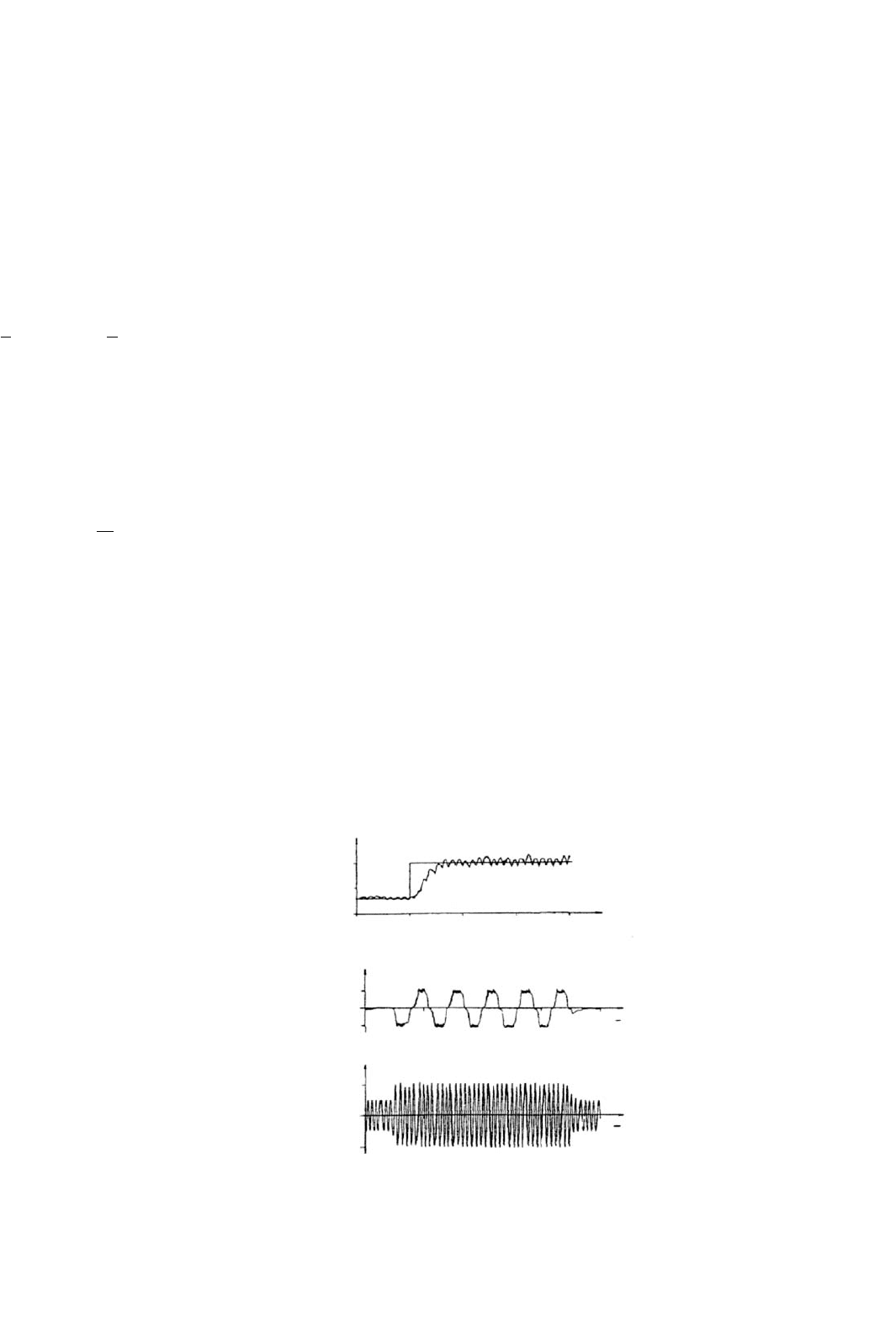
868 M. F. Rahman et al.
The negative sign arises because the thyristor converter
develops negative dc voltage in the inverter mode of oper-
ation. The dc-link inductor is mainly to ensure continuous
current through the converter so that the expression (33.21)
holds for all conditions of operation. Combining the preceding
three equations gives
sω
s
=−ω
s
cos α so that, s =−n cos α
and the rotor speed
ω
o
=
1
P
(
1 −s
)
ω
s
=
1
P
ω
s
(
1 +n cos α
)
rad/s (33.22)
Thus, the motor speed can be controlled by adjusting the
firing angle α. By varying α between 180
◦
and 90
◦
, the speed of
the motor can be varied from zero to full speed, respectively.
For a motor with low rotor resistance and with the assump-
tions taken earlier, it can be shown that the developed torque
of the motor is given by
T = 3P
V
s
ω
s
i
d
≈ 3Pλ
m
i
d
Nm (33.23)
where i
d
is the dc-link current. Thus, the inner torque control
loop of a variable-speed drive using the Scherbius scheme nor-
mally employs a dc-link current loop as the innermost torque
loop. Figure 33.16 shows the transient responses of the dc-
link, rotor and stator currents of such a drive when the motor
is accelerated between two speeds.
The drive is normally started with a short-time-rated liquid
resistor, and the thyristor speed controller is started when the
drive reaches a certain speed.
By replacing the diode rectifier of Fig. 33.16 with another
thyristor bridge, power can be made to flow to and from the
Step response of dc link current
control loop
Rotor current during step change
Stator current during step change
i
D
/A
50
25
0
i
R
/A
50
0
−50
i
S
/A
44
0
−44
025
0.25 0.5 0.75 1.0
t
s
t
s
50 75 100
t/ms
FIGURE 33.16 Transient responses of a slip power controlled drive under acceleration.
rotor circuit, allowing the motor to operate at a rate higher
than synchronous speed. For very large drives, a cycloconverter
may also be used in the rotor circuit with direct conversion of
frequency between the ac supply and the rotor and driving the
motor above and below synchronous speed.
33.3.3.3 Variable-voltage, Variable-frequency (V–f )
Control
33.3.3.3.1 SPWM Inverter Drive When an induction motor
is driven from an ideal ac voltage source, its normal operating
speed is less than 5% below the synchronous speed, which
is determined by the ac source frequency and the number of
motor poles. With a sinusoidally modulated (SPWM) inverter,
indicated in Fig. 33.17, the supply frequency to the motor can
be easily adjusted for variable speed. Equation (33.18) implies
that, if rated airgap flux is to be maintained at its rated value
at all speeds, the supply voltage V
1
to the motor should be
varied in proportion to the frequency f
1
. The block diagram of
Fig. 33.18a shows how the frequency f
1
and the output voltage
V
1
of the SPWM inverter are proportionately adjusted with
the speed reference. The speed reference signal is normally
passed through a filter that only allows a gradual change in
the frequency f
1
. This type of control is widely referred to as
the V–f inverter drive. Control of the stator input voltage V
1
as a function of the frequency f
1
is readily arranged within
the inverter by modulating the switches T
1
–T
6
. At low speed,
however, where the input voltage V
1
is low, most of the input
voltage may drop across the stator impedance, leading to a
reduction in airgap flux and loss of torque.
Compensation for the stator resistance drop, as indicated in
Fig. 33.18b, is often employed. However, if the motor becomes
lightly loaded at low speed, the airgap flux may exceed the rated
value, causing the motor to overheat.