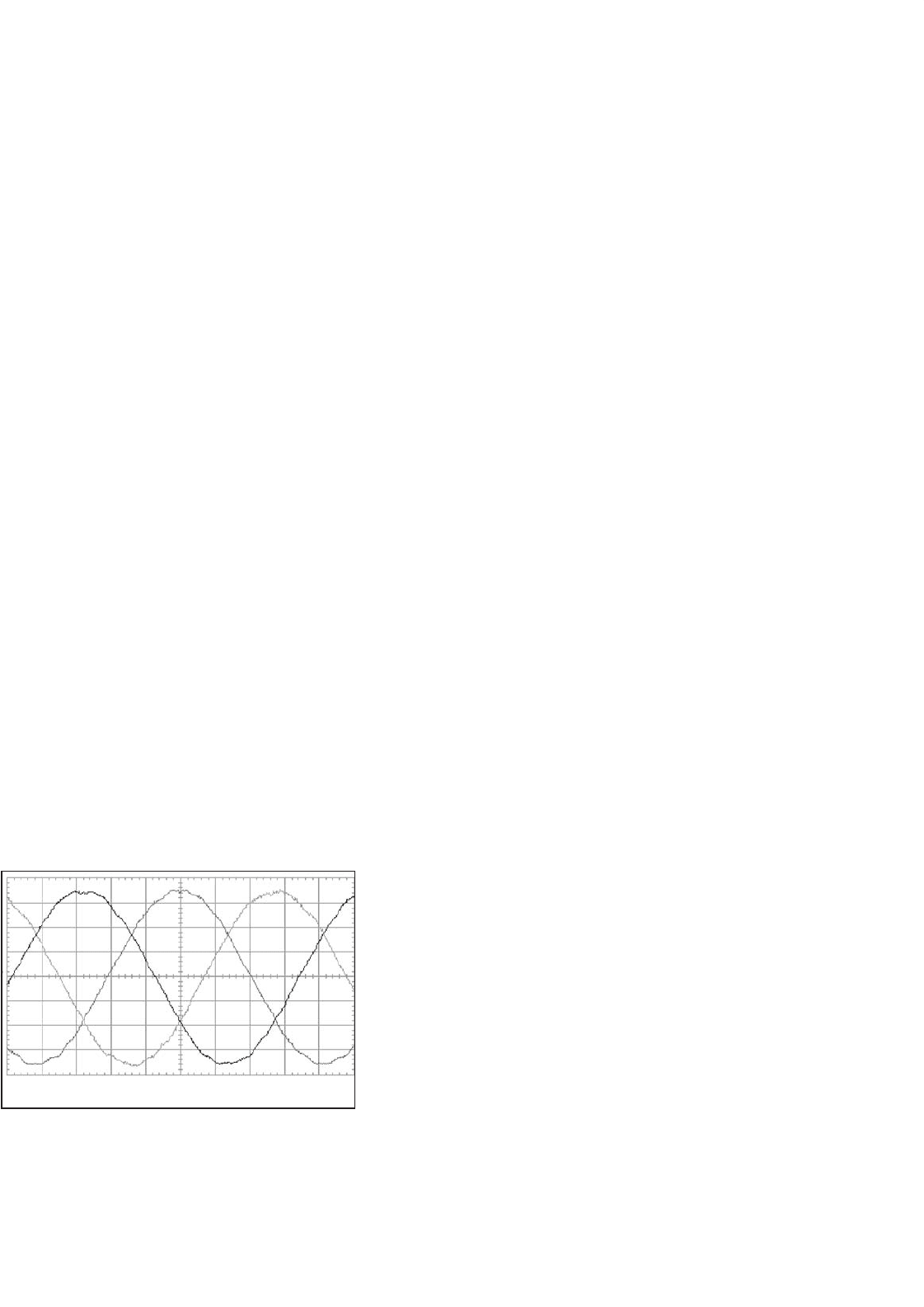
888 M. F. Rahman et al.
33.5.2.2 Sensorless Operation of the PM BLDC Motor
In spindle and other variable-speed drive applications, where
the lowest speed of operation is not less than a few hundred
revs/min, it may be possible to obtain the switching signals for
the inverter from the motor back-emf, thus dispensing with
rotor-position sensors. The method consists of integrating the
back-emf waveforms, which are the same as the applied phase
voltage if the other voltage drops are neglected, and comparing
the integrated outputs with a fixed reference. These compara-
tor outputs determine the switching signals for inverter. It
may be noted that the amplitude of the back-emf waveforms
is proportional to the operating speed, so that the frequency
of the comparator outputs increases automatically with speed.
In other words, the angle γ and the current waveform rel-
ative to the back-emf waveform in each phase remains the
same regardless of the operating speed. Integrated circuits are
available from several suppliers, that perform this task of sen-
sorless BLDC operation satisfactorily, covering a reasonable
speed range.
33.5.3 The PM Sinewave Motor
The PM sinewave motor, which may also have magnets on the
rotor surface or buried inside the rotor (as in the interior-
magnet motor of Fig. 33.46), has sinusoidally distributed
windings. The airgap flux distribution produced by the rotor
magnets is also sinusoidal, arranged through magnet shaping.
Consequently, the back-emf waveform of each phase is also
a sinusoidal waveform, as indicated in Fig. 33.50, when the
motor is driven at a constant speed.
It should be noted, however, that with magnets mounted
on the rotor surface, the effective airgap is large and uniform
so that L
d
= L
q
= L
s
. Because of the large equivalent air-
gap, these inductances are also small, and consequently, the
armature reaction is small. As a result, this motor essentially
operates with fixed excitation, and there is hardly any scope
100 V/div 5 ms/div
FIGURE 33.50 Back-emf waveforms of a sinewave PM motor.
Speed = 1815 rev/min.
for altering the operating power factor or the rotor mmf, once
the motor and its drive voltage and current ratings have been
selected.
The PM sinewave interior-magnet motor, which comes with
magnets buried inside the rotor as indicated in Figs. 33.46 and
33.47, has an easier magnetization path along the rotor q-axis,
so that L
q
> L
d
. The small airgap implies that the inductances
L
d
and L
q
may not be small, and hence may allow considerable
scope for field weakening.
If the sinewave motor is supplied from an SPWM inverter,
the analyses and vector diagrams of this motor are not different
from those in Section 33.4 for the nonsalient-pole and salient-
pole synchronous motor drives. The surface-magnet motor is
more akin to the nonsalient-pole motor, since L
d
= L
q
= L
s
,
whereas the interior-magnet motor is more akin to the salient-
pole motor because of the d- and q-axes inductances being
unequal. Thus, the equations in Section 33.4 will apply equally
well for this motor, both in the steady state and dynamically
and for both voltage- and current-source supply.
33.5.3.1 Control of the PM Sinewave Motor
The sinusoidal back-emf waveforms imply that the three-phase
motor must be supplied with a sinusoidal three-phase currents
if a dc-motor-like (or vector-control-like) torque characteristic
is desired, as was found in Section 33.4. For such operation, the
phase currents must also be synchronized with the respective
phase back-emf waveforms, in other words, with the rotor dq-
reference frame. This implies the operation with a specified γ
angle. Two implementations are possible.
In one scheme, the stator currents are regulated in the stator
reference frame and the stator current references are produced
with reference to the rotor position, as indicated in Fig. 33.51.
The rotor position θ is continuously sensed and used to pro-
duce three sinusoidal current references of unit amplitude.
The phase angle γ of the references relative to the respec-
tive back-emf waveforms is usually derived from the speed
controller, which defines the field-weakening regime of the
drive. The operating power factor of the drive may also be
addressed using the γ angle control, as explained in Section
33.4.5. The amplitudes of these references are then multiplied
by the error of the speed controller in order to produce the
desired torque reference. In this way, both the RMS value I
of the phase current and its angle γ with respect to E
f
can be
adjusted independently (which is equivalent to independent
dq-axes current control). Three PWM current controllers are
indicated, but two suffice for a balanced motor. Other types of
current controllers, such as hysteresis controllers, may also be
used.
In the second scheme, the motor currents are first trans-
formed into the rotor dq-reference frame using continuous
rotor position feedback and the measured rotor d- and q-
axes currents are then regulated in the rotor reference frame,
as indicated in Fig. 33.52. The main advantage of regulating