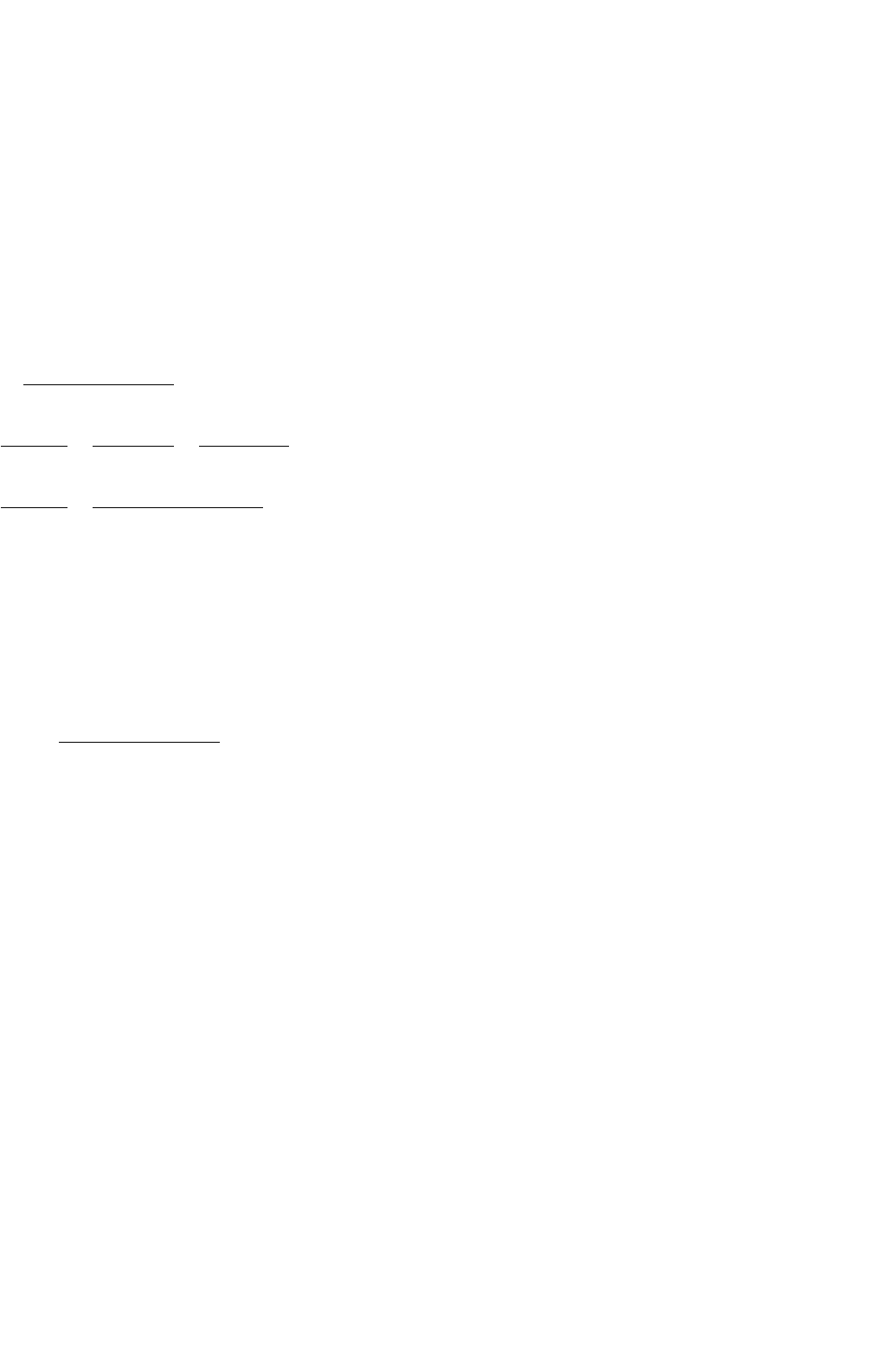
944 J. F. Silva and S. F. Pinto
Proportional–Integral derivative (PID), plus high-frequency
poles
The PID notch filter type (34.52) scheme is used in convert-
ers with two lightly damped complex poles, to increase the
response speed, while ensuring zero steady-state error. In most
switching converters, the two complex zeros are selected to
have a damping factor greater than the converter complex
poles and slightly smaller oscillating frequency. The high-
frequency pole is placed to achieve the needed phase margin
[9]. The design is correct if the complex pole loci, heading to
the complex zeros in the system root locus, never enter the
right half-plane.
C
PIDnf
(s) = T
cp
s
2
+2ξ
cp
ω
0cp
s +ω
2
0cp
s
1 +s/ω
p1
=
T
cp
s
1 +s/ω
p1
+
2T
cp
ξ
cp
ω
0cp
1 +s/ω
p1
+
T
cp
ω
2
0cp
s
1 +s/ω
p1
=
T
cp
s
1 +s/ω
p1
+
T
cp
ω
2
0pc
1 +2sξ
cp
/ω
0cp
s
1 +s/ω
p1
(34.52)
For systems with a high-frequency zero placed at least one
decade above the two lightly damped complex poles, the com-
pensator (34.53), with ω
z1
≈ ω
z2
<ω
p
, can be used. Usually,
the two real zeros present frequencies slightly lower than the
frequency of the converter complex poles. The two high-
frequency poles are placed to obtain the desired phase margin
[9]. The obtained overall performance will often be inferior to
that of the PID type notch filter.
C
PID
(s) = W
cp
(
1 +s/ω
z1
)(
1 +s/ω
z2
)
s
1 +s/ω
p
2
(34.53)
34.2.5.2 Compensator Selection and Design
The procedure to select the compensator and to design its
parameters can be outlined as follows:
1. Compensator selection: In general, since V
DC
per-
turbations exist, null steady-state error guarantee is
needed. High-frequency poles are usually necessary, if
the transfer function shows a −6 dB/octave roll-off due
to high frequency left plane zeros. Therefore, in gen-
eral, two types of compensation schemes with integral
action (34.51 or 34.50), and (34.52 or 34.53) can be
tried. Compensator (34.52) is usually convenient for
systems with lightly damped complex poles;
2. Unity gain frequency ω
0dB
choice:
•
If the selected compensator has no complex zeros,
it is better to be conservative, choosing ω
0dB
well below the frequency of the lightly damped
poles of the converter (or the frequency of the
right half plane zeros if lower). However, because
of the resonant peak of most converter transfer
functions, the phase margin can be obtained at a
frequency near the resonance. If the phase mar-
gin is not enough, the compensator gain must be
lowered;
• If the selected compensator has complex zeros,
ω
0dB
can be chosen slightly above the frequency
of the lightly damped poles;
3. Desired phase margin (φ
M
) specification φ
M
≥ 30
◦
(preferably between 45
◦
and 70
◦
);
4. Compensator zero-pole placement to achieve the
desired phase margin:
• With the integral plus zero-pole compensation
type (34.51), the compensator phase φ
cp
, at the
maximum frequency of unity gain (often ω
0dB
),
equals the phase margin (φ
M
) minus 180
◦
and
minus the converter phase φ
cv
,(φ
cp
= φ
M
−180
◦
−
φ
cv
). The zero-pole position can be obtained cal-
culating the factor f
ct
= tg (π/2 + φ
cp
/2) being
ω
z
= ω
0dB
/f
ct
and ω
M
= ω
0dB
f
ct
.
• With the PID notch filter type (34.52) controller,
the two complex zeros are placed to have a damp-
ing factor equal to two times the damping of
the converter complex poles, and oscillating fre-
quency ω
0cp
30% smaller. The high-frequency pole
ω
p1
is placed to achieve the needed phase margin
(ω
p1
≈ (ω
0cp
·ω
0dB
)
1/2
f
2
ct
with f
ct
= tg(π/2+φ
cp
/2)
and φ
cp
= φ
M
−180
◦
−φ
cv
[5]).
5. Compensator gain calculation (the product of the con-
verter and compensator gains at the ω
0dB
frequency
must be one).
6. Stability margins verification using Bode plots and root
locus.
7. Results evaluation. Restarting the compensator selec-
tion and design, if the attained results are still not good
enough.
34.2.6 Examples: Buck–Boost DC/DC
Converter, Forward DC/DC Converter,
12 Pulse Rectifiers, Buck–Boost DC/DC
Converter in the Discontinuous Mode
(Voltage and Current Mode), Three-phase
PWM Inverters
EXAMPLE 34.4 Feedback design for the buck–boost
dc/dc converter
Consider the converter output voltage v
o
(Fig. 34.1)
to be the controlled output. From Example 34.2 and
Eqs. (34.33) and (34.35), the block diagram of Fig. 34.7 is
obtained. The modulator transfer function is considered
a pure gain (G
M
= 0.1). The magnitude and phase of the