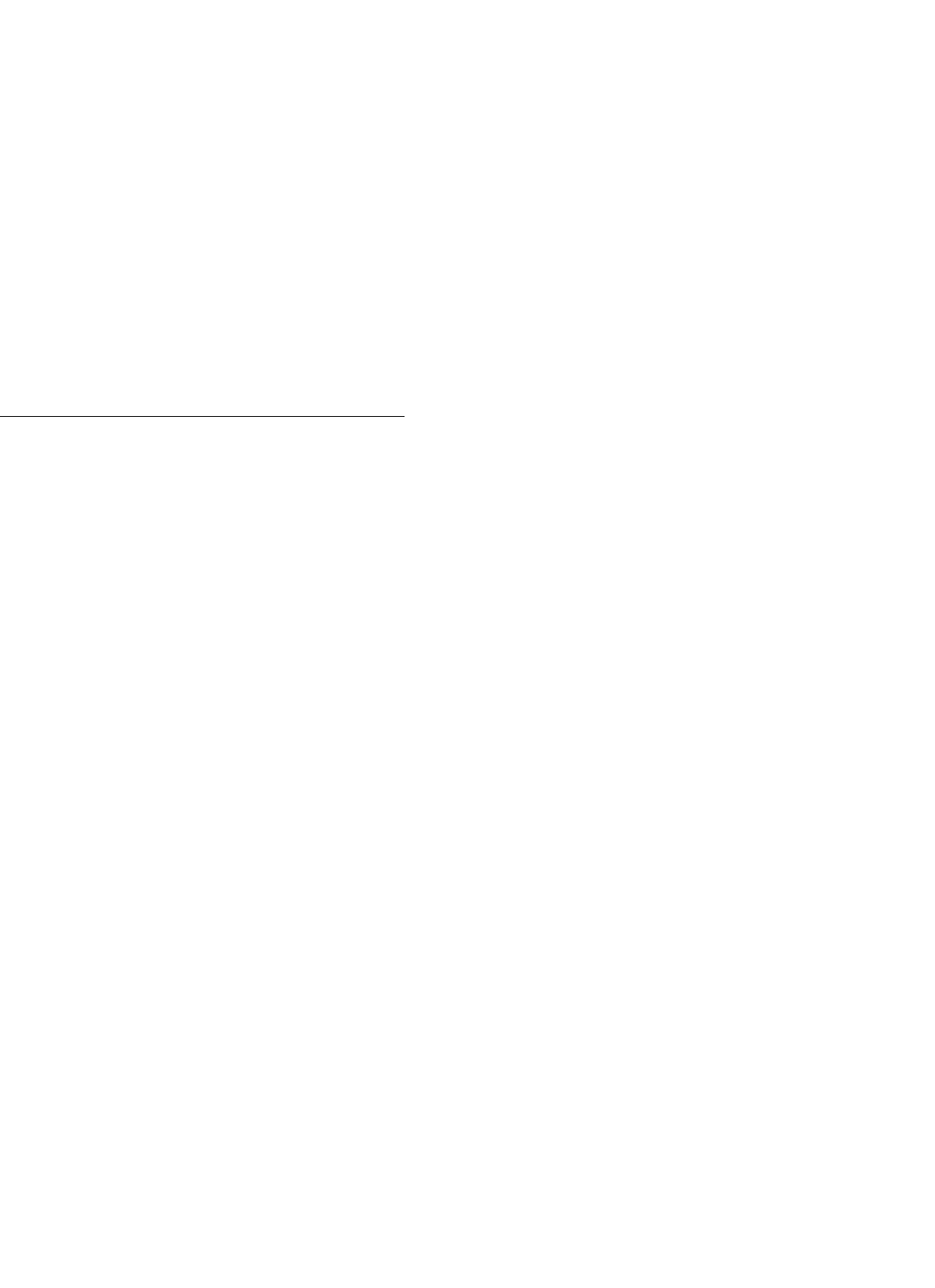
902 M. F. Rahman et al.
following the discussion in the first part of Section 33.6.3,
Current/Torque Control about H bridge switching, prepare the
logic tables again for full bidirectional control, using the I up
and I down logic signals exactly as above, but applying them to
both “legs” determined by the rotor position. Only one form
of current sensing was discussed in detail. There are many sim-
pler schemes in use which do not have quite the flexibility and
accuracy of the above, but which can suit certain applications.
Similarly, there are other forms of current control such as
the constant-frequency linear method briefly discussed. Shaft
position sensors take many forms. Adherence to the HE sensor
was for simplicity, and to reinforce the magnetic field aspects
of the machine operation.
33.7 Servo Drives
33.7.1 Introduction
Servo drives are motor drives that operate with high dynamic
response. Historically, servo drives have implied motion-
control systems in which sophisticated motor design, drive,
and control techniques have been employed to obtain very
much shorter positioning times than is possible with con-
ventional drive systems. Examples are in machine tool drives,
robotic actuators, computer disk drives, and so on. The power
range for these drives has typically been in the range of a few
kilowatts or less. This range has steadily increased in recent
years as a result of advances in magnetic materials, machine
design, power and signal electronic devices, and sensors.
Apart from the fast positioning times, “high dynamic
response” also means that the drive operates with the follow-
ing:
1. Very smooth torque up to a very low speed,
2. Very high reliability and little maintenance,
3. Immunity from load disturbances.
The last of the foregoing items is brought about by robust
and intelligent control algorithms; the first two items are
brought about by innovative and often costly motor and con-
troller designs. As a result of these, the cost of a servo motor
drive is usually much higher than the equivalent power rated
industrial drives.
The distinctions just mentioned may be easily recognized
by noting, for example, that the drives that bring material to
a mill may not require high performance, but the drives that
take part in shaping, milling, or reducing the material should
have high dynamic response in order to increase throughput
and meet the accuracy requirements of the final product.
33.7.2 Servo Drive Performance Criteria
The performance of a servo drive can be expressed in terms
of a number or factors such as servo bandwidth, accuracy,
percentage regulation, and stiffness. While servo bandwidth
indicates the ability of the drive to track a moving or cyclic
reference, the percentage regulation and stiffness stipulates the
drive’s static holding performance for speed or position, in the
face of disturbances from the load and in the supply condi-
tions. The servo bandwidth, specified as a frequency in Hertz
or rad/sec, is often found from the system frequency response
plot, such as the Bode diagram.
The percentage regulation of a speed-controlled system
often refers to the percentage change in speed from no load
to full load. In a type-zero system, this figure will have a finite
value. Many systems are type zero, albeit with a high gain so
that the regulation is acceptably low. For such systems, the
regulation is often necessary for operational reasons. In some
applications, zero percentage error is required, which calls for
type 1 or integral type control system.
The servo stiffness is similar to the percentage error men-
tioned earlier, but it applies mainly for the position servo. It
specifies the deflection of the load from its reference position,
when full load torque is applied. It is usually the slope of the
deflection versus the applied load torque in rad/Nm around
the reference position.
33.7.3 Servo Motors, Shaft Sensors, and
Coupling
Servo drives use motors which allow the desired goals of high
dynamic response to be achieved. The important parameters/
attributes of a servo motor are:
1. High torque-to-inertia ratio,
2. High torque-to-volume ratio,
3. Low inductance of the motor windings,
4. Low cogging torque at low speed,
5. Efficient heat dissipation,
6. Low coefficient of shaft compliance,
7. Direct-coupled, high-resolution, shaft-mounted sensors
for position and speed.
High torque-to-inertia ratio allows fast acceleration or
deceleration of the drive when motion references are changed.
This is often achieved through innovative low-inertia rotor
design and low inductance in the stator winding. One example
of a dc servo motor is the pancake printed armature dc motor
with no iron in the rotor, as indicated in Fig. 33.70. The rotor
is sandwiched between axially mounted stator poles. The com-
mutator is also on the printed armature. Another example is
the disk rotor stepping motor, also without iron in the rotor,
as indicated in Fig. 33.71.
The PM ac synchronous motors with modern high-energy-
density magnets in the rotor, as described in Section 33.6, are
also examples where the motor designer strives to minimize the
rotor inertia. Modern permanent magnets allow the required
airgap flux to be developed with a much reduced volume of
the magnets, consequently reducing the diameter of the rotor.